In the world of industrial applications, the pneumatic valve stands as a cornerstone technology, renowned for its reliability and efficiency in controlling a variety of media such as gases and liquids. This essential piece of equipment finds its place in numerous sectors including manufacturing, oil and gas, pharmaceuticals, and food processing, to name a few. As technology evolves, the importance of understanding the intricacies of pneumatic valves becomes paramount for businesses looking to optimize their operations.
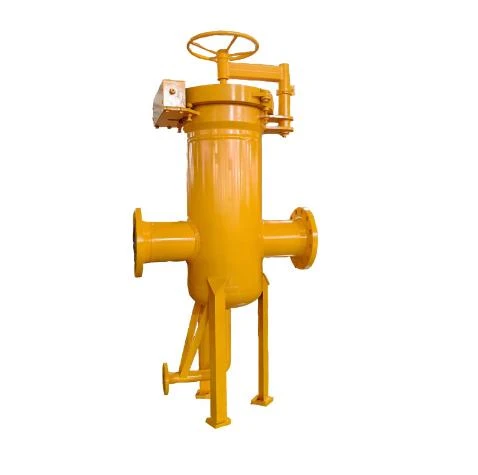
The pneumatic valve operates by utilizing compressed air to regulate the flow of fluid through a system. Unlike manual valves that require physical intervention to operate, pneumatic valves offer automated control, which integrates seamlessly with modern systems requiring real-time fluid dynamics management. This automated control not only enhances precision but also significantly improves safety and reduces labor costs.
When diving deeper into the technicalities, pneumatic valves come in various types, each suited for specific applications. The most common types include the diaphragm valve,
ball valve, and butterfly valve. Each carries distinct advantages making them suitable for particular environments. For example, diaphragm valves are ideal for hygienic and sterile processes because they minimize the risk of contamination and are easy to clean. On the other hand, ball valves provide excellent sealing capabilities and are therefore preferred in high-pressure applications.
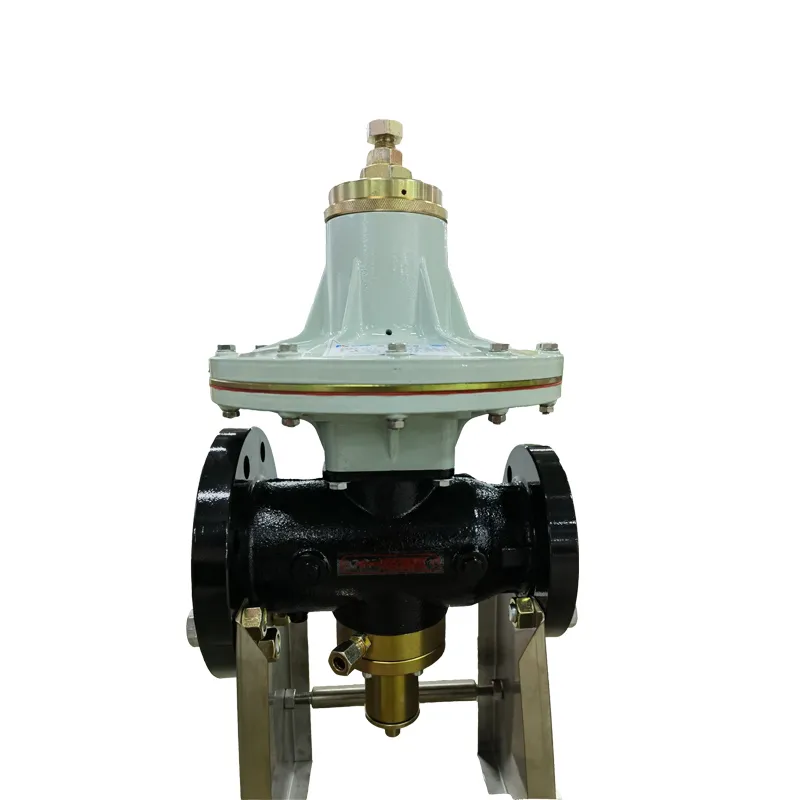
Experience in implementing pneumatic valves in diverse conditions has shown that choosing the correct type can dramatically impact system efficiency. An incorrect choice can lead to reduced performance, increased maintenance needs, and potential downtime. Therefore, expertise in understanding the operational environment and the media involved is essential for selecting the appropriate valve type. Engineers and technical specialists are often required to assess these conditions and recommend the best solutions accordingly.
Trustworthiness in selecting a suitable pneumatic valve supplier cannot be overstated. Reliable manufacturers not only provide products that meet industry standards and certifications but also offer robust after-sales support and warranty services. This support includes technical assistance, installation guidance, and troubleshooting, ensuring that any operational hiccups are dealt with promptly and efficiently.
Air valve
Furthermore, the materials used in pneumatic valve construction play a critical role in determining their durability and suitability for different applications. Materials such as stainless steel offer excellent resistance against corrosion and can withstand a range of temperatures, making them ideal for harsh environments. This material selection signifies the importance of authority in the manufacturing process, where certified and experienced manufacturers adhere to stringent quality control measures in their production lines.
The implementation of pneumatic valves also intersects with the emergence of smart technologies. The incorporation of IoT (Internet of Things) into pneumatic systems allows for enhanced monitoring and control capabilities. Smart valves equipped with sensors can relay real-time data regarding pressure, temperature, and flow rates directly to control systems. This feature allows for predictive maintenance and immediate response to any anomalies, significantly reducing the risk of operational failures.
Understanding the benefits and capabilities of pneumatic valves through hands-on experience provides an invaluable perspective that textbook knowledge alone cannot supply. Businesses that have integrated these systems report increased efficiency, reduced manual intervention, and improved operational transparency. This direct feedback loop ensures that the sector continues to innovate and develop more sophisticated solutions.
Finally, one cannot overlook the global trends pushing towards sustainable and environmentally friendly solutions. Pneumatic valves have been at the forefront of this movement, aiding in energy conservation by optimizing air consumption. The efficient use of air not only conserves energy but also contributes to lower carbon emissions, aligning with contemporary environmental goals and regulations.
In conclusion, the pneumatic valve is a pivotal component in advanced industrial systems. Its role stretches beyond simple fluid control to encompass the integration of smart technologies and sustainable practices. Mastery of pneumatic valve systems necessitates experience, expertise, authority, and trust, ensuring operational efficiency and strategic advantages in various industrial applications. As industries continue to expand their scope, the reliance on and significance of pneumatic valves will only amplify, making them indispensable in the modern industrial landscape.