Gas valves are an integral component in numerous systems and appliances, from household kitchens to industrial applications. Their primary function is to control the flow and pressure of gas within a piping system, ensuring safety and efficacy. Understanding the nuances of gas valves, their types, maintenance, and selection criteria can enhance safety and improve operational efficiency.
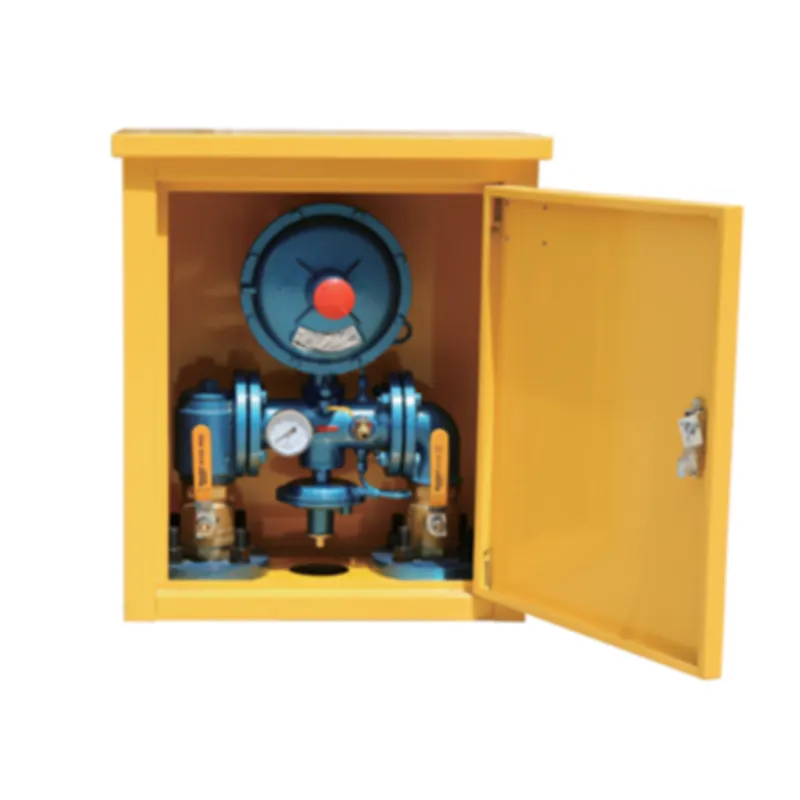
Gas valves come in various types, tailored for specific applications. Among the common varieties are ball valves, butterfly valves, and diaphragm valves. Each type has its distinct design and functionality. Ball valves, for instance, are known for their durability and are used where a tight seal is critical. Their mechanism involves a rotating ball with a bore, which aligns with the flow when open and obstructs when closed. Butterfly valves, on the other hand, use a rotating disc to allow or block flow, offering quick shut-off and being space-efficient due to their compact design. Diaphragm valves add the benefit of precise flow regulation, especially beneficial in systems requiring sterile conditions, such as in pharmaceutical industries.
The selection of a gas valve is a critical decision influenced by several factors including the nature of the gas, pressure requirements, temperature ranges, and the specific application's safety regulations. For instance, valves used in industrial applications might need to withstand extreme pressures and temperatures, requiring materials like stainless steel or other high-performance alloys. In contrast, domestic applications would prioritize ease of use and reliability over extreme specifications. Thus, thoroughly understanding these requirements ensures the selection of a valve that is both safe and efficient.
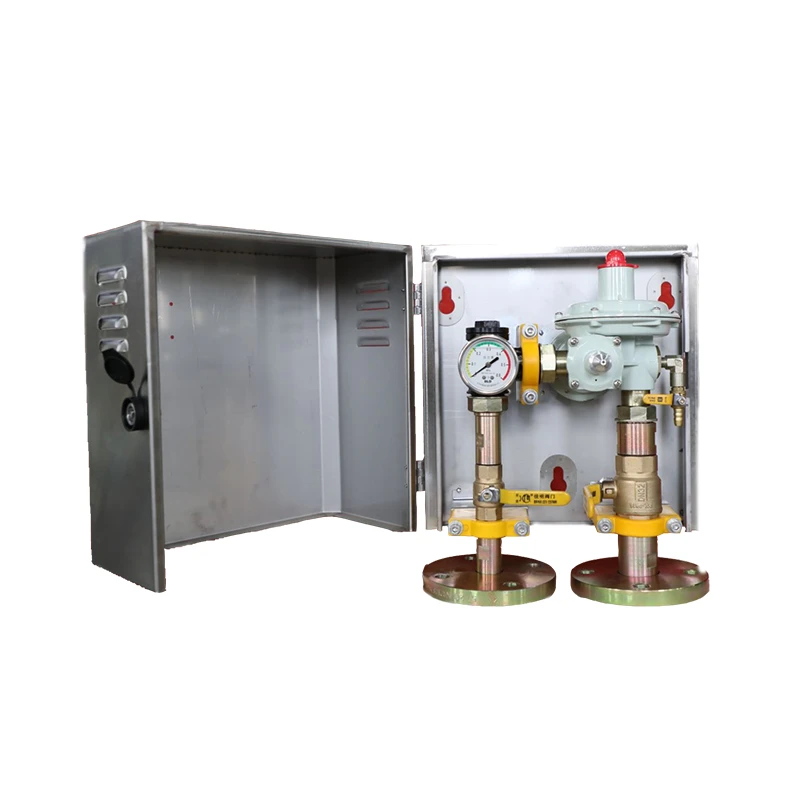
Installation and maintenance of gas valves is another crucial aspect of their operation. Proper installation involves ensuring that the valve is compatible with the system's design, and is positioned to allow easy access for future maintenance. It is crucial for reducing potential hazards such as leaks, which could lead to dangerous gas accumulation. Maintenance includes regular inspections for wear and tear, testing for leaks, and ensuring that the seals remain intact. A rigorous maintenance schedule not only extends the life of the valve but also maintains the safety of the entire system. Any signs of aging or damage, such as corrosion or wear, should prompt immediate replacement to prevent system failures.
Safety is paramount when dealing with gas valves. Training personnel in proper handling techniques and emergency procedures is essential. Clear labeling of valve controls, regular system audits, and adherence to regulatory standards form the backbone of a solid safety strategy. Furthermore, incorporating advanced technologies such as electronic monitoring systems can provide real-time data on valve performance, enabling prompt corrective actions when deviations from normal operation are detected.
Gas valve
Expertise in gas valve technology extends beyond just technical know-how; it encompasses an understanding of regulatory landscapes that govern their use. Compliance with standards such as the American National Standards Institute (ANSI) and the International Organization for Standardization (ISO) is vital for ensuring that gas valves meet required safety and quality benchmarks. These standards often dictate specifications regarding material, design, and operational testing, integrating safety and reliability into every facet of valve manufacturing and application.
Additionally, the integration of smart technologies is transforming how gas valves are operated and maintained. Smart valves equipped with sensors and connectivity options allow for automated monitoring and control of gas flow. These advancements enable predictive maintenance, reducing downtime and enhancing the lifespan of the valve-and-system complex. For industries transitioning to smart infrastructures, investing in these cutting-edge technologies might seem upfront expensive, but the long-term cost savings in maintenance and enhanced safety offer a substantial return on investment.
Trust in a gas valve system is built over time through a combination of high-quality manufacturing, rigorous testing, and consistent performance in the field. Users should look for manufacturers with a proven track record of producing reliable valves and offering comprehensive customer support. This support is crucial when troubleshooting issues or when seeking advice on system upgrades and optimizations.
In conclusion, the strategic selection, installation, and maintenance of gas valves are imperative for ensuring operational safety and efficiency. As technology evolves, so too do the capabilities of these systems, offering new opportunities for enhancing safety, performance, and cost-effectiveness. Armed with knowledge and expertise in this field, choosing the right gas valve solution is achievable and rewarding for both residential and industrial applications.