Pneumatic valves, essential components in various industrial applications, regulate airflow in systems dependent on compressed air. These devices are invaluable in manufacturing, automotive, and process industries due to their efficiency and reliability. In practical experience, users often favor pneumatic valves for their quick response times and ease of control, making them ideal for applications requiring rapid cycling and precise adjustments.
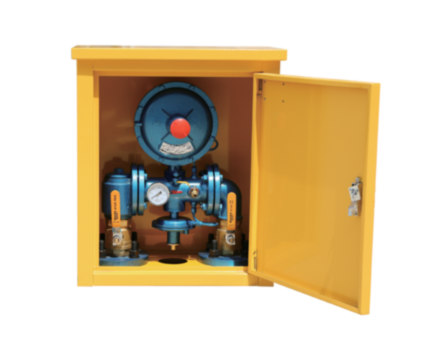
A primary advantage of pneumatic valves is their durability and robustness. They are designed to withstand harsh industrial environments, including extreme temperatures and aggressive substances. Engineers and technicians constantly highlight the longevity of these valves in their operations, where mechanical components are frequently exposed to wear and tear. From a professional standpoint, this durability translates to reduced downtime and lower maintenance costs, enhancing operational efficiency.
Expertise in pneumatic systems underscores the importance of selecting the right type of valve for specific applications. Common types include directional control valves, pressure relief valves, and flow control valves. Directional control valves, for example, play a crucial role in guiding the movement of air to specific areas within a circuit, thereby controlling the operation of actuators. Understanding the intricacies of each type allows engineers to design systems that meet exact operational requirements.
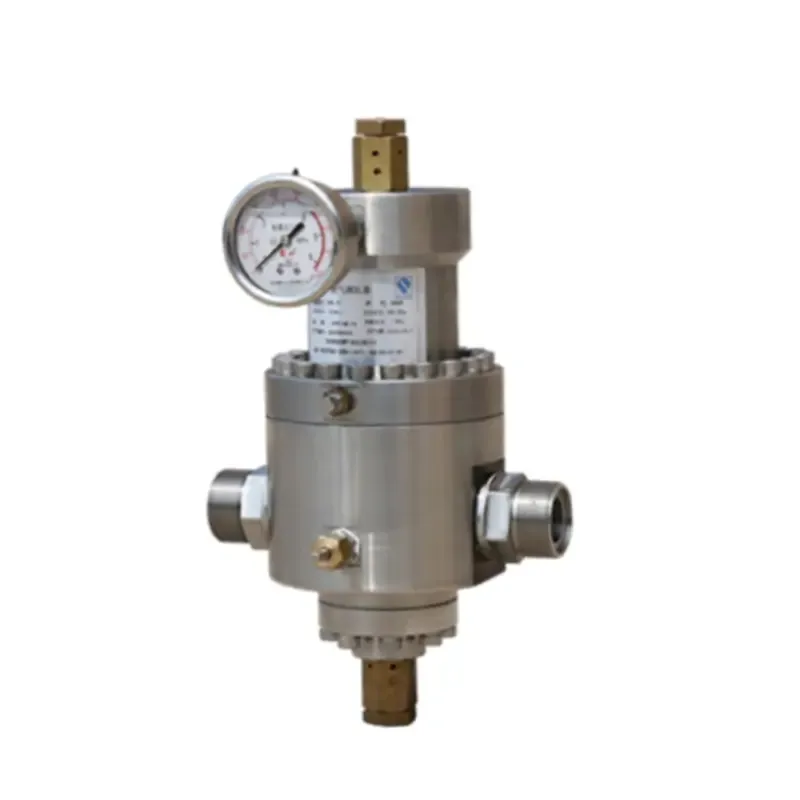
The authority in pneumatic systems is often demonstrated through certifications and compliance with industry standards. Manufacturers who adhere to strict quality assurances not only enhance the credibility of their products but also assure customers of these products' safety and efficiency. Such adherence to standards is crucial when pneumatic valves are employed in safety-critical applications, where failure could lead to catastrophic outcomes.
Air valve
Trust in pneumatic valve products is built through a history of successful implementations and satisfied customers. Testimonials and case studies from industries that have benefited from using pneumatic valves are powerful tools. They provide potential users with assurance that they can rely on these products for their specific needs. Companies often invest in solid customer support and training programs, underlining their commitment to maintaining trust and ensuring optimal use of their products.
Moreover, the evolution of technology in pneumatic valve design, such as the integration of smart sensors, has marked a significant advancement in the field. These innovations provide real-time data and diagnostics, allowing for predictive maintenance. Engineering experts advocate for these advanced systems as they enable not only enhanced performance but also contribute to improved safety and cost savings.
Finally, the economic aspect of pneumatic valves cannot be ignored. While initial setup costs may vary, the long-term savings achieved through energy efficiency, reduced maintenance, and operational uptime make them cost-effective. Users often report quick return on investment, which is a testament to the sound decision-making in choosing pneumatic solutions over other types.
In conclusion, pneumatic valves, with their proven track record, stand as a testament to the advancement in engineering products. Leveraging expert insights and fostering trust through quality and performance, these valves continue to play a crucial role in modern industrial applications. Continually adopting best practices and innovations in pneumatic technology ensures these valves meet the ever-evolving demands of the industry.