In the rapidly evolving landscape of industrial applications, particularly those involving petrochemicals and natural gas processing, the role of a reliable gas filter [مرشح الغاز] cannot be understated. A gas filter is a critical component that ensures the purity and quality of the processed gas, ultimately affecting the efficiency, safety, and cost-effectiveness of the entire operation.
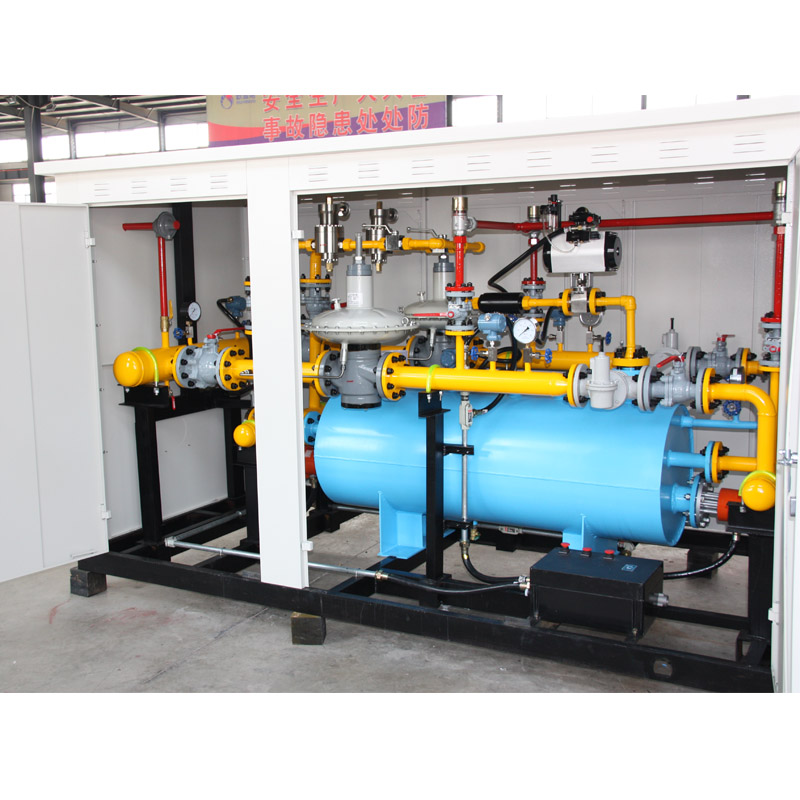
Drawing from real-world experience, the importance of selecting the right gas filter is akin to securing the foundational stone of a building. The experience of industry professionals unanimously underscores that gas filters play a pivotal role in preventing contaminants and particulates from tarnishing the quality of the end product. Contaminants, ranging from dust particles to complex hydrocarbons, pose a significant risk to equipment integrity and operational efficiency. A robust gas filtration system eliminates these threats, prolonging equipment life and enhancing output quality.
When delving into the expertise surrounding gas filters, it becomes imperative to examine the technical specifications that differentiate one filter from another. Filters are often categorized based on their material construction, operational pressure range, temperature handling capabilities, and the size of particles they can efficiently filter. Advanced materials such as Teflon, stainless steel, and specialized polymers are now being used to construct filters that can withstand extreme conditions without losing efficacy. Furthermore, experts emphasize that understanding the specific requirements of your application – such as the chemical composition of the gas stream, the desired purity level, and the maximum allowable pressure drop – is essential in choosing the most suitable gas filter.
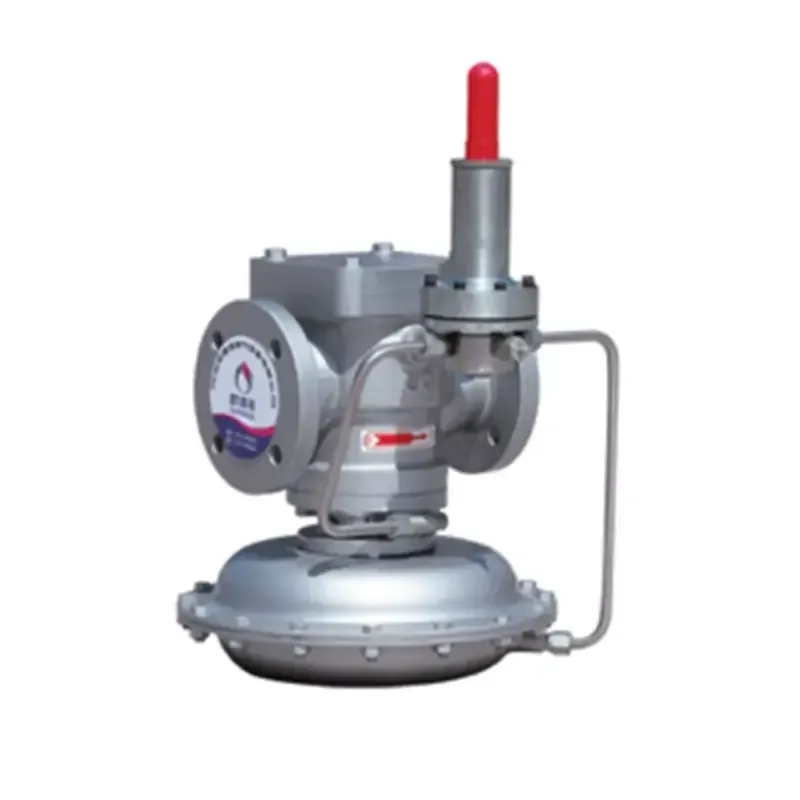
From an authoritative standpoint, industry standards like those outlined by the American Society of Mechanical Engineers (ASME) and the International Organization for Standardization (ISO) guide the production and testing processes of gas filters. Compliance with these standards is not just a marker of quality but an assurance of safety and reliability. Industry leaders in gas filtration emphasize the significance of adhering to these guidelines, as they are designed to cater to the universal benchmarks of safety and performance, thus establishing a global trust in the products manufactured under such standards.
Natural gas filter
Trust in the realm of gas filtration is built over time through consistent performance and positive end-user feedback. Real-world reliability testing and user testimonials are indispensable in corroborating a filter's claim. Users often report that filters with superior adaptability to different operating conditions and those requiring less frequent maintenance tend to yield higher satisfaction and economic efficiency. Moreover, the incorporation of digital monitoring systems in modern gas filters has enhanced their trustworthiness by enabling predictive maintenance, thereby minimizing downtime and preventing potential system failures.
Ultimately, selecting the right gas filter transcends simple purchase decisions; it is a strategic investment towards operational excellence. Industry practitioners suggest that while initial costs might appear higher for top-tier filters, the long-term benefits – including extended equipment lifespan, reduced maintenance costs, and improved throughput quality – significantly outweigh the initial expenditure.
To conclude, the nuanced world of gas filtration requires a balance of practical experience, technical expertise, adherence to established standards, and a demonstrated commitment to trustworthy practices. As industries strive for greater efficiency and sustainability, the ongoing evolution of gas filter technology will undoubtedly play a critical role in shaping the future of gas processing methodologies.