Understanding the significant role that heat exchangers play in various industries is crucial for experts and businesses alike. These devices are essential for transferring heat efficiently from one fluid to another, which is pivotal in processes like power generation, chemical processing, and HVAC systems in both residential and commercial buildings.

Heat exchangers come in various types, each serving specific purposes and tailored to particular industries. Tube and shell heat exchangers, for example, are commonly used in power plants and petroleum refineries due to their robust design and ability to handle high-pressure applications. Plate heat exchangers, on the other hand, are apt for environments where space is a constraint and efficiency is critical. Their compact design allows for excellent heat transfer rates and easy maintenance, proving indispensable in industries like food processing and pharmaceuticals.
From an expert standpoint, understanding the nuances of choosing the right heat exchanger involves considering factors such as thermal efficiency, material compatibility, and maintenance needs. Thermal efficiency varies greatly between different types of heat exchangers, influencing decision-making significantly. For instance, while a gasketed plate heat exchanger might offer higher thermal efficiency for moderate temperature applications, a spiral heat exchanger could be more suitable for highly viscous fluids and applications with heavy fouling.
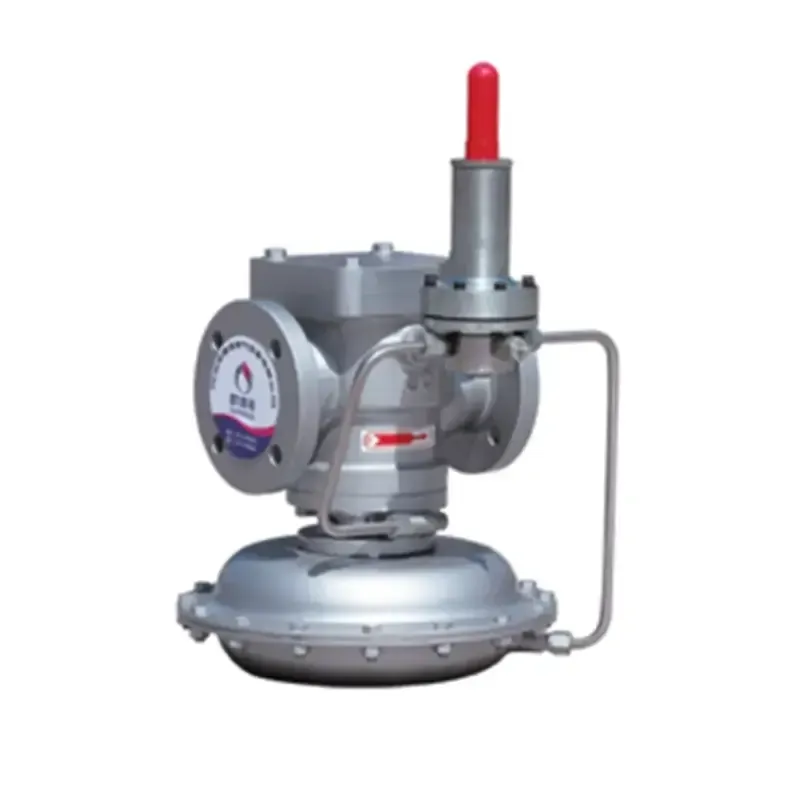
Material selection is another pivotal aspect. Corrosion resistance is vital, especially in industries processing aggressive chemicals or operating under extreme conditions. Stainless steel, titanium, and various alloys are commonly used materials, each offering distinct advantages depending on the operational environment. Expertise in material science enables engineers and procurement specialists to choose the optimal material, ensuring longevity and reliability of the heat exchanger, thereby reducing downtime and maintenance costs.
Authoritativeness in heat exchanger selection also involves keeping abreast with the latest technological advancements and industry standards. With technological innovations, such as nanofluid-based heat exchangers, emerging in the market, industry leaders must continually update their knowledge to maintain competitive advantage. Continuous education and certifications from established entities like ASME (American Society of Mechanical Engineers) enhance credibility and trustworthiness in the field.
Heat exchanger
Real-world experience provides invaluable insights into the practical aspects of implementing and operating heat exchangers. For instance, years of operational data might reveal the propensity for fouling in specific applications, guiding preventive maintenance practices. Operators often rely on their hands-on experience to optimize heat exchanger performance, potentially tweaking operational parameters like flow rate and temperature to achieve desired outcomes without incurring excessive wear and tear.
When addressing trustworthiness, the importance of transparent manufacturer guarantees and service agreements cannot be overstated. A reputable manufacturer will not only provide warranties but also support through lifecycle services such as inspection, cleaning, and refurbishment. A collaborative relationship with manufacturers and service providers ensures that operational disruptions are minimized and that expert advice is always at hand when unexpected challenges arise.
In addition, leveraging IoT and modern analytics for predictive maintenance can greatly enhance the reliability of heat exchangers. Real-time monitoring and data analytics allow for early detection of potential issues such as leaks or blockages, enabling prompt intervention. This foresight not only prevents costly downtime but also extends the lifespan of the equipment.
In conclusion, the expertise required in selecting and maintaining heat exchangers transcends basic knowledge of their types and applications. It demands a holistic understanding of industry needs, technical specifications, and trends, complemented by continuous learning and real-world experience. Applying this multifaceted knowledge ensures that heat exchangers remain efficient and reliable pillars in industrial operations. This comprehensive approach assures that businesses can rely on their heat exchanger systems to support their operational goals now and in the future, establishing a standard of excellence and trustworthiness that is recognized across the industry.