Cyclone separators, known for their efficiency in removing particulates from fluids, have emerged as a vital component in various industries. Their unique design and functionality make them indispensable for companies looking to enhance operational efficiency while maintaining environmental compliance. The following insights delve into the intricacies of cyclone separators, offering both expert knowledge and practical experiences that underscore their indispensability in modern industrial applications.
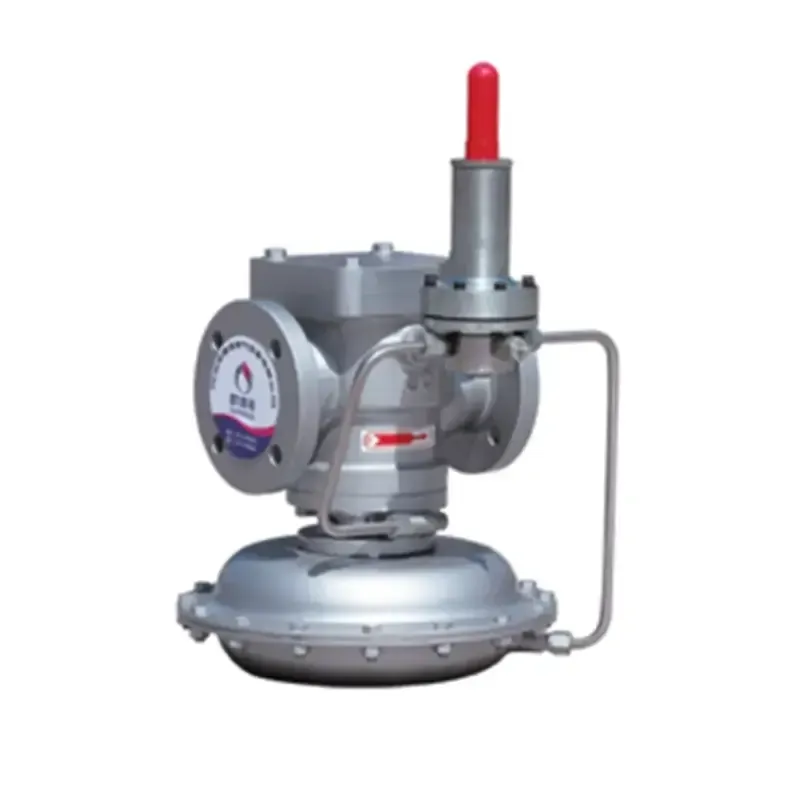
Cyclone separators operate on a simple yet effective principle centrifugal force. By exploiting this force, these devices separate particulates from liquids or gases without the need for filters, offering a low-maintenance solution. This operational principle not only makes them cost-effective but also environmentally friendly, as they don't require disposable filters, reducing waste generation—a topic of increasing importance in today's sustainable business practices.
Industrial sectors such as oil and gas, pharmaceuticals, and automotive industries have shared valuable firsthand experiences on how cyclone separators have enhanced their operational efficiencies. For instance, in the oil and gas industry, cyclone separators significantly reduce the wear and tear on downstream processing equipment by removing abrasive particles from the crude fluid streams. This leads to a reduction in maintenance costs and downtime, providing a compelling financial incentive for their adoption.
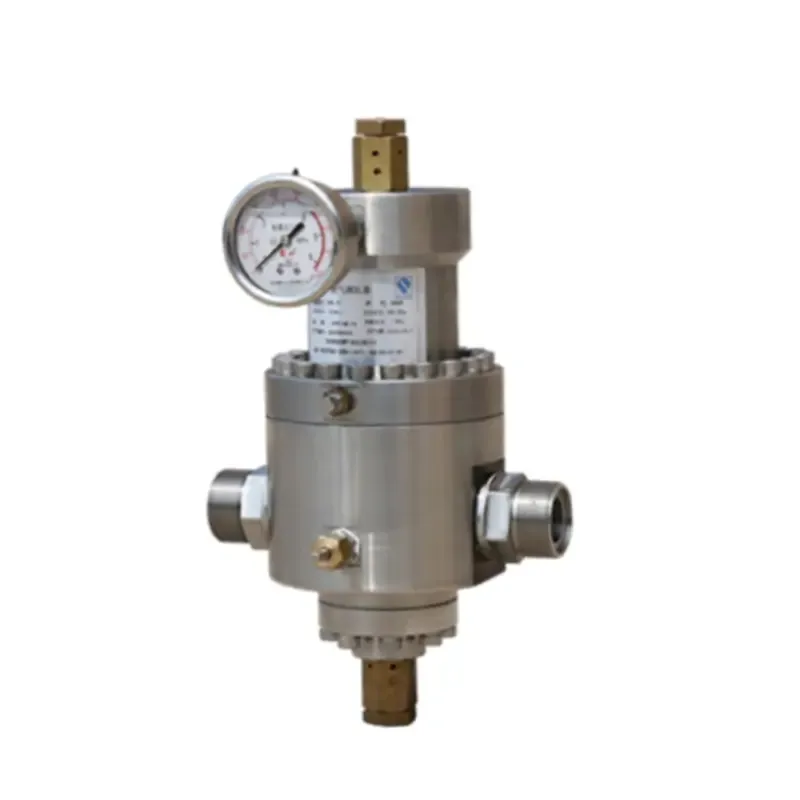
Pharmaceutical manufacturers use cyclone separators to ensure the purity and quality of their products. By efficiently removing particulate contaminants during the manufacturing process, these separators play a crucial role in adhering to strict regulatory standards. This ensures product safety and efficacy, bolstering consumer trust—a cornerstone for any pharmaceutical company.
cyclone separator
When it comes to expertise, designing a cyclone separator requires a deep understanding of fluid dynamics. Engineers must consider factors such as volumetric flow rate, particle size distribution, and fluid viscosity to tailor a separator to specific industrial needs. Companies can avail themselves of customized cyclone separators, engineered to accommodate their unique operational challenges, which in turn enhances the separator’s performance comprehensively.
Authoritative voices in the engineering domain assert that regular maintenance of cyclone separators, although minimal, is paramount for optimal performance. A consistent schedule of inspection and cleaning prevents the buildup of particles within the separator, which can compromise its efficiency over time. Thus, adopting a preventive maintenance strategy is advised, one that leverages the expertise of trained technicians to ensure seamless operations.
The trust in cyclone separators is further solidified by their track record in enhancing environmental compliance. With stringent regulations aiming to minimize industrial emissions, cyclone separators help companies meet these standards without significant investments in complex filter systems or extensive effluent treatment processes. Their ability to operate effectively under demanding conditions makes them a reliable component in emission control strategies.
In conclusion, cyclone separators are not just a piece of equipment; they are an amalgamation of innovative engineering, practical utility, and sustainable practice. Their role in optimizing industrial processes is backed by extensive expertise and a proven track record of delivering value in complex operational landscapes. As industries continue to pivot towards more sustainable and efficient practices, the importance of such reliable and effective solutions cannot be overstated. Investing in cyclone separators is an investment in efficiency, compliance, and ultimately, business success. With industry leaders continually validating their effectiveness, cyclone separators remain a trusted choice for companies aiming to achieve operational excellence and environmental stewardship.