In the ever-evolving landscape of industrial technology, ensuring machinery efficiency is paramount, especially when it comes to components like gaseous gas filters. These filters are crucial in maintaining the purity and performance of complex systems that rely on gas-clean environments. Understanding their role, selection, and maintenance can significantly impact operational success.
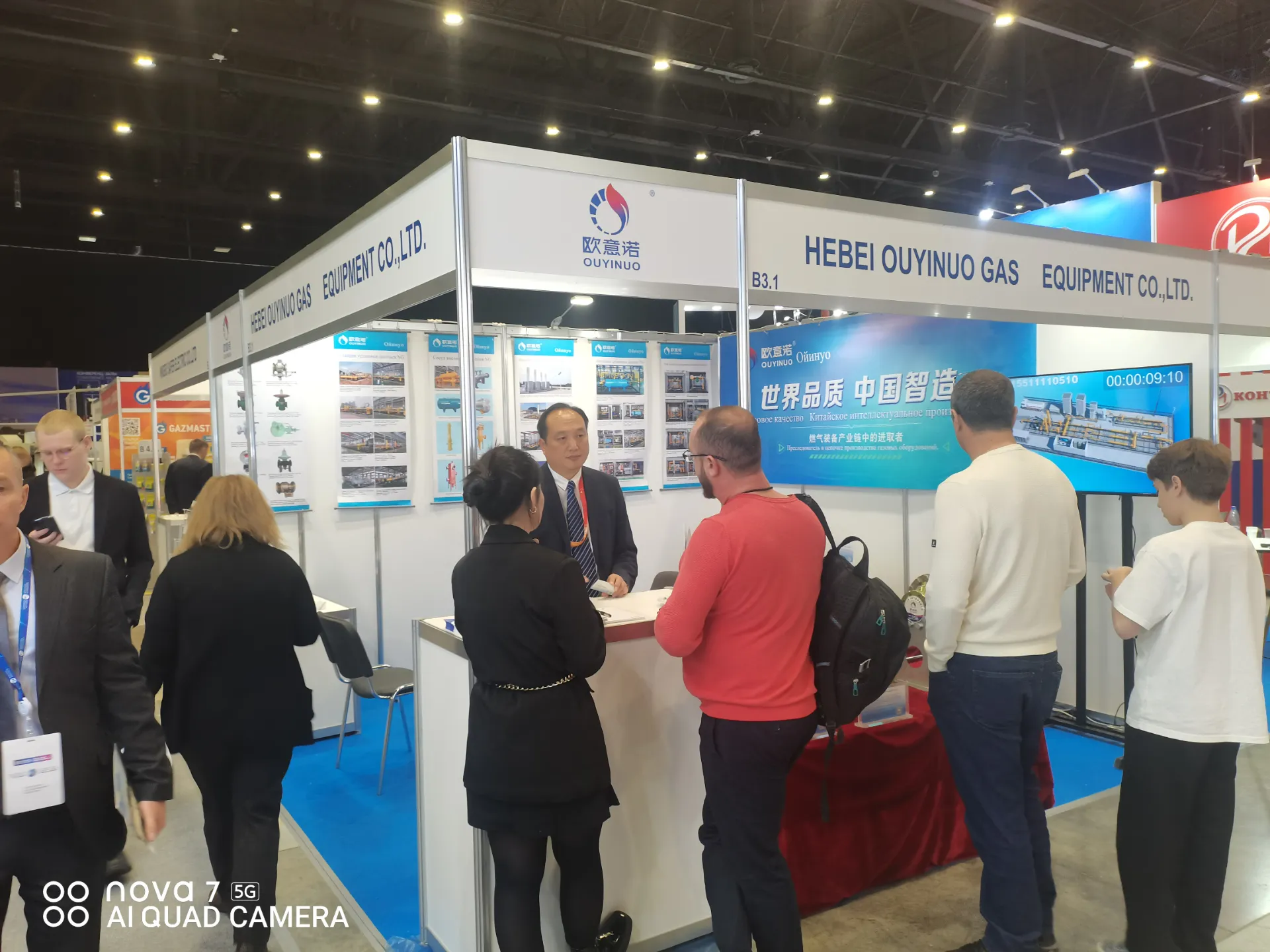
Gaseous gas filters specialize in trapping impurities from gaseous streams, preventing contamination and ensuring the optimum performance of machinery. Their effectiveness hinges on selecting the right filter for specific applications, adhering to high quality and standards, and regular maintenance. Here’s an in-depth look into why gaseous gas filters are indispensable and how to ensure their efficiency and longevity.
The Importance of Gaseous Gas Filters
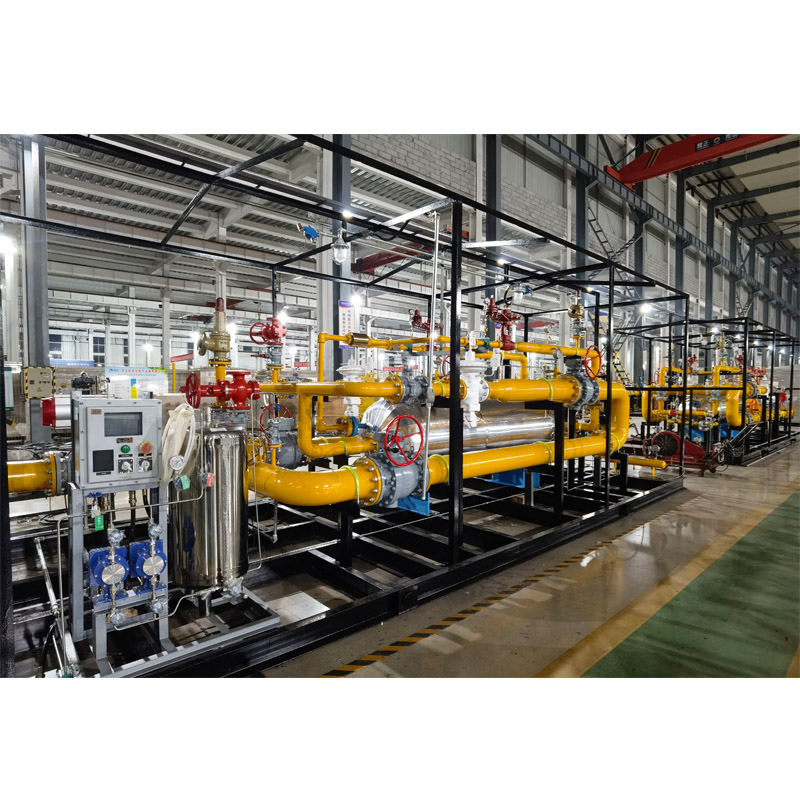
Gaseous environments, whether in chemical plants, refineries, or manufacturing setups, often carry particulates, dust, oils, or other contaminants that, if not filtered properly, can degrade equipment and product quality. The most significant advantage of using gaseous gas filters is their ability to remove these impurities, thus prolonging equipment life and maintaining the integrity of the final product.
Their strategic importance spans across various industries such as automotive, aerospace, pharmaceuticals, and food processing, where even minor contamination can lead to significant product recalls and safety hazards. Hence, the critical role of gaseous gas filters cannot be overstated, as they are vital in safeguarding investments and ensuring compliance with strict industry standards.
Key Considerations for Selecting a Gaseous Gas Filter
1. Filtration Efficiency Selecting a filter with the right efficiency rating is crucial. Factors like the size of contaminants, flow rate, and operational pressures must be considered to ensure the filter captures all potential impurities without hindering system performance.
2. Material Composition Filters need to be constructed from materials resistant to the specific gases and contaminants they’ll encounter. Stainless steel, PTFE, and other non-reactive materials are often used to withstand harsh chemical environments and prevent corrosion.
3. Temperature and Pressure Tolerances Choose filters that can operate under the temperature and pressure conditions typical for your application. This ensures longevity and reliability, even under extreme operating conditions.
4. Certification and Standards Compliance Filters that adhere to industry standards, such as ASME or ISO certifications, assure quality and performance, making them a trustworthy choice for critical applications.
Gas Gas Filter
Maintenance and Best Practices
Proper maintenance of gaseous gas filters is key to sustaining their functionality and extending their service life
1. Regular Inspection and Cleaning Routine inspections are necessary to check for wear and tear, while regular cleaning extends the filter's life and maintains its efficiency.
2. Scheduled Replacements Even the most resilient filters require replacement after a certain number of hours or operational cycles. Sticking to a replacement schedule prevents unexpected downtimes and ensures continuous protection.
3. Monitoring Systems Utilize pressure gauges and flow sensors to monitor filter performance, allowing for timely interventions and adjustments when deviations occur.
Industry Trends and Innovations
Recent advances in filtration technology have introduced enhanced filtering media, self-cleaning mechanisms, and smart monitoring systems. These innovations improve filtration efficiency and reduce operational costs through less frequent maintenance requirements.
Conclusion
Gaseous gas filters are a pivotal component in ensuring the operational efficiency of systems that require pristine gaseous conditions. By focusing on high-quality products, regular maintenance, and adopting innovative technologies, businesses can significantly enhance their system performance while securing their investment and reputation.
By understanding and implementing best practices in gaseous gas filtration, businesses align with the principles of Experience, Expertise, Authoritativeness, and Trustworthiness, ensuring both reliability and compliance in their industry operations. Through this dedication to excellence, companies not only safeguard their processes but also contribute positively to broader industrial advancements.