Safety valves, known as صمام الأمان in Arabic, play a crucial role in various industries, safeguarding both equipment and personnel from hazardous situations. Their importance spans through numerous sectors including oil and gas, chemical processing, power generation, and manufacturing. A deep dive into this critical component reveals its essential functions, the expertise required for its maintenance, and best practices for ensuring its reliability and trustworthiness.
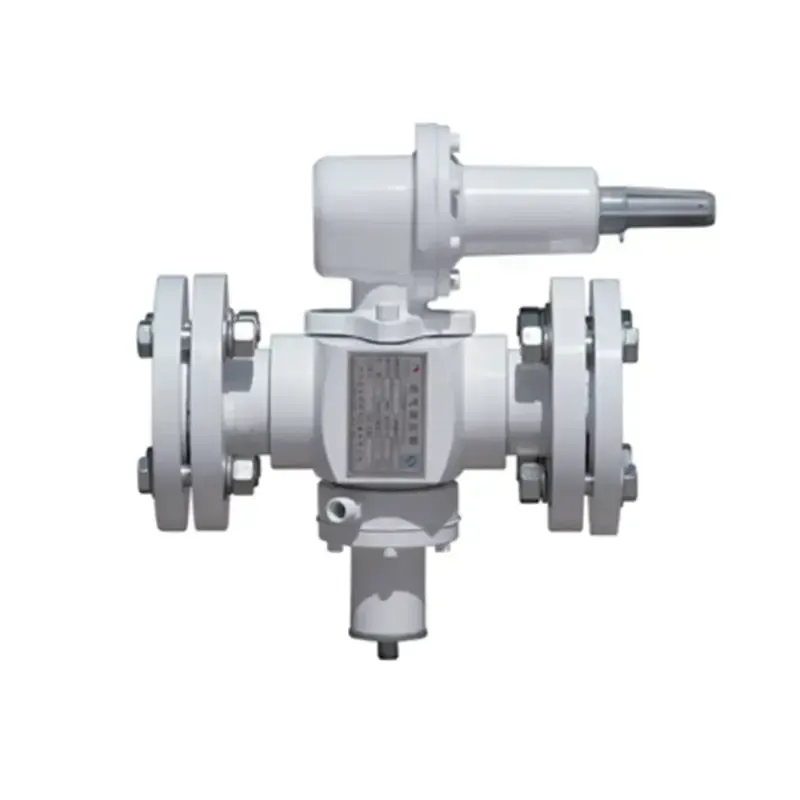
A safety valve is a fail-safe device designed to automatically release substances from a boiler, pressure vessel, or other system when the pressure or temperature exceeds preset limits. This component is different from relief valves, which generally operate gradually, because safety valves are built to open fully and quickly when a specific limit is reached. The precise and immediate relief offered by safety valves minimizes the risks of explosion, equipment failure, and injury, thus ensuring the safety and efficiency of operations.
The technological expertise behind safety valves lies in their design and materials. High-quality safety valves are constructed from durable materials capable of withstanding extreme conditions, including high pressures and corrosive substances. They undergo rigorous testing to meet international standards, such as those set by the American Society of Mechanical Engineers (ASME) or the European Pressure Equipment Directive (PED). Expertise in this field ensures that safety valves not only comply with stringent safety standards but also enhance operational reliability.
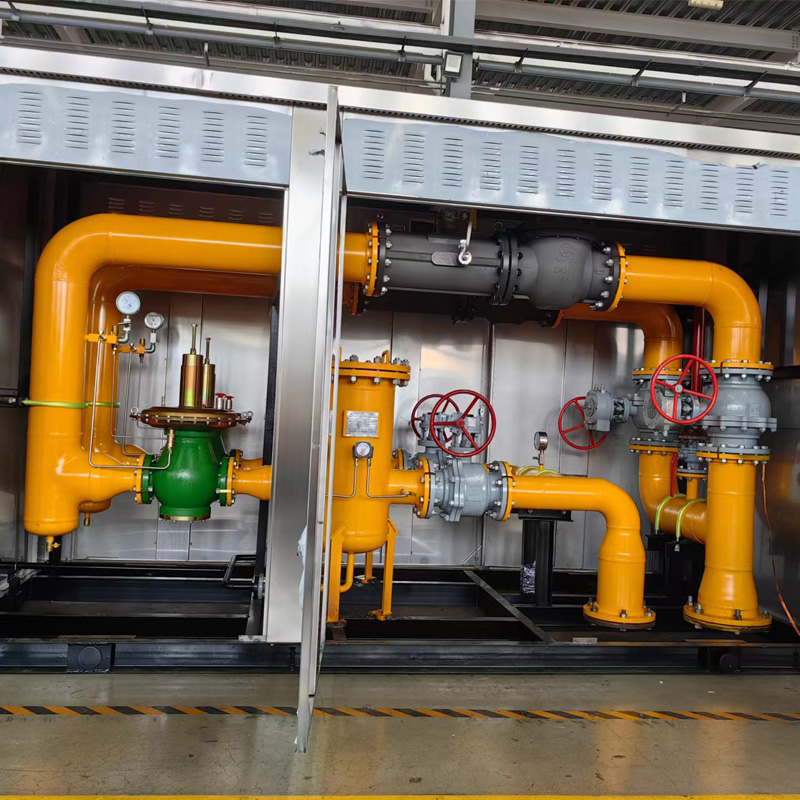
Real-world experience highlights the necessity of regular maintenance and inspection of safety valves. Experienced technicians and engineers emphasize the importance of routine checks to verify the proper operation and detection of wear and tear that could compromise performance. Maintenance typically involves cleaning, recalibrating, and replacing parts if necessary. Regular inspections are crucial in environments where process conditions may lead to deposits or corrosion that affect valve performance. Neglecting these practices can result in catastrophic system failures, underscoring the need for disciplined maintenance schedules.
Safety valve
Authoritative organizations often publish guidelines and best practices for the installation and maintenance of safety valves. These guidelines recommend factors to consider when selecting a valve, such as the type of fluid, pressure, temperature, and the environment in which it will operate. Ensuring that the valve type matches the application prevents common issues such as seat leakage or premature failures. Manufacturers and industry leaders provide training and certification programs to uphold these standards, reinforcing trustworthiness in their products.
Trustworthiness extends to the documentation and traceability of safety valves. Reliable manufacturers offer detailed documentation on each valve's performance, material specifications, and test results. This transparency not only builds customer trust but also aids in troubleshooting and maintenance by providing a comprehensive history of the component.
In conclusion, safety valves are an indispensable part of many industries, providing vital protection against overpressure and temperature extremes. By combining expertise in design, materials, and maintenance with adherence to authoritative standards and practices, industries can ensure these components operate reliably and safely. Maximum trust is achieved through comprehensive documentation and transparency offered by reputable manufacturers, solidifying safety valves as a trustworthy safeguard in any high-pressure application.
Embracing cutting-edge technology and adhering to best practices broadens the application possibilities for safety valves while enhancing their protective capabilities — a testament to their critical role in both industrial safety and process efficiency.