Gas coalescers are pivotal components in various industrial processes, where the purification of gas streams is crucial. These devices play a critical role in ensuring that gases are free from liquid aerosols and particulate contaminants, which can cause inefficiencies, safety hazards, or costly downtime if left unchecked.
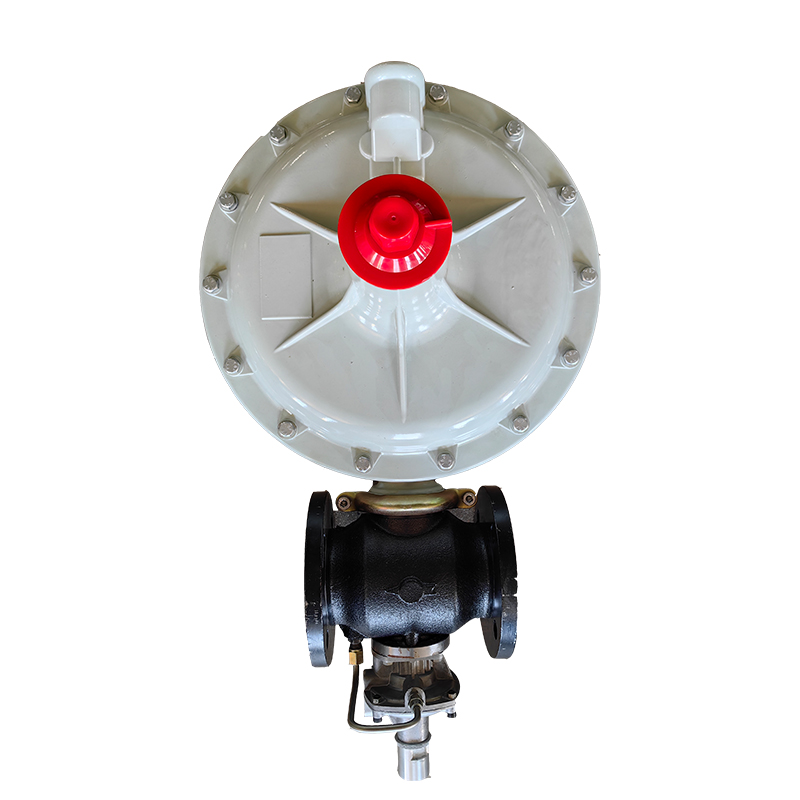
Experience tells us that the deployment of an effective gas coalescer system can significantly enhance operational efficiencies. In industries such as natural gas processing, petrochemicals, and air separation, these systems serve as guardians of purity, ensuring that only clean gas progresses through the production line. Field operators and engineers have consistently reported lower maintenance costs and extended equipment longevity following the integration of premium gas coalescers into their facilities.
From a technical perspective, gas coalescers operate on intricate principles of filtration and coalescence. Their design typically incorporates a multi-layered filter medium, often using micro-fiber technology, which effectively captures and wicks away liquid droplets. As gas passes through, fine droplets coalesce into larger ones, making it easier for them to separate from the gas stream due to gravity or centrifugal forces. Expertise in selecting the right type of coalescer—whether vertical, horizontal, or cartridge-based—depends on process conditions, the nature of the contaminants, and the specific requirements of the gas stream.
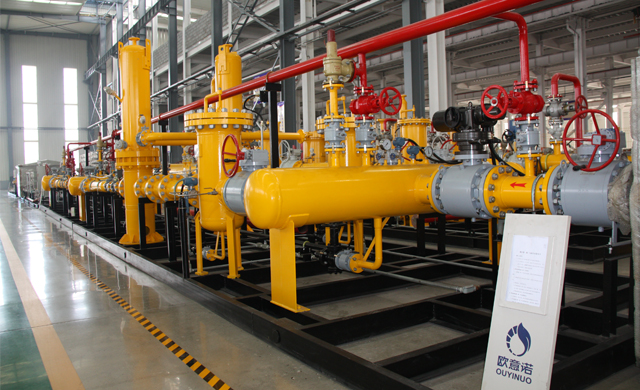
gas coalescer
The authoritative voice in gas filtration technology often emphasizes the importance of matching coalescer materials to the operational environment. Material selection can range from stainless steel for corrosive environments to advanced polymers for high-temperature applications. Leaders in this domain, such as Pall Corporation and Parker Hannifin, recommend routine inspections and replacements based on pressure drop measurements across the coalescer unit. Keeping in tune with the latest technological advancements and research findings can aid in unlocking additional efficiency and reliability gains.
Trustworthiness in gas coalescer systems is bolstered by rigorous compliance with industry standards. Manufacturers are compelled to adhere to specifications such as ASME VIII and API 1581, which guarantee that these units withstand operational pressures and provide adequate separation efficiency. End users rely on performance data assessed under controlled conditions, often simulated to reflect real-world operational challenges, ensuring that the gas coalescer will meet expectations when challenged by varying flow rates or unexpected particulate surges.
In sum, the integration of a well-chosen gas coalescer not only enhances the quality and safety of gas handling processes but also demonstrates fiscal prudence through reduced operational costs and protective measures against contamination-related complications. As industries evolve, adopting newer, more advanced filtration technologies will likely further simplify maintenance practices and bolster efficiency—a continual journey towards perfecting gas purification through innovative coalescer designs and applications. Achieving this level of optimization is not only a technical challenge but also an investment in operational trustworthiness and reliability.