Pressure relief valves are essential components in various industrial systems, providing a critical safety function to prevent overpressure conditions that could lead to equipment failure, catastrophic destruction, or personal injury. With their ability to automatically release pressure from a system when it exceeds a preset limit, these valves are indispensable in industries ranging from chemical processing to oil and gas, and their expertise in maintaining system integrity is paramount.
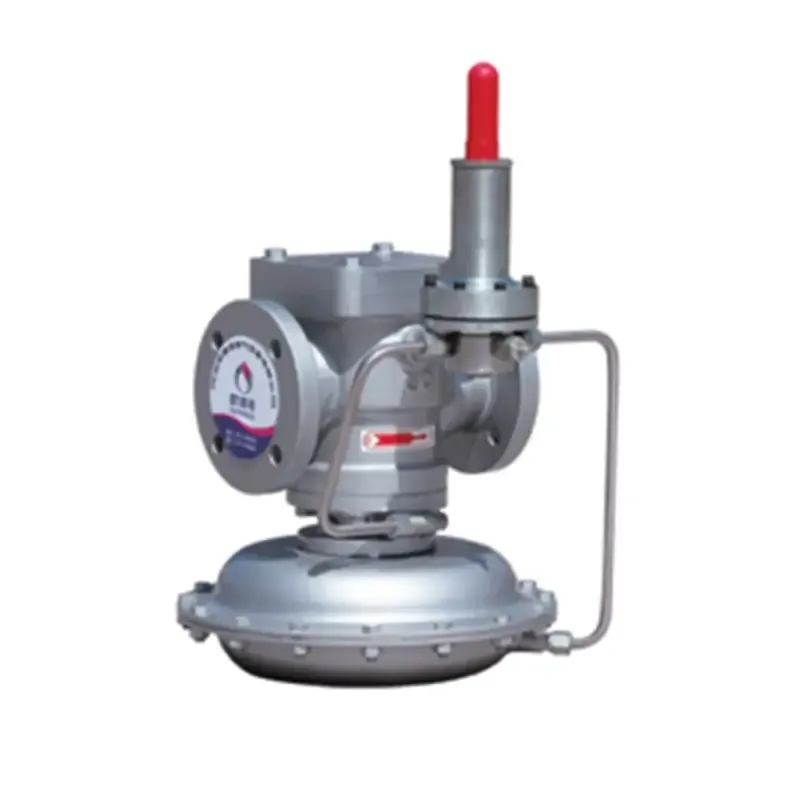
Selecting the right pressure relief valve is crucial for the optimal operation of any pressurized system. Factors to consider include the medium (gas or liquid) within the system, the set pressure, temperature conditions, and the specific industry application. Tailoring these factors ensures that the valve not only performs efficiently but also complies with regulatory standards and industry best practices, safeguarding both the equipment and personnel.
The design of pressure relief valves has evolved significantly, with manufacturers leveraging advanced materials and cutting-edge technology to enhance performance and reliability. For instance, modern valves are often crafted from high-grade stainless steel or specialized alloys, providing exceptional resistance to corrosion and extreme environmental conditions. Innovations such as soft seat technology and bellows construction further enhance sealing capabilities and reduce the risk of leakage, even under high cycling conditions.
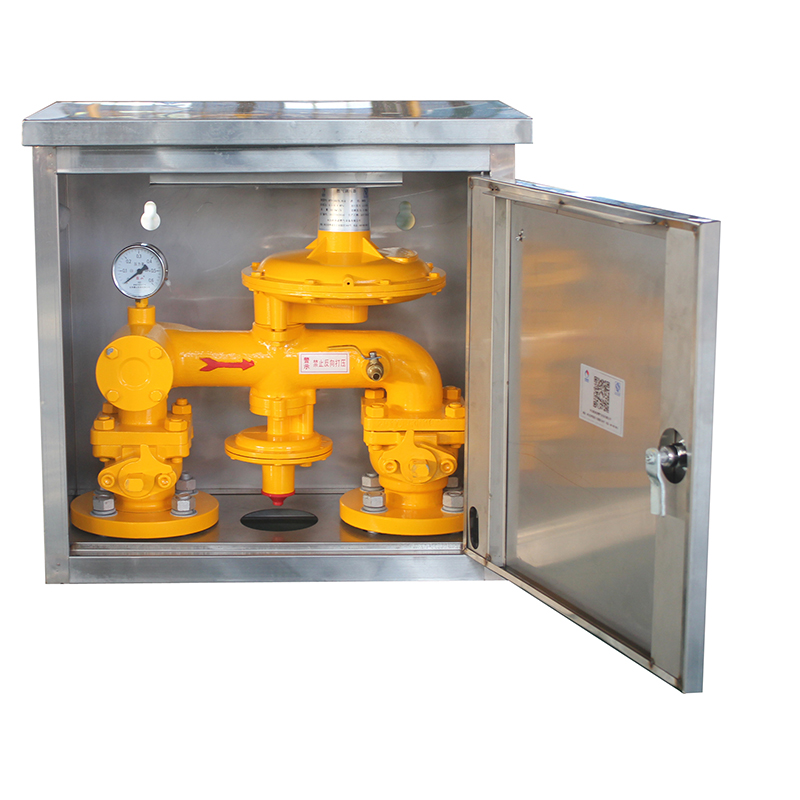
Installation and maintenance of pressure relief valves require expertise to ensure operational readiness. Proper installation involves not only secure mechanical mounting but also precise alignment and system integration. Skilled technicians or engineers must calibrate the valves accurately according to the predefined pressure limits, which are often determined during the system design phase. Regular maintenance checks, including inspections for wear and tear, debris accumulation, and mechanical integrity, are vital in prolonging the valve's life and assuring its functionality.
Compliance with international standards such as those outlined by the American Society of Mechanical Engineers (ASME) or the International Organization for Standardization (ISO) is another critical aspect. These standards dictate the design, testing,
and certification of pressure relief valves. Purchasing valves certified by recognized bodies assures quality and reliability, reducing downtime and preventing potentially costly incidents.
Pressure relief valve
To boost operational efficiency and ensure uninterrupted safety, employing digital pressure management systems can greatly enhance the capabilities of traditional pressure relief valves. These systems provide real-time monitoring and analytics, facilitating proactive maintenance and immediate response to anomalies. Industrial Internet of Things (IIoT) integration enables remote monitoring, offering a layer of convenience and advanced control over the pressurized systems.
In industries such as oil and gas or chemical processing, where the stakes are high, utilizing pressure relief valves with proven performance and durability can lead to operational excellence. Industries benefit not only from compliance and safety but also from the trust they build with stakeholders by demonstrating a commitment to using reliable and efficient pressure management systems.
Trust in a pressure relief valve manufacturer is built through a track record of excellence, adherence to stringent quality standards, and continuous innovation. Manufacturers that invest in research and development, listening to the specific needs of various industries and tailoring their products accordingly, stand out as leaders in the field. A company’s ability to offer technical support and training further enhances its authority and trustworthiness in the market.
Ultimately, pressure relief valves are more than just mechanical devices; they are a cornerstone of operational safety and reliability across numerous industries. The expertise involved in designing, selecting, and maintaining these valves ensures that systems run smoothly, risks are minimized, and operational continuity is maintained. As technology advances, so too will the capabilities and reliability of these vital components, continuing to provide assurance and peace of mind in the most demanding environments.