Gasification equipment has revolutionized the way industries convert organic and fossil fuel-based materials into synthetic gas. This transformation allows for more efficient energy production, aligning with sustainable practices and reducing carbon emissions. When diving into the world of gasification, understanding the fundamentals, technological advancements, and potential applications becomes paramount.
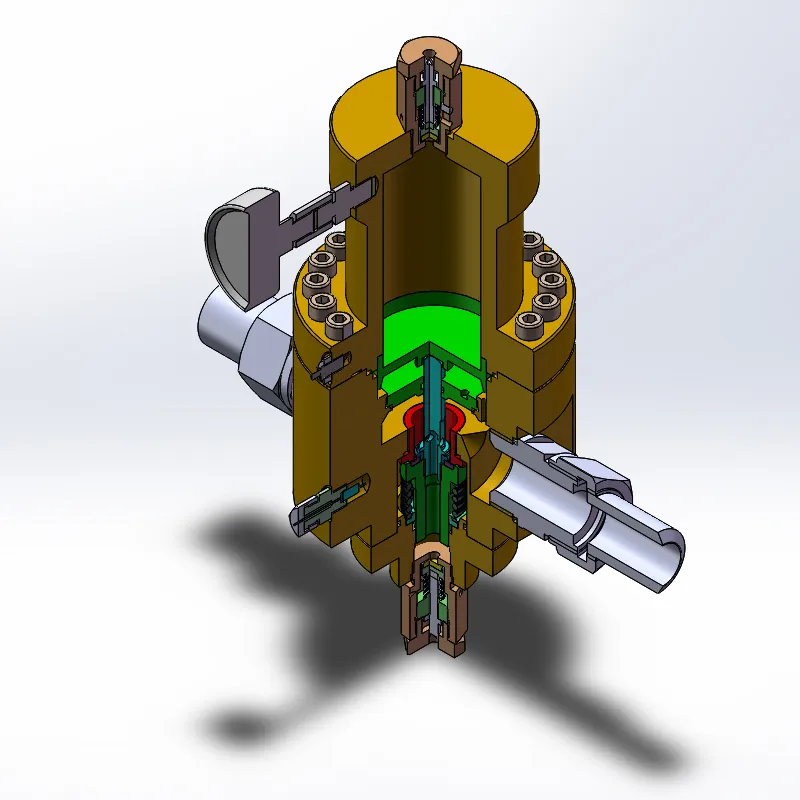
To appreciate the impact and utility of gasification equipment, it's crucial to explore both the design and operation principles. At its core, gasification transforms solid or liquid substrates into syngas (a mixture of hydrogen, carbon monoxide, and often some carbon dioxide) through a high-temperature, oxygen-deprived environment. This process theoretically converts the energy potential from the feedstock into a versatile feedgas that can power turbines, produce electricity, or serve as an intermediate for chemical synthesis.
Gasification equipment typically consists of essential components such as feed systems, gasifiers, gas cleaning units, and heat recovery systems. Each component plays a pivotal role in ensuring the process is efficient, safe, and environmentally friendly. Modern gasifiers are equipped with cutting-edge technologies, including fluidized beds or entrained flow systems, which optimize the contact between the heat source and the material being gasified.
This leads to a more complete conversion and higher quality of the resultant gas.
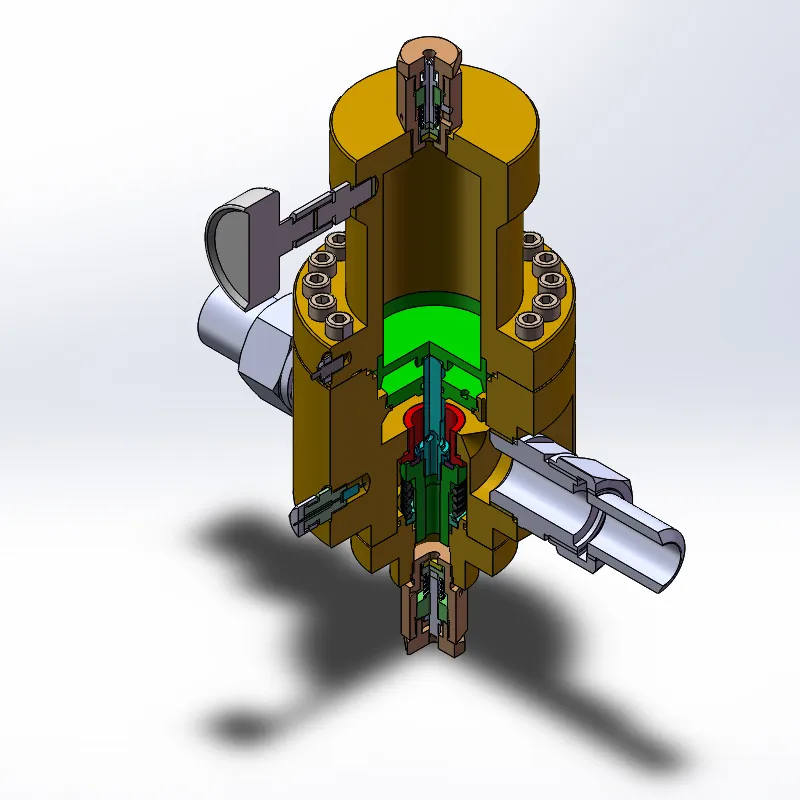
In terms of expertise, it's essential to understand the variations in gasification technologies. Fixed-bed, fluidized-bed, and entrained-flow reactors each have their unique advantages and limitations, dictated by feedstock type, output requirements, and scalability needs. Fixed-bed systems, for example, are adept at handling solid fuels with minimal processing but may not achieve the high conversion efficiencies of fluidized systems. On the other hand, entrained-flow systems, requiring finely ground feeds, provide rapid and complete conversion, making them suitable for large-scale applications.
A deep dive into the operational experience reveals that success in gasification depends largely on the nature of the feedstock. Biomass, coal, and municipal solid waste each present unique challenges and opportunities. Biomass gasification, for instance, often capitalizes on renewable materials, yet requires robust pre-treatment processes to enhance gas yield and quality. Coal, albeit less environmentally favorable, is still prominent due to its energy density and abundance. Strategies for coal gasification include careful management of ash content and sulfur removal to mitigate environmental impacts.
Lubrication equipment
Authoritativeness in this field often belongs to firms and institutions that lead the charge in technological innovations. Companies that design and manufacture gasification equipment, such as Siemens, GE, and various others, drive progress in efficiency and environmental compatibility. Moreover, academic and governmental research centers contribute by exploring newer methods of gas cleanup, carbon capture, and overall process optimization, thus enhancing the viability of gasification as a green energy solution.
When it comes to trustworthiness, it is vital for customers to consider equipment providers with proven track records. Transparency in performance data, warranties, and after-sales support can significantly influence trust. Independent certifications and adherence to international standards like ISO further attest to the equipment’s quality and reliability.
Potential applications of gasification are as diverse as the feedstocks used. Beyond energy production, syngas can be converted into liquid fuels through Fischer-Tropsch synthesis, used as inputs for ammonia production, or transformed into methanol, an important industrial chemical. The flexibility of syngas underscores the strategic advantage of gasification, particularly in a world moving towards energy diversification and security.
To conclude, gasification equipment stands as a cornerstone in the transition to more sustainable and efficient energy systems. By leveraging a thorough understanding of the technologies, operational challenges, and supplier credentials, stakeholders can effectively harness this power for varied applications. As industries continue to prioritize reducing their carbon footprint, the role of gasification will undoubtedly expand, fostering innovation and driving economic growth in tandem with environmental stewardship.