Isolation valve systems are pivotal in the functioning of diverse industrial, commercial, and residential infrastructures. As the term implies, an isolation valve serves a primary function it isolates sections of a system which enhances safety, efficiency, and maintenance. An exploration of its applications and benefits underscores the rationale behind its ubiquitous presence in piping systems around the globe.
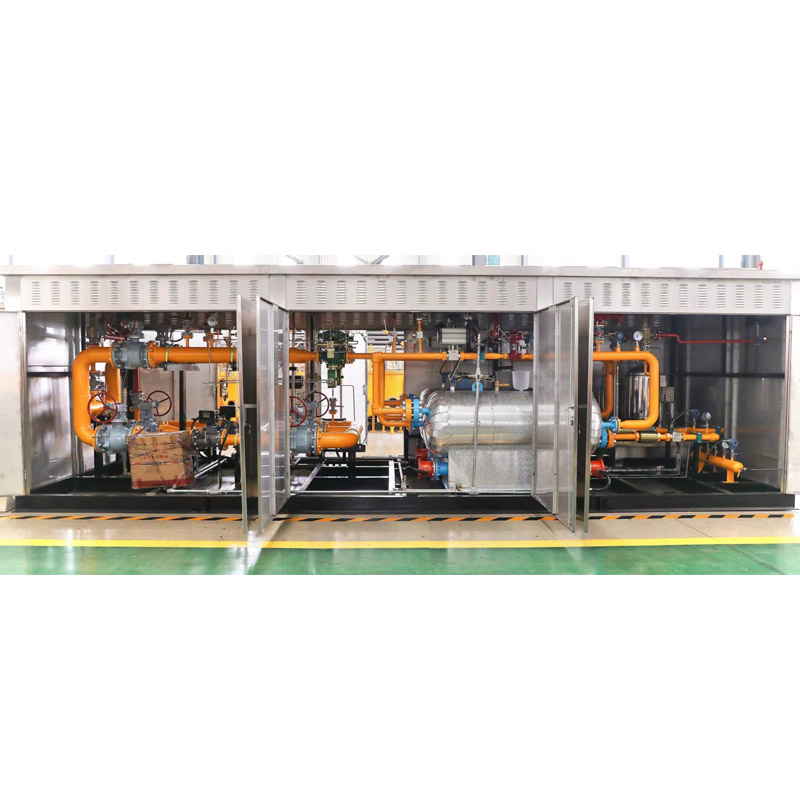
An expert understanding of isolation valves begins with their definition and types. Isolation valves, also known as shut-off valves or block valves, are devices installed into a pipeline to halt or redirect the flow of a fluid. Various kinds include gate valves for linear flow halting, ball valves offering rotational flow control, and plug valves for on-off control. Their versatility makes them indispensable for fluid handling in industries like petrochemical, water treatment, and HVAC systems.
The credibility of these valves stems from their proven capability to prevent leaks and system failures, ensuring both safety and operational integrity. High-quality isolation valves reduce the risk of pressure surges that can lead to significant damage, thus maintaining the reliability of extensive fluid systems. This reliability is particularly vital in hazardous environments where any malfunction can lead to catastrophic outcomes.
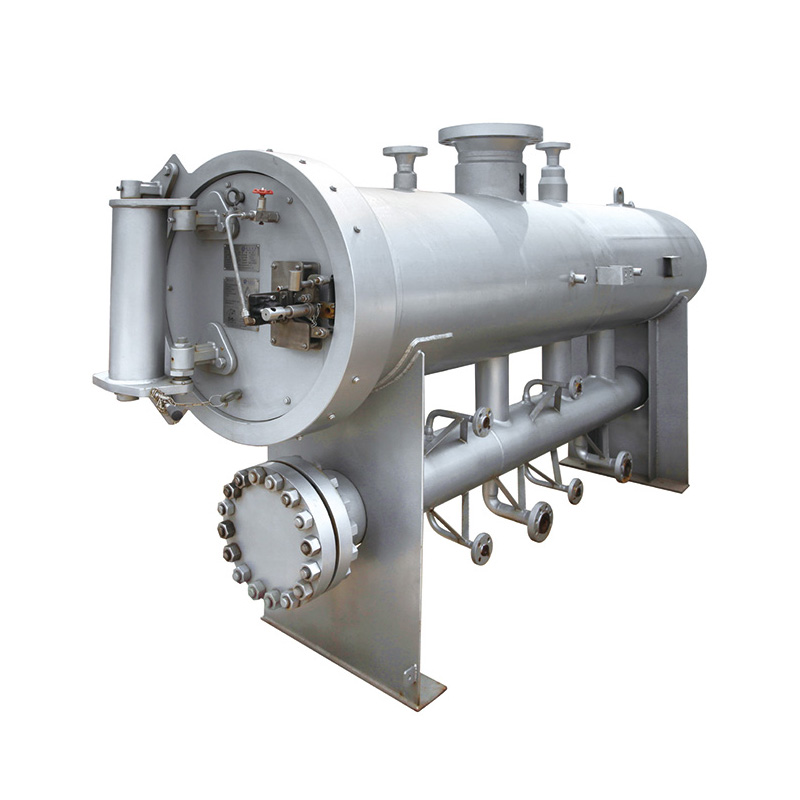
From an authoritative standpoint, isolation valves are manufactured to comply with stringent international standards, such as the American National Standards Institute (ANSI) and the British Standards Institution (BSI). These standards ensure that the valves meet rigorous durability and performance criteria, thereby guaranteeing safety and efficiency.
Close the valve
In terms of expertise, it is essential for technicians and engineers to understand the nuances of selecting the appropriate valve for specific applications. Proper selection requires a deep understanding of the system's pressure requirements, type of fluid being transported, and environmental considerations. For instance, a high-pressure steam line may necessitate the use of gate valves for their ability to handle high temperatures without deformation.
Trustworthiness in the realm of isolation valves is built on consistent performance and regular maintenance. Routine checks ensure that valves function smoothly and extend their operational lifespan. Consulting reputable manufacturers known for their longevity and commitment to quality reinforces trust in these crucial components. King companies in the industry often provide extensive warranties reflecting confidence in their product’s durability and functionality.
Real-world applications of isolation valves are both vast and varied. In residential settings, they are critical for water supply systems, allowing for easy maintenance and preventing catastrophic leaks. In industrial applications, isolation valves are essential for safely conducting repairs and routine maintenance without disrupting entire systems. For example, in a chemical plant, they enable specific sections to be isolated while others continue operating, maximizing productivity and safety.
In summary, the indispensable role of isolation valves in maintaining the safety, efficiency, and reliability of various fluid systems cannot be overstated. Their intrinsic value is evident from homes to complex industrial infrastructures, helping avert potential hazards and optimize operational capacity. As technological advancements continue to refine their design and functionality, isolation valves remain a cornerstone of modern engineering solutions, embodying reliability and innovation in a constantly evolving landscape. Their universal adoption and adherence to international standards make them a trusted and authoritative component in the world of fluid dynamics.