In the rapidly evolving energy sector, natural gas has emerged as a pivotal resource, particularly due to its role in reducing carbon footprints and enhancing energy efficiency. This rise in prominence brings attention to natural gas filtration, a crucial process ensuring that the gas delivered to consumers and industries is clean and efficient. In a market driven by sustainability and technological advancement, understanding the intricacies of natural gas filtration is essential for stakeholders at all levels.
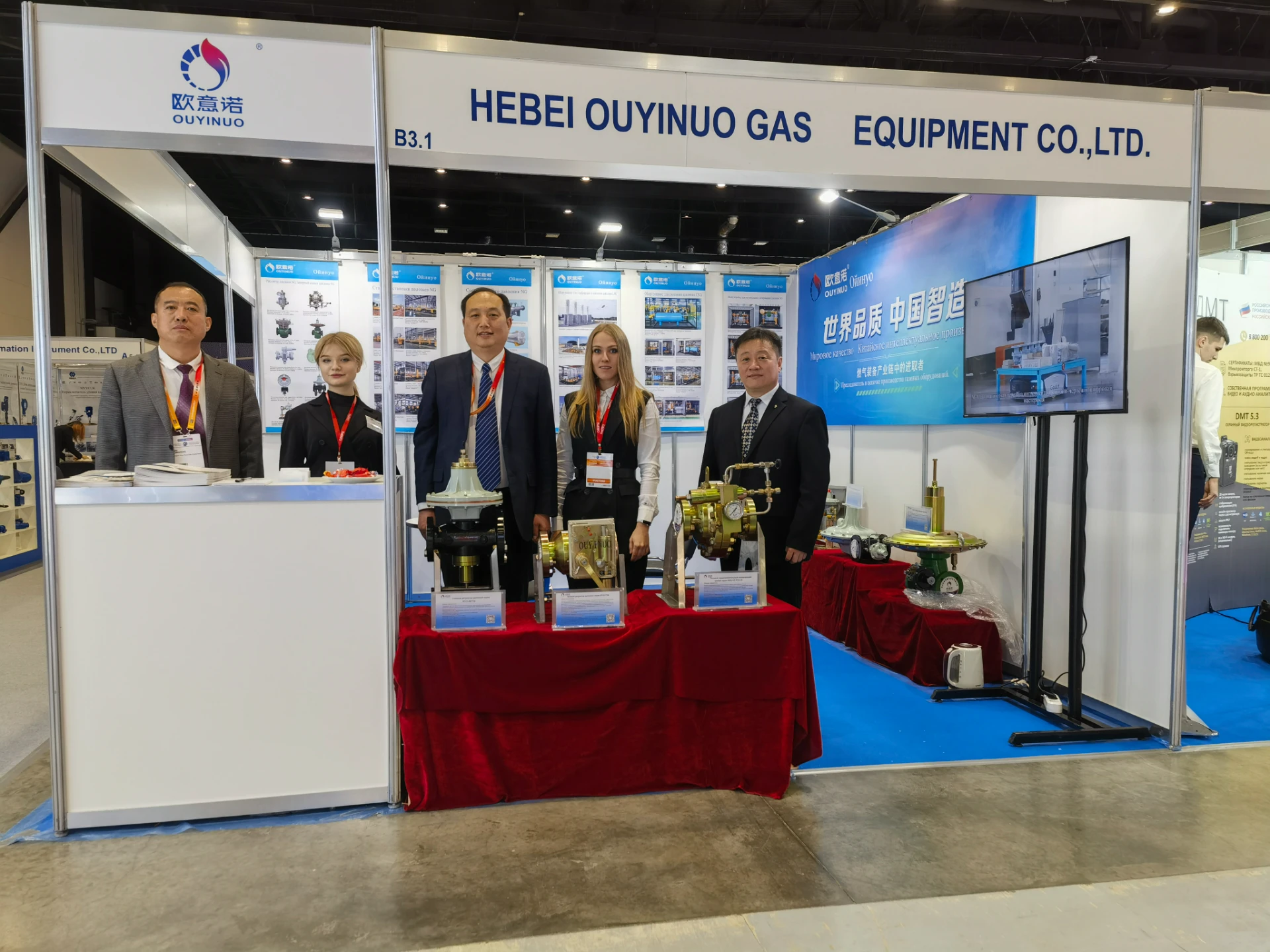
Natural gas, as it is extracted directly from the earth, is not entirely pure. It often contains contaminants such as carbon dioxide, hydrogen sulfide, water vapor, and particulates. These impurities, if not addressed, can lead to numerous issues, including reduced energy efficiency, corrosive damage to pipelines and engines, and even hazardous emissions when the gas is used. Herein lies the importance of effective natural gas filtration, a field where significant strides have been made in recent years.
One of the foremost developments in this sector is the integration of advanced membrane technologies. Such membranes are designed to selectively permeate desired gases while filtering out impurities. This not only optimizes the quality of natural gas but also enhances the overall efficiency of its distribution network. These technologies have been refined to operate under varying pressures and temperatures, demonstrating versatility and robustness in different operational environments.
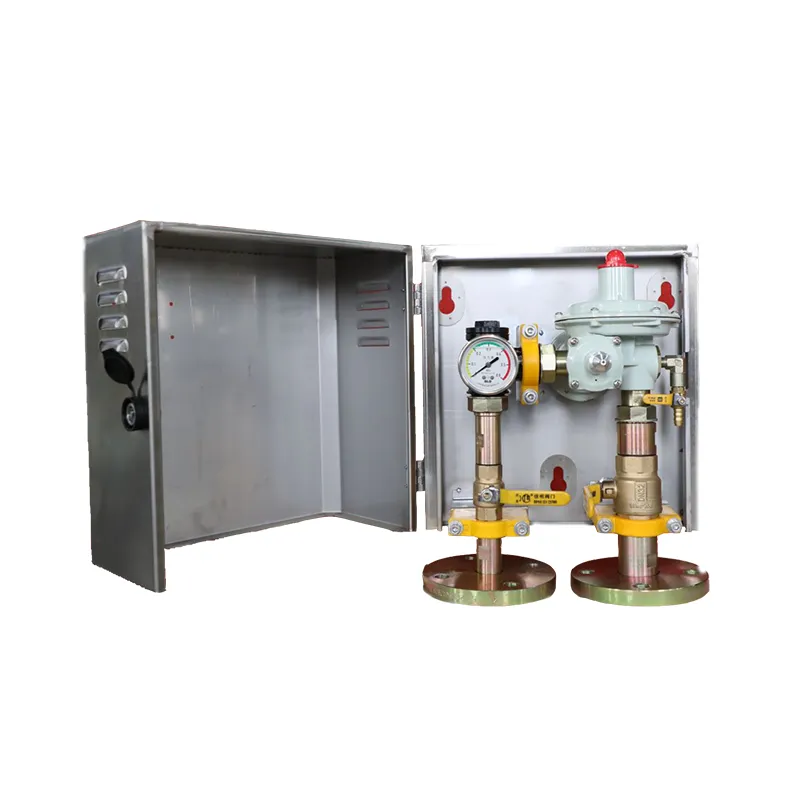
Industry experts emphasize the importance of employing multi-stage filtration processes. These systems are built to tackle different types of contaminants at various stages. Initial stages might involve coarse filters that eliminate large particulates, while subsequent stages use more sophisticated methods, like adsorption and membrane filtration, for finer purification. By layering these methodologies, filtration systems ensure a high purity level in the gas delivered downstream.
Natural gas filtration
Trust in filtration systems is bolstered by rigorous testing protocols. Companies producing filtration equipment often partner with independent laboratories to certify the efficiency and reliability of their products. These certifications, coupled with compliance to international standards such as ISO 9001 and API (American Petroleum Institute) specifications, offer end-users peace of mind regarding the safety and performance of their filtration solutions.
Furthermore, the drive towards sustainability has led to innovations that reduce the environmental impact of filtration technologies. For instance, some systems now incorporate reusable materials and energy-efficient operations, decreasing the ecological footprint of natural gas processing facilities. This development aligns with the broader industry trend towards green energy and responsible resource management.
Experience from industry leaders highlights the importance of proper installation and maintenance of filtration systems. Regular inspections, cleaning, and timely replacement of filter components are crucial to maintaining optimal performance and extending the lifespan of the systems. Companies often provide comprehensive service packages to support clients in these tasks, ensuring uninterrupted operation and compliance with safety regulations.
The field of natural gas filtration exemplifies a fusion of experience, expertise, authority, and trustworthiness. It is a testament to how rigorous engineering practices, informed by years of research and development, can create solutions that meet modern energy challenges efficiently. Stakeholders worldwide continue to invest in filtration technology, recognizing its indispensable role in delivering cleaner, safer, and more efficient energy solutions for the future.