In the realm of measurement systems, accuracy and precision hold paramount significance in the world of industrial and scientific applications. Measurement systems form the backbone of processes from manufacturing to laboratory experiments, and the advancements in this field have revitalized how results are documented and outcomes are executed.
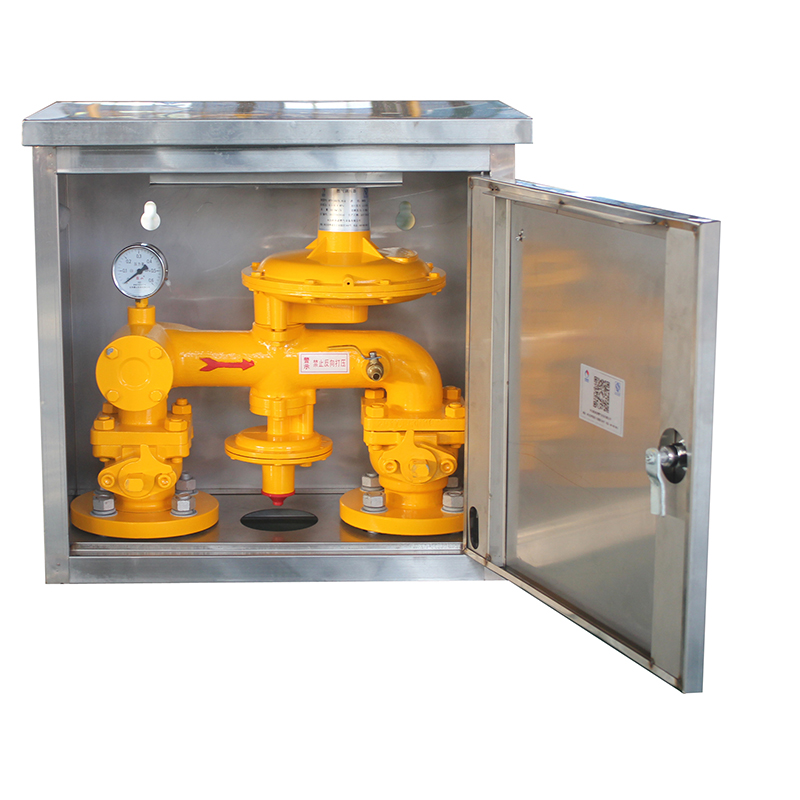
With decades of research and experience, the evolution of measurement systems has transcended traditional methods, incorporating state-of-the-art technology that enhances efficiency and reliability. These systems not only accommodate dynamic variables but also ensure integrity and consistency, crucial for industries where even the slightest variance can lead to substantial impact.
Digital Transformation in Measurement Systems. The advent of digital technology has redefined measurement systems. This change is not merely about replacing analog with digital; it involves the integration of Internet of Things (IoT) and artificial intelligence that allows devices to communicate seamlessly. These smart systems address several industry pain points, such as real-time data analysis, predictive maintenance, and seamless calibration procedures.
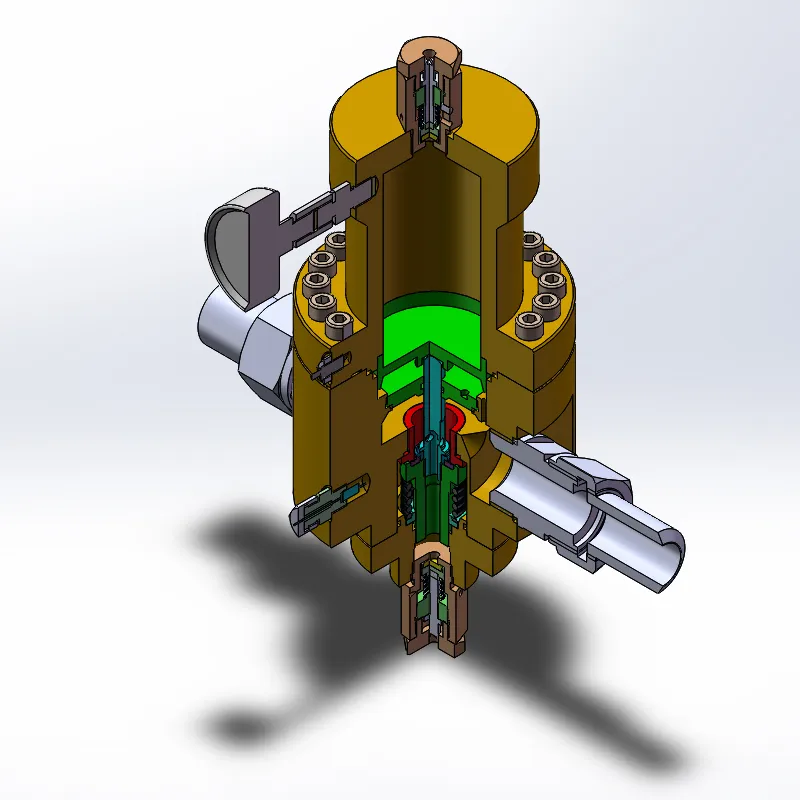
Scientific research has traditionally relied on analog measurement instruments, known for their robust operation but limited by range and accuracy. Modern digital systems take one step further by offering higher sensitivity and quicker response times. For instance, digital micrometers and calipers are indispensable in sectors which demand exacting precision, offering error margins that are almost negligible.
The Role of Calibration in Ensuring Accuracy. Calibration ensures that measurement systems retain their accuracy over time, which is pivotal for maintaining the integrity of the results. Automated calibration processes allow these systems to self-correct, significantly reducing human error. The ability of these systems to recalibrate on-the-fly alerts users of potential deviations before they impact the broader operation.
In industries such as aerospace or automotive, where precision engineering is non-negotiable, the repercussions of using uncalibrated instruments can be catastrophic. Hence, manufacturers are increasingly investing in automatic calibration solutions which not only bolster accuracy but also enhance productivity with minimal downtime.
Measurement systems
Legal and Regulatory Compliance. Compliance with international standards and regulatory mandates is another key aspect that measurement systems must adhere to. These systems often underpin processes that influence safety and quality; thus, abiding by standards such as ISO, ANSI, or NIST is crucial. The integration of regulatory compliance within the design and implementation phases of measurement systems ensures that operations align with legal requisites, providing a double fold advantage—ensuring superior product quality and circumventing legal liabilities.
Case Studies and Real-World Applications. Explore industries which have notably benefited from advanced measurement systems. The pharmaceutical industry, for example, leverages high-precision measurement systems for dosing and compounding medications to enhance patient safety. These advancements have revolutionized how drugs are formulated and administered, significantly reducing human error.
A dive into aerospace reveals where measurement systems facilitate the scrutinization and validation of even the smallest components, ensuring they meet rigorous standards. The incorporation of highly sophisticated systems, such as laser measurement devices, permits the examination of each particular metric, guaranteeing the structural integrity of aircraft components.
Future Prospects and Innovations. The future of measurement systems is set on a trajectory of extensive innovation. With upcoming technologies such as quantum metrology and nanotechnology foreseeing simplification of intricate measurement tasks, industries can expect unprecedented precision levels. Furthermore, the rise of cloud-based systems is revolutionizing data management and accessibility, enabling organizations to streamline processes and achieve outstanding operational efficiencies.
Concluding Insights. The amalgamation of groundbreaking technology with traditional principles of measurement systems has ushered a new era of measurement standards. These transformations are not merely supplementary but quintessential to the sustenance and growth of industries worldwide.
From ensuring adherence to international mandates to empowering industries through precise data analytics, the innovation in measurement systems embodies a confluence of experience, expertise, authority, and trustworthiness. This is not merely an evolution, but a necessary progression to meet the demands of modern technology and global industry standards. The adaptability and precision offered by these contemporary systems irrevocably enhance operational productivity and pave the way for a future underscored by technological excellence.