Natural gas filtration systems play a crucial role in maintaining the efficiency and safety of operations across industries relying on natural gas as a primary energy source. These systems are fundamental in ensuring that the natural gas reaching homes, businesses, and industrial plants is free from contaminants that could impair equipment functionality and compromise safety.
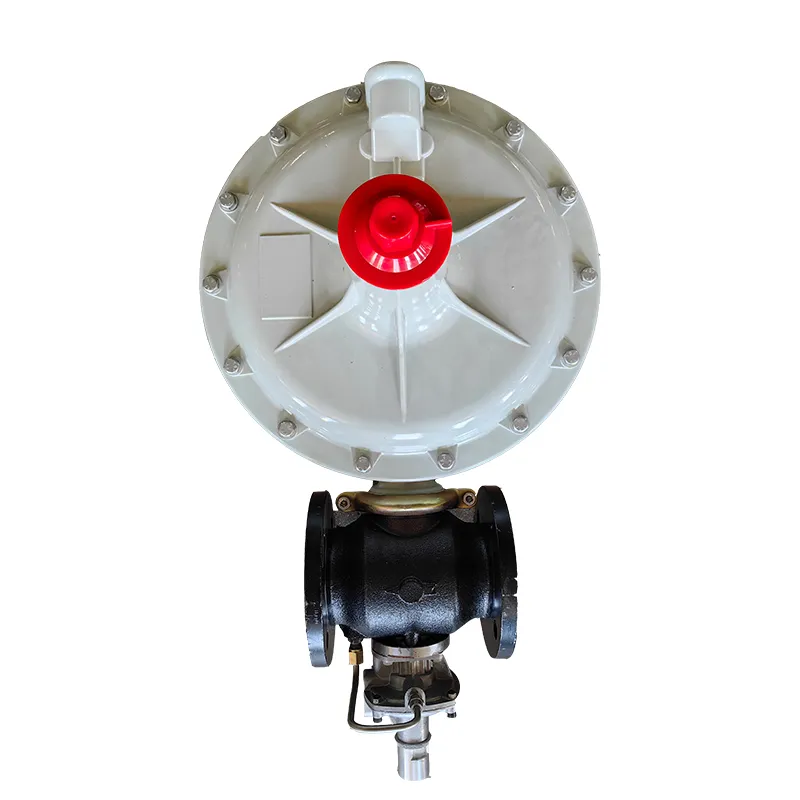
The essence of natural gas filtration lies in its ability to remove various impurities, such as solid particulates, liquids, and gas-phase contaminants. Achieving high levels of purity in natural gas is paramount, not only to meet regulatory standards but also to enhance the performance and longevity of the machinery it's used in, thereby providing significant cost savings and operational efficiency.
Natural gas filtration systems are typically comprised of several stages, each serving a unique purpose in the removal of different types of impurities. The initial stages of filtration often involve coalescing filters designed to aggregate fine particles into larger droplets and solid particles, enabling their easier removal. These filters are indispensable in extracting moisture and liquid hydrocarbons, which can otherwise cause corrosion, freezing, and fouling.
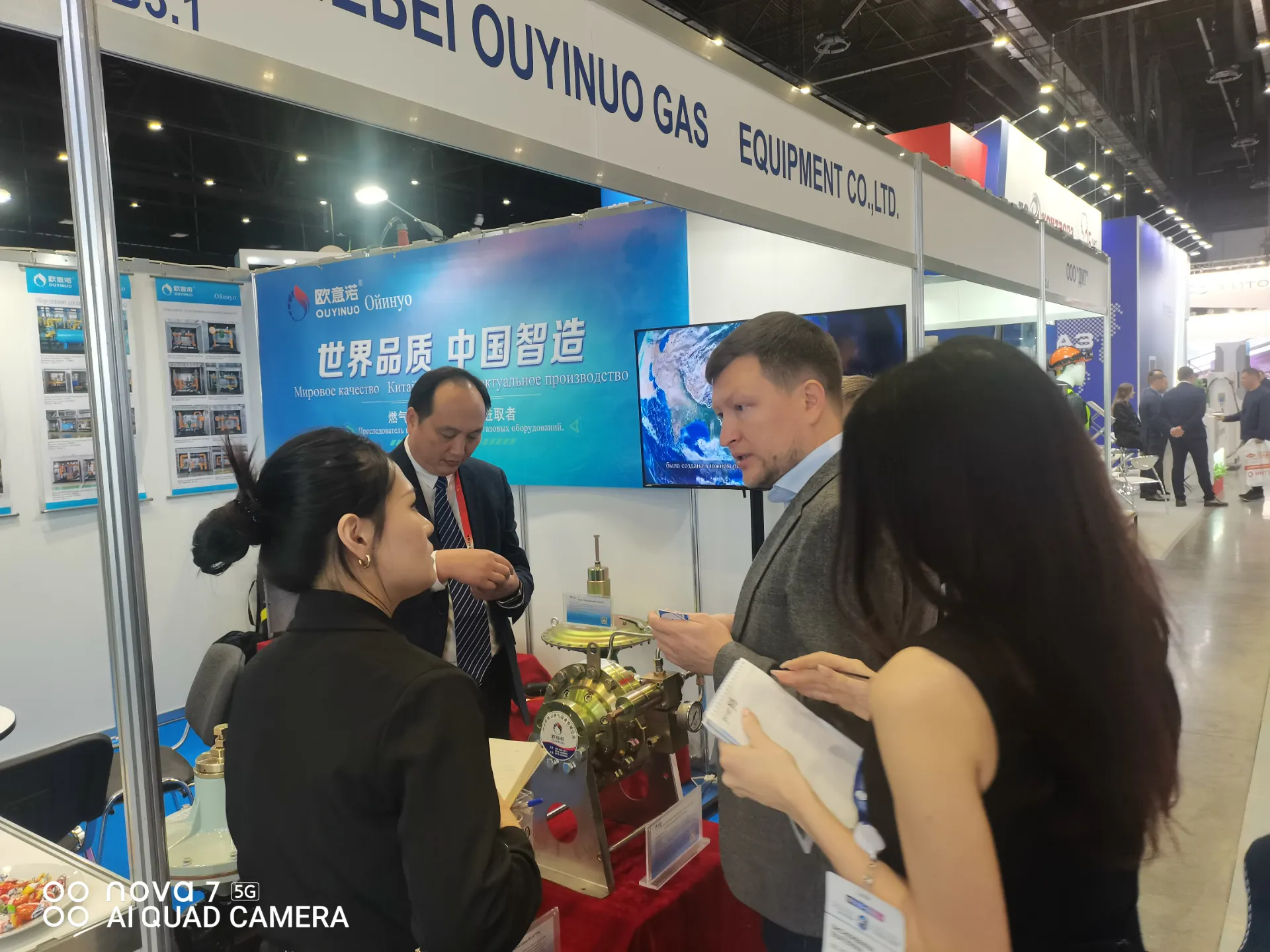
In further stages, adsorption filters come into play.
These filters employ materials such as activated carbon or zeolites to adsorb odorants and volatile organic compounds (VOCs). This step is critical in eliminating sulfur compounds and other gaseous contaminants that not only have environmental and health implications but may also damage combustion systems or inhibit catalysts used in chemical processing.
Advancements in filter technology have seen the introduction of high-efficiency particulate air (HEPA) and ultra-low penetration air (ULPA) filters, enhancing filtration capability. The emergence of nanotechnology has also started to influence the design of filtration systems. Nanofilters, for instance, allow for molecular-level separation, which is especially beneficial in high-precision industries where gas purity cannot be overstated.
An often overlooked component of efficient natural gas filtration systems is the monitoring and maintenance schedule. Regular maintenance including timely replacement of filter elements is critical to ensuring the system functions as intended. Modern filtration systems incorporate smart technology that alerts operators when maintenance is due or predicts potential failures, allowing for proactive management.
Filter natural gas
Industrial applications of natural gas filtration systems span numerous sectors such as power generation, chemical manufacturing, and oil refining. Each of these applications requires tailored filtration solutions; therefore, expertise in designing and implementing systems that meet specific operational needs is invaluable. Companies like Pall Corporation, Parker Hannifin, and Donaldson Company, Inc., lead the industry with their cutting-edge filtration products and solutions known for reliability and effectiveness.
Natural gas filtration is not merely a technical requirement; it's integral to environmental stewardship and operational sustainability. By removing harmful pollutants from natural gas, filtration systems help reduce emissions and the environmental footprint of gas utilization. Compliance with increasingly stringent environmental regulations mandates not only adherence to proper filtration practices but also ongoing research and development to innovate even more efficient systems.
Trust in natural gas filtration systems is paramount for stakeholders, from engineers and operators to regulatory bodies and end-users. The reliability and credibility of these systems hinge on their consistent performance and the quality assurance embedded in their design and manufacture. Professionals dedicated to this field often hold certifications and undergo continuous training to stay abreast of the latest developments.
Choosing the right natural gas filtration system involves a careful evaluation of the specific requirements related to gas composition, pressure, temperature, and flow rates. Expertise in this field ensures the selection of a system that delivers optimal performance, cost-efficiency, and compliance with health and safety standards.
In conclusion, natural gas filtration is a multifaceted discipline that calls for specialized knowledge, cutting-edge technology, and a commitment to excellence. As industries continue to demand higher energy efficiency and lower environmental impact, the role of advanced filtration systems becomes ever more critical. Investing in top-tier filtration solutions not only protects valuable equipment and ensures smooth operations but also demonstrates a commitment to sustainable and responsible energy use.