As demand for natural gas continues to rise globally, ensuring the efficient and safe operation of gas systems has become crucial. Natural gas filter separators play an integral role in maintaining the purity and reliability of gas provisions by removing contaminants and protecting downstream equipment.
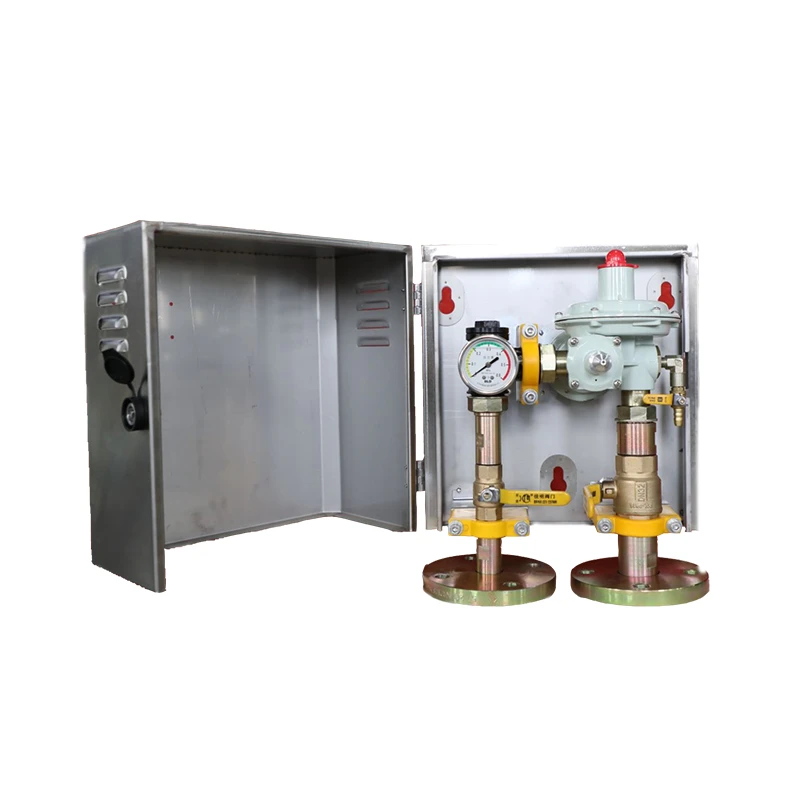
Natural gas filter separators are engineered to address a variety of issues encountered in gas pipelines such as dust, liquid hydrocarbons, water, and other particulate matter. These contaminants pose significant risks, including pipeline corrosion, equipment malfunction, and reduced efficiency of gas transmission. Therefore, a reliable filter separator is essential for any natural gas processing setup.
A diverse array of designs exists to accommodate different operational requirements and environmental conditions. Among the most common types are cartridge and coalescing filters, each with distinct applications. Cartridge filters are primarily used for solid particle removal, employing materials like cellulose or synthetic fibers to trap debris. Coalescing filters, on the other hand, are designed to remove liquid aerosols, using a multi-layered approach to trap liquid droplets and allow them to coalesce into larger droplets for easy drainage.
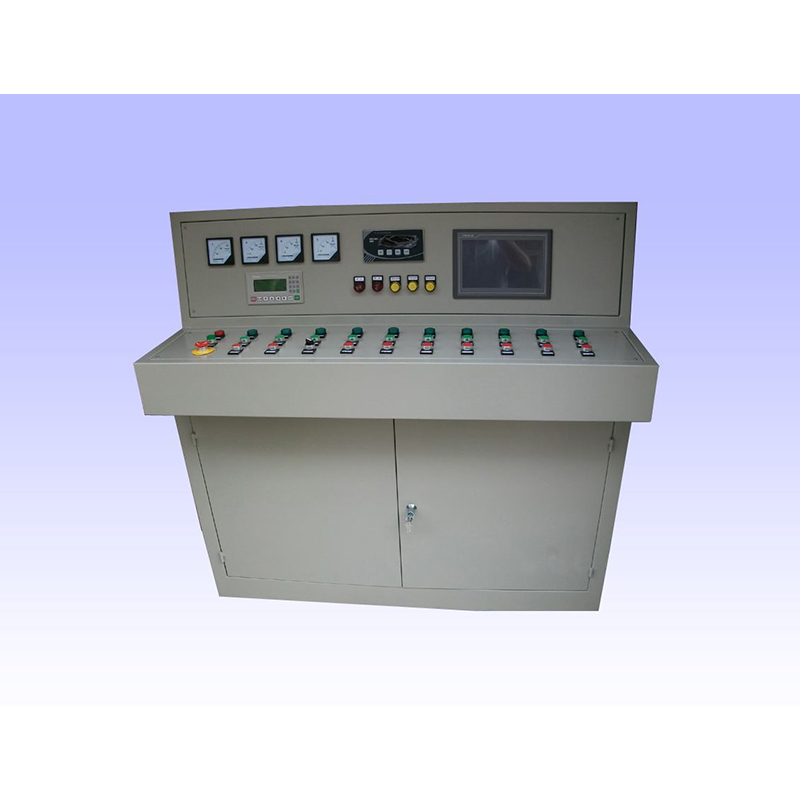
One of the primary benefits of investing in high-quality natural gas filter separators is the enhancement of downstream equipment's lifecycle and performance. By ensuring the gas is consistently clean and free from contaminants, these separators prevent the abrasive and corrosive damage that could otherwise result in costly repairs or downtime. Furthermore, operators can achieve regulatory compliance with environmental standards more efficiently by using filter separators that minimize pollutant emissions.
Natural gas filter separator
Real-world experience provides valuable insights into the operation and maintenance of natural gas filter separators. Industry experts recommend routine inspections and maintenance to ensure optimal performance. This includes regularly checking pressure differentials, inspecting filter mediums for saturation or damage, and replacing elements as needed to maintain efficiency.
Moreover, customization of natural gas filter separators can lead to better alignment with specific operational needs. Companies with unique requirements can work with manufacturers to design bespoke solutions that maximize filtration efficiency while minimizing pressure drops. An example is the use of advanced materials such as stainless steel or advanced polymers in environments with extreme temperatures or corrosive substances.
Choosing the right filter separator is essential for operational success. Factors to consider include the nature of the gas stream, potential contaminant load, expected flow rates, and existing infrastructure. Collaboration with seasoned professionals ensures that these considerations are addressed effectively, resulting in a filtration system that offers optimal performance.
In conclusion, natural gas filter separators are vital to maintaining the purity, reliability, and safety of gas systems. By investing in quality equipment and adhering to regular maintenance protocols, companies can protect their infrastructure, comply with environmental regulations, and ensure a consistent supply of high-quality natural gas. As the industry continues to grow, leveraging the expertise and innovation within the field will be crucial for continued success.