Basket strainers, widely recognized in various industries for their efficiency in filtering particulates from a liquid flow, serve an essential role in safeguarding machinery and systems from damage. These devices are indispensable for industries ranging from water treatment to chemical processing and even in culinary applications. But what exactly makes a basket strainer an indispensable component in such a wide array of applications? Understanding the intricacies of basket strainers can not only enhance system longevity but can also optimize performance and reduce maintenance costs.
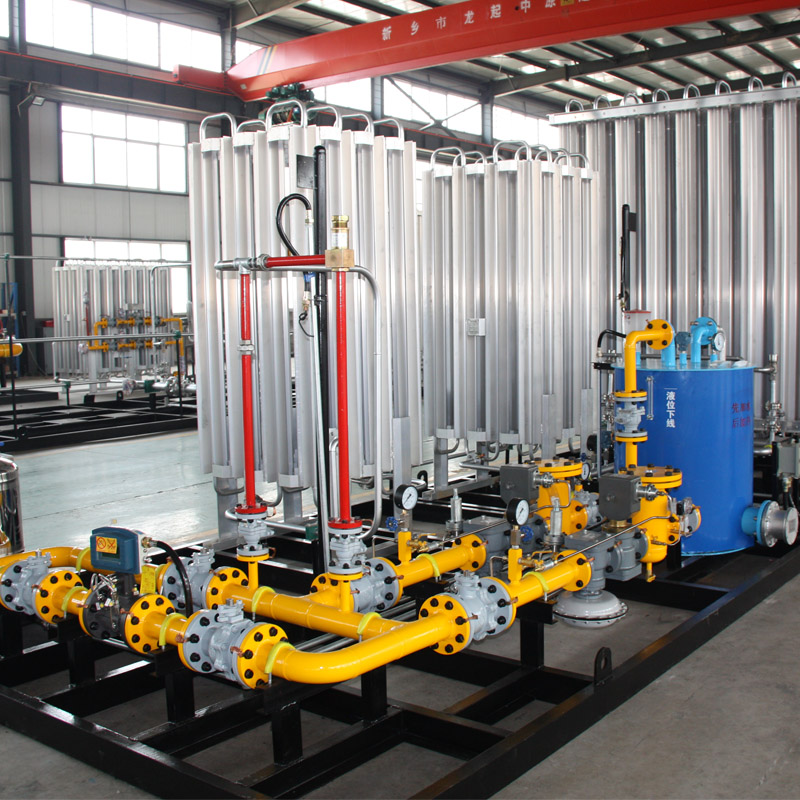
At the core of the basket strainer's design is its ability to trap debris and unwanted particles, thereby ensuring that only clean fluid continues through a pipeline. This seemingly simple function helps prevent damage to downstream equipment such as pumps, valves, and other essential components. By eliminating contaminants early in the process, basket strainers significantly reduce the risk of costly repairs and downtimes.
Selecting the right basket strainer for your specific application requires a nuanced approach. Key considerations include the nature of the fluid, the type and size of particulates to be filtered, and the required flow rate. For instance, in a petrochemical plant, the strainer must be built to withstand high pressures and corrosive materials. In this context, stainless steel or high-nickel alloy basket strainers are preferable due to their durability and resistance to chemical attacks.
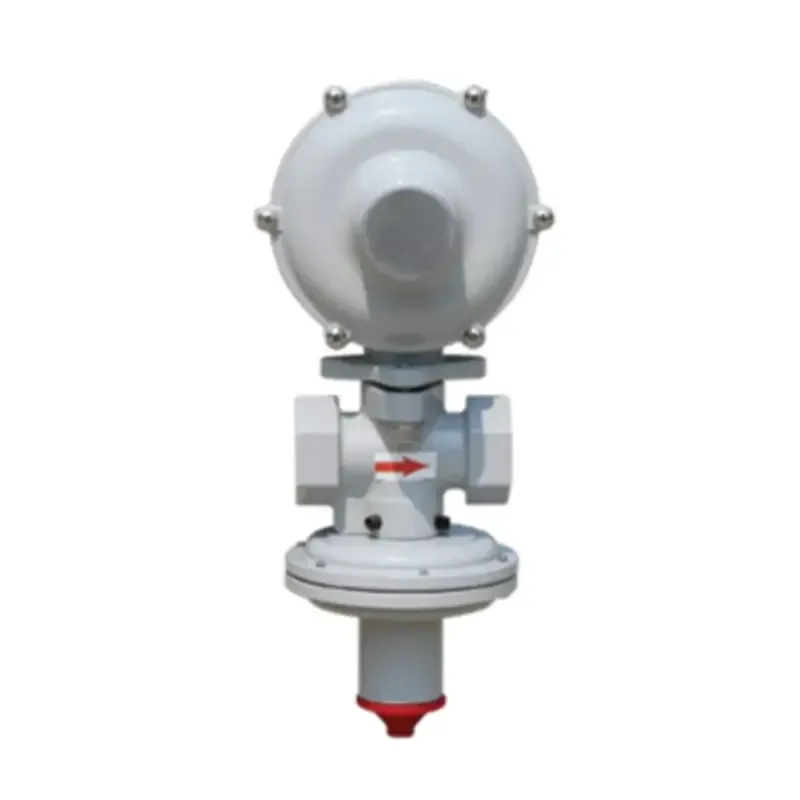
Beyond material choice, the basket strainer's design intricacies play a pivotal role in its efficiency. A well-designed strainer maximizes the surface area through which the fluid can flow, reducing pressure drop and allowing for optimal filtering performance. This design efficiency ensures that systems can function at their intended capacity without undue strain or energy consumption.
Installation of a basket strainer requires careful consideration. Proper positioning within a pipeline system is crucial for maximizing its effectiveness. Ideally, a basket strainer should be placed upstream of critical equipment to serve as the first line of defense against debris. Furthermore, ease of access is important for routine maintenance, as basket strainers require periodic cleaning to maintain their efficiency.
Maintenance routines for basket strainers play a crucial role in safeguarding system performance. Regular inspection and cleaning schedules prevent the buildup of debris, which can compromise fluid flow and increase pressure drops. Utilizing a monitoring system to detect when a strainer becomes clogged can automate this process, ensuring timely maintenance without the need for constant manual checks.
basket strainers
Industries utilizing basket strainers experience long-term benefits that include reduced operating costs and extended lifespan of machinery. For example, in the food and beverage industry, where contamination control is critically important, basket strainers ensure liquid ingredients are free from impurities, contributing to the high quality of the final product. Here, strainers are crafted from food-grade materials to comply with stringent health standards.
In the realm of water treatment, basket strainers function as a preliminary filtering stage, often serving as the first barrier against sediment and debris. This initial filtration significantly enhances the efficiency of subsequent water purification processes, such as reverse osmosis or membrane filtration systems.
Notably, basket strainers also contribute to environmental sustainability. By ensuring efficient operation of systems, they help conserve energy and resources, aligning with global efforts to improve industrial sustainability practices. In wastewater treatment facilities, efficient filtration reduces environmental impact by ensuring cleaner effluents and reducing the volume of waste material needing disposal.
As industry standards and regulatory requirements continue to evolve, the role of basket strainers is more critical than ever. Manufacturers are now innovating with advanced materials and smart technologies to enhance the performance of these devices. Features such as automated cleaning and digital monitoring for predictive maintenance represent the future of strainer technology.
Investing in high-quality, reliable basket strainers is essential for businesses looking to optimize operational efficiency while ensuring compliance with industry regulation. By choosing the right strainer for specific applications and maintaining a diligent upkeep schedule, industries can significantly enhance their operational processes and safeguard critical infrastructure from unnecessary wear and tear.