Natural gas safety valves, often known as safety shutdown valves, play a crucial role in ensuring the secure and efficient operation of gas systems worldwide. These devices are designed to control and manage the flow of natural gas, mitigating risks associated with potential leaks or system failures. Their importance cannot be overstated, especially in industrial settings where large volumes of gas are handled regularly.
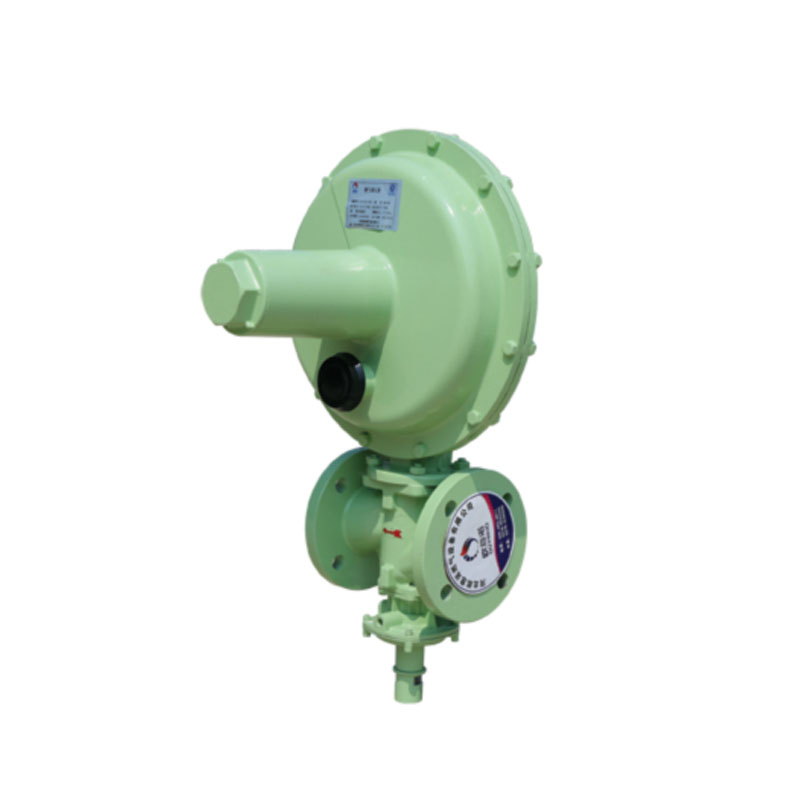
The core function of a natural gas safety valve is to automatically shut off the gas supply in case of a leak or other emergency, reducing the risk of accidents such as explosions or fires. The valve is typically connected to a system of sensors that detect pressure changes, enabling it to respond swiftly to any irregularities. By providing a fail-safe mechanism, these valves help protect both property and human lives, ensuring that any disruption in the gas supply does not escalate into a more serious incident.
The design and engineering behind natural gas safety valves have evolved significantly over the years. Modern valves boast enhanced reliability and precision, owing to advances in materials science and sensor technology. For instance, high-grade stainless steel and advanced composites offer corrosion resistance and durability, making the valves suitable for a wide range of environments. Meanwhile, state-of-the-art sensors ensure accurate detection of pressure anomalies, allowing for quick reaction times in critical situations.
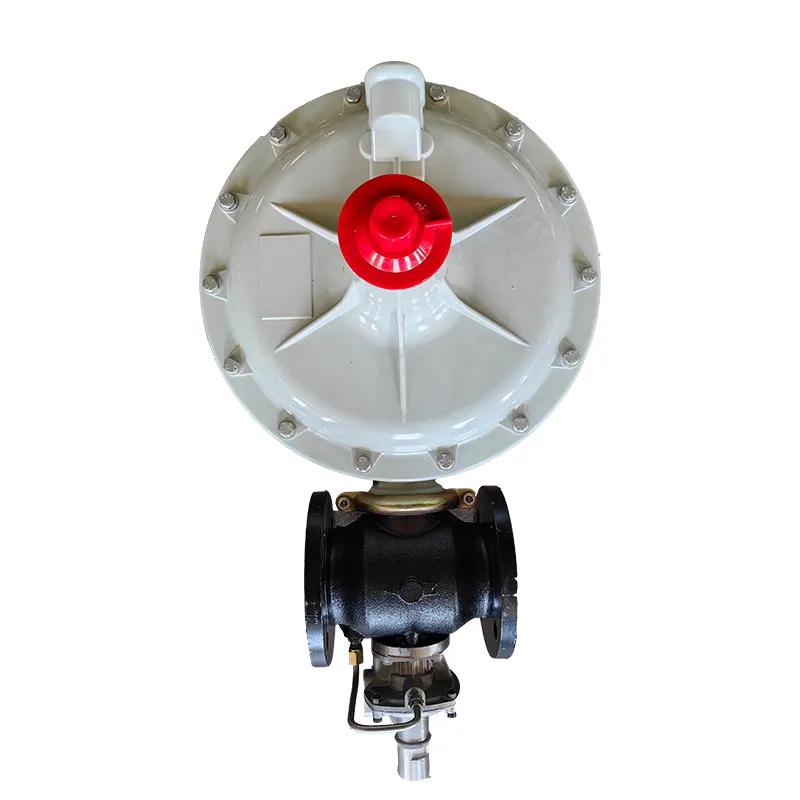
From an expertise standpoint, the installation and maintenance of natural gas safety valves require specialized knowledge and skills. These tasks should only be undertaken by qualified professionals who understand the complexities of gas systems and adhere to industry regulations and standards. Proper installation ensures that the valve functions as intended, while regular maintenance checks are essential to verify its operational integrity and safety.
Natural gas safety valve
Moreover, natural gas safety valves are an integral part of a comprehensive safety strategy in gas management systems. Their deployment is guided by stringent regulatory frameworks that mandate specific protocols for testing and inspection. Compliance with these regulations not only ensures optimal performance of the valves but also fosters a culture of safety and accountability within the organization.
Authoritativeness in the context of natural gas safety valves is reinforced by industry endorsements and certifications. Reputable manufacturers seek certifications from recognized bodies, which serve as a testament to the quality and reliability of their products. For consumers and businesses, choosing certified valves provides an assurance of safety and performance, as these products have undergone rigorous testing and evaluation.
Trustworthiness is another key attribute associated with natural gas safety valves. Users rely on these devices to function correctly under all conditions, and any failure can have dire consequences. Therefore, transparency in manufacturing processes, adherence to safety standards, and robust customer support are vital components that build trust between the manufacturer and the end user. Companies that excel in these areas are more likely to cultivate long-term relationships with their clients, based on the reliability and performance of their products.
In conclusion, natural gas safety valves are indispensable components in the realm of gas safety management. Their design, installation, and maintenance demand a high level of expertise and professionalism, underscored by comprehensive regulatory oversight. As technological advancements continue to enhance their capabilities, these valves will remain pivotal in safeguarding lives and infrastructure against the inherent risks of natural gas systems. For businesses and consumers alike, prioritizing safety and quality in selecting and managing these devices is crucial in fostering an environment of trust and reliability.