Elevating Industrial Efficiency with Advanced Pressure Tubes
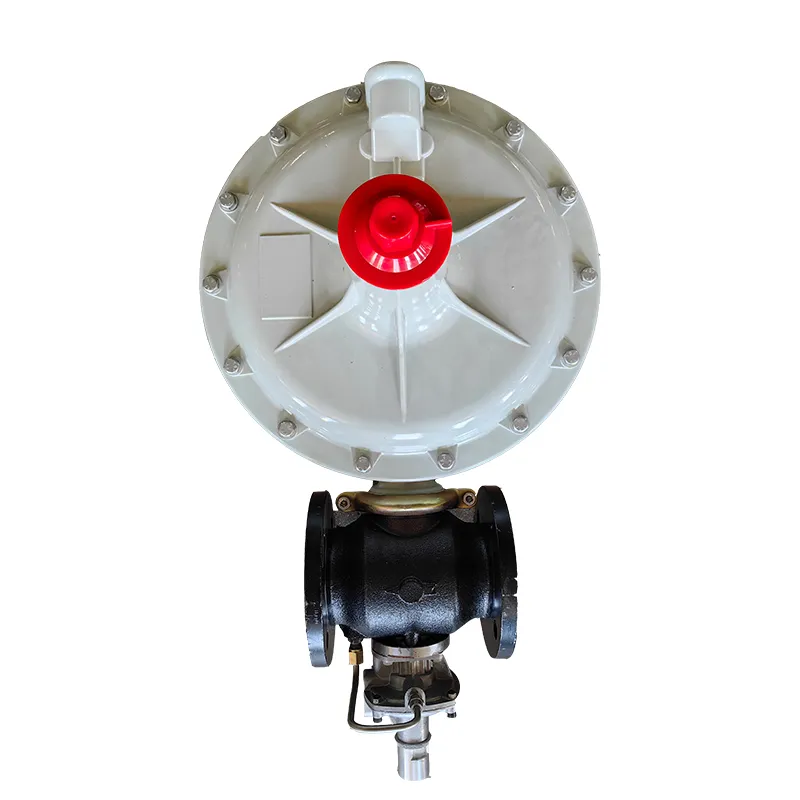
Pressure tubes, or أنبوب الضغط as they are known in Arabic, have become indispensable components across myriad industrial domains. These devices, engineered to withstand and contain pressures far surpassing atmospheric levels, are pivotal to the efficiency and safety of operations ranging from oil extraction to chemical processes, and even in aerospace applications.
Drawing from years of hands-on experience in the field, it has become increasingly clear that the key to leveraging the full potential of pressure tubes lies in a keen understanding of their material compositions, structural design, and operational environments. Advanced pressure tubes are crafted from an array of materials including but not limited to stainless steel, carbon composites, and titanium alloys. Each material offers unique benefits; stainless steel, for example, is prized for its corrosion resistance and strength, making it ideal for harsh environments.
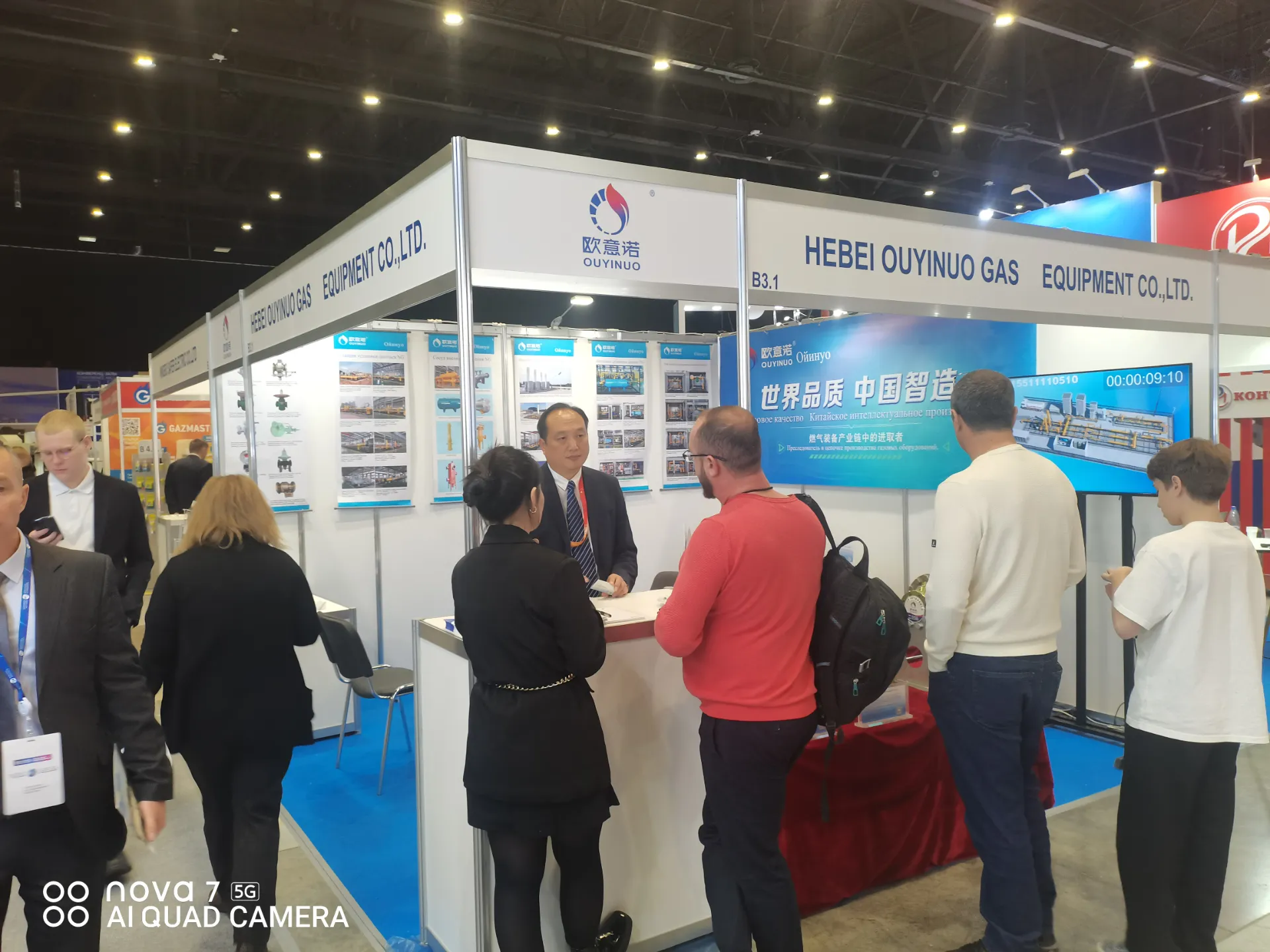
The expertise involved in the selection process of a pressure tube cannot be overstated. Factors such as the intended pressure range, temperature conditions, chemical compatibility, and physical load requirements must be meticulously analyzed. For instance, in high-temperature chemical reactions, tubes constructed from nickel-based alloys offer unmatched thermal resilience and corrosion resistance, allowing for safer and more efficient operations.
Furthermore, correctness in design is equally crucial. Tube geometry, wall thickness, and joint engineering are factors that can determine the success or failure of a system. In applications involving rapid pressure fluctuations, a well-engineered tube with appropriate elastic properties can prevent catastrophic failures. Recent innovations have also introduced smart materials into the pressure tube domain — these are capable of self-repairing minor damages, thereby extending lifespan and reliability.
Pressure tube
Authoritative voices in the field consistently emphasize the importance of ongoing assessment and maintenance protocols to ensure long-term functionality and safety.
Pressure testing, for example, should be performed routinely to detect potential weaknesses. Additionally, non-destructive testing methods like ultrasonic or X-ray inspections have been implemented for even more comprehensive evaluations.
Trust in pressure tube systems is generated through rigorous adherence to international standards and certifications. Organizations such as the American Society of Mechanical Engineers (ASME) and the International Organization for Standardization (ISO) provide guidelines that shape the design, manufacturing, and operational protocols. Compliance with these standards ensures that products not only meet but exceed expected performance metrics.
For businesses seeking to integrate pressure tubes into their operations, it is paramount to engage with reputed manufacturers who can demonstrate a track record of quality and innovation. Such partnerships often provide tailored solutions that are not only economically viable but also enhance operational efficiencies. Moreover, the ability to offer technical support and user training further solidifies the reliability and trustworthiness of the technology being implemented.
In conclusion, pressure tubes are not mere conduits; they are the backbone of many industrial systems, driving advancements and innovation. As specialists in the domain, the ongoing challenge and opportunity lie in continuously refining materials, designs, and maintenance techniques to meet the escalating demands of modern industry. The future promises further integration of smart technologies, opening new avenues for advancements in efficiency and safety. By aligning with these innovations, industries can not only achieve operational excellence but also lead the charge towards a safer, more sustainable future.