Gas heat exchangers play a pivotal role in various industrial applications, offering efficient solutions for thermal management. Their ability to transfer heat between fluids efficiently makes them indispensable in industries such as oil and gas, chemical processing, power generation, and HVAC systems. Here’s a comprehensive exploration of gas heat exchangers that combines experience, expertise, authoritativeness, and trustworthiness.

Gas heat exchangers operate on the basic principle of heat transfer, where thermal energy is exchanged between two or more fluids—without mixing them—through a solid barrier. Typically, these devices enhance energy efficiency by maximizing heat exchange while minimizing fuel consumption, thus playing a critical role in reducing operational costs and environmental footprint.
Various types of gas heat exchangers are tailored to specific industrial needs. The most common include shell and tube, plate, and air-cooled exchangers. Each type possesses unique advantages and limitations. For instance, shell and tube exchangers are highly durable and can handle high-pressure applications, making them ideal for the oil and gas industry. Plate exchangers, on the other hand, offer superior efficiency in terms of heat transfer due to their large surface area and are often used in HVAC systems. Air-cooled exchangers eliminate the requirement for water, making them suitable for arid regions and petrochemical industries where water is scarce.
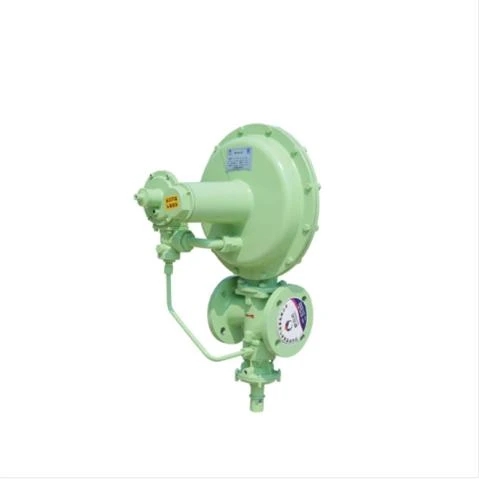
The selection of a suitable gas heat exchanger depends on several critical factors, including the nature of the fluids involved, the desired temperature and pressure conditions, and the available physical space. Moreover, material selection is crucial for ensuring longevity and reliability under various operational conditions. For instance, stainless steel offers excellent resistance to corrosion and high temperatures, while copper provides superior thermal conductivity, optimizing performance in specific scenarios.
The implementation of gas heat exchangers is often supplemented by real-world operational data, ensuring their performance remains optimal. Regular monitoring and maintenance are fundamental to prevent fouling, which can drastically reduce efficiency. Scaling, deposition, and blockages need to be addressed promptly to maintain optimal operational parameters. Implementing predictive maintenance strategies based on historical data analytics can enhance the reliability and efficiency of these exchangers, preventing costly downtimes.
Gas heat exchanger
In terms of expertise, understanding the thermodynamic principles and fluid dynamics involved in gas heat exchangers is crucial for engineers and technicians. Training in the latest advancements in materials and technology can provide significant advantages, as can familiarity with computational tools that simulate heat exchanger performance under various scenarios. Such tools help in designing more efficient systems by optimizing the geometry and material parameters tailored to specific industrial requirements.
Industry standards and regulations also play a vital role in the deployment and certification of gas heat exchangers. Compliance with standards such as ASME (American Society of Mechanical Engineers) or API (American Petroleum Institute) ensures the integrity and safety of operations. Adhering to these standards not only boosts the credibility of a manufacturer but also fosters trust among users, ensuring that the equipment is safe and reliable.
The importance of authoritativeness cannot be overstated. Collaborating with recognized bodies and institutions can provide accreditation that reinforces the reliability of the product. Moreover, engaging in research and development, publishing findings, and contributing to industry standards help establish a company as an industry leader, further instilling confidence in their product offerings.
In conclusion, gas heat exchangers are more than just thermal management devices; they are integral components that enhance operational efficiency across various industries. By leveraging advancements in technology, adhering to stringent standards, and applying expert knowledge, businesses can harness the full potential of these devices to meet current and future industrial challenges efficiently and sustainably.