The world of fluid control systems is intricate, with precise engineering and cutting-edge technology at its core. At the heart of many such systems is the vital component known as the صمام تنظيم, or control valve. Understanding the nuances of this component helps in optimizing fluid systems for industries ranging from oil and gas to water treatment and manufacturing.
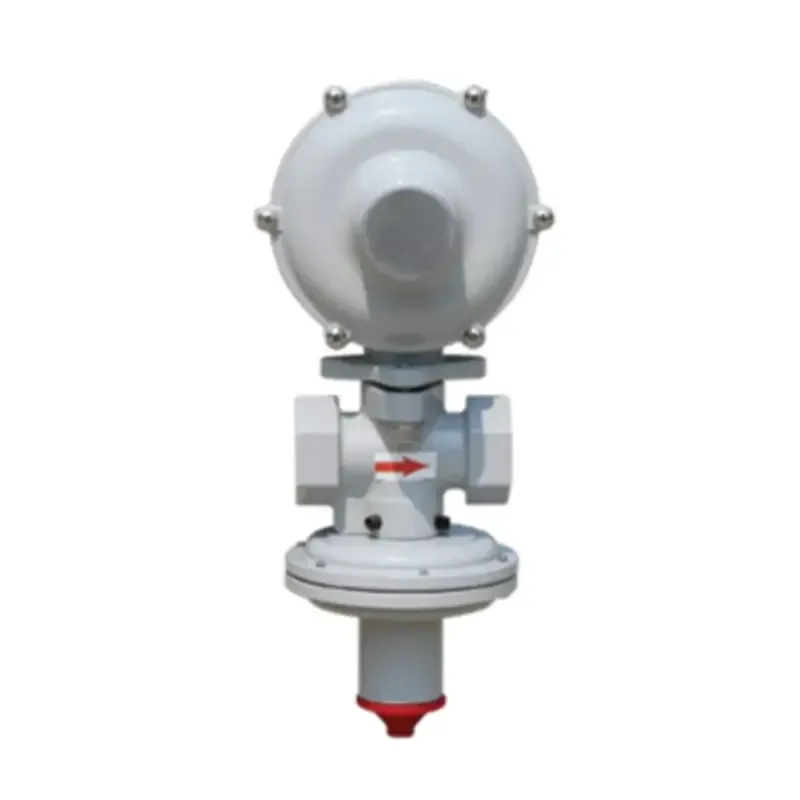
Control valves are instrumental in modulating fluid flow, pressure, and temperature across a system by varying the size of the flow passage.
Their design allows for precise regulation, ensuring that systems operate efficiently and safely. The primary function of a control valve is to receive a control signal and adjust the flow accordingly, maintaining the desired setpoint in the process.
With decades of rapid advancements in technology, modern control valves come equipped with smart features. These include digital control interfaces, IoT capabilities, and advanced diagnostic systems that predict maintenance requirements and optimize performance. This evolution reflects the broader trend towards Industry 4.0, where automation and data exchange in manufacturing technologies are essential for efficiency.
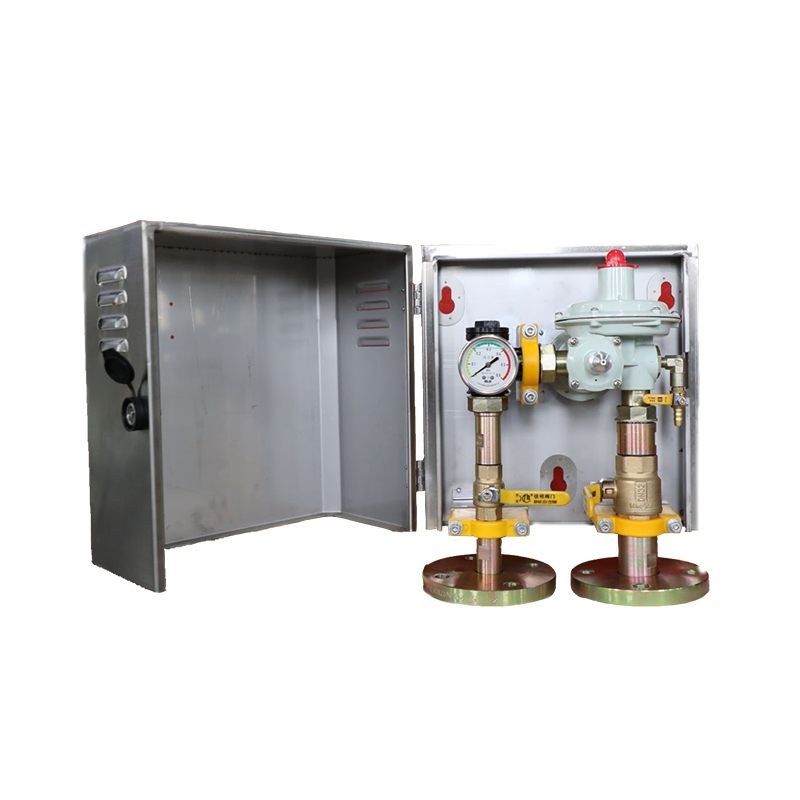
Experience with control valves shows their critical role in ensuring system longevity and reliability. For industries where process control is vital, selecting the right type of control valve can make a significant difference. For instance, in the chemical industry, precise control of reaction conditions is necessary to ensure product quality and safety. Control valves, tailored to withstand harsh chemical environments, provide the reliability needed in these demanding applications.
Expertise in control valve technology involves understanding the variety of valve types available globe valves, butterfly valves, ball valves, and diaphragm valves, among others. Each type is suited to specific applications, dictating factors such as material compatibility, pressure drops, and sealing technology. Selecting the right valve requires a detailed analysis of system requirements, including flow characteristics, pressure ratings, and temperature ranges, as well as understanding the process's dynamic behavior.
regulating valve
Authoritative knowledge is essential when discussing control valves, as these components significantly impact a system's operational efficiency and safety. Insights from industry leaders and engineers highlight the need for a comprehensive approach when integrating control valves into a system. This involves not just the mechanical endurance of the valve itself but also the integration with plant control systems and compliance with industry standards and regulations.
Trustworthiness is paramount in the context of industrial components like control valves. Suppliers of these valves must provide detailed documentation and testing results, ensuring that the products meet rigorous quality and safety standards. Additionally, end-users should engage with trusted brands and manufacturers who have a proven track record of delivering reliable and robust valves that perform under varying conditions.
Maintenance and regular inspection of control valves are crucial for sustaining their performance and extending their operational life. Best practices recommend periodic checks of the valve components such as actuators, seals, and seats, as well as calibration of sensors and control interfaces. Employing predictive maintenance strategies, utilizing advanced data analytics from smart valve technology, ensures that potential issues are identified before they result in system downtime.
In conclusion, the control valve, or صمام تنظيم, is a critical component for efficient fluid control within industrial systems. Its selection and maintenance are vital for ensuring process safety and operational efficiency. By leveraging the latest advancements in valve technology, industry professionals can optimize their systems for improved performance, reduced operational costs, and enhanced safety, all while adapting to the rapid evolutions within their respective fields.