Exploring the Essential Role of Gas Coalescers in Optimizing Industrial Applications
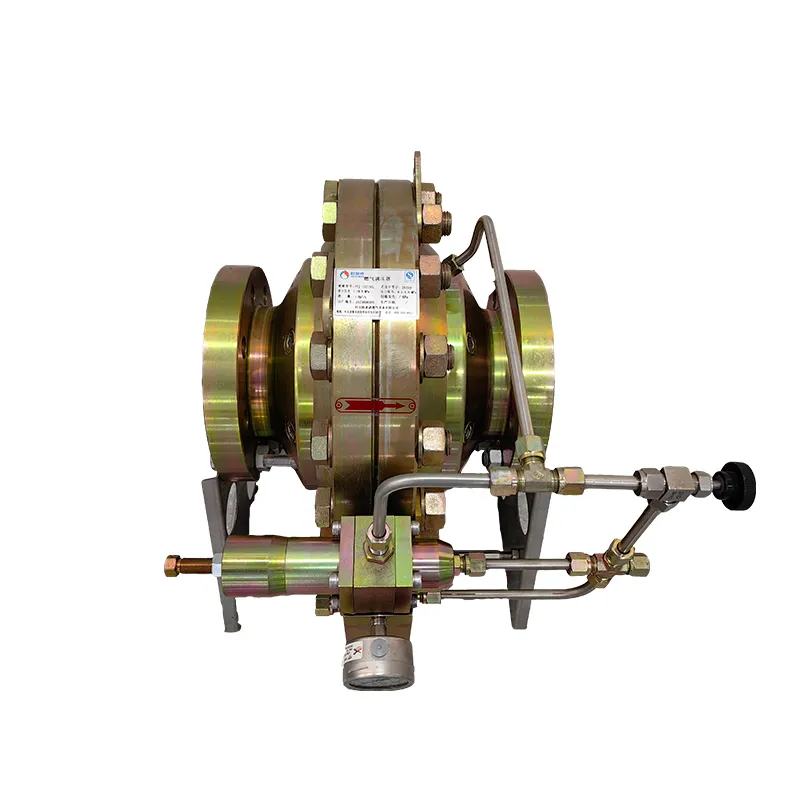
In the world of industrial applications, ensuring the purity of gases is paramount for the smooth operation and longevity of equipment. Gas coalescers have emerged as vital components in various industries, offering high-efficiency solutions for gas filtration systems. With technological advancements and the increasing demand for cleaner operations, understanding the significance of gas coalescers has never been more crucial.
Gas coalescers are intricately designed filtration systems that focus on the removal of liquid contaminants and solid particles from gas streams.
These contaminants, if not addressed, can lead to corrosion, inefficiency, and failure of machinery. Coalescers operate by combining multiple filtering mechanisms - including impaction, interception, and diffusion - to effectively eliminate these impurities.
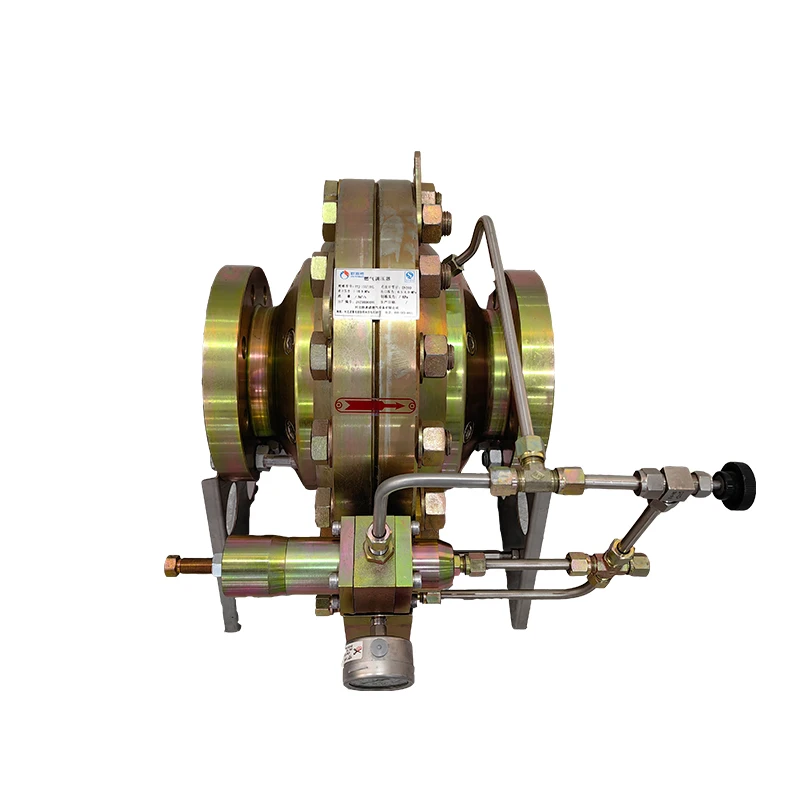
A key feature that sets gas coalescers apart is their multi-layered media design. This sophisticated construction is adept at capturing even the finest particles, ensuring that the output gas is free from impurities. By employing surface filtration and depth filtration techniques, coalescers provide a dual action that not only traps particles on the surface but also captures them within the filter media, extending their effectiveness and durability.
The efficiency of a gas coalescer largely depends on its design and the specific application it serves. Industries such as petrochemicals, natural gas processing, and refineries heavily rely on gas coalescers to maintain the integrity of their operations. These sectors face unique challenges, including the handling of complex mixtures and harsh chemical environments. The right coalescer will cater to these specific needs, offering customized solutions that enhance performance and reliability.
gas coalescer
One notable advancement in gas coalescer technology is the development of materials that withstand extreme temperatures and aggressive chemicals. Modern coalescers are built using materials like stainless steel, synthetic fibers, and polymers, which are engineered to resist degradation and optimize longevity. This ensures that the coalescers remain effective over long operational periods, reducing the need for frequent replacements and minimizing downtime.
The installation of gas coalescers also contributes significantly to improved energy efficiency and cost savings. By ensuring cleaner gas streams, they prevent the fouling of downstream equipment, thereby reducing energy consumption and maintenance costs. The return on investment for industries employing gas coalescers is realized through prolonged equipment life, reduced operational hiccups, and compliance with stringent environmental regulations.
Trustworthiness in gas coalescer performance can be assessed through rigorous testing and certifications. Reputable manufacturers subject their products to thorough evaluations to meet international standards, such as ASME and ISO, ensuring that users can confidently rely on the quality and efficiency of their coalescers. Credible third-party certifications further enhance the authority of these products in the market, reassuring clients of their capability to deliver on promises.
In conclusion, gas coalescers are indispensable in modern industrial applications, adapting to evolving demands for cleaner operations and heightened efficiency. Their sophisticated designs and robust materials make them an authoritative choice for industries seeking dependable and high-performance filtration solutions. As industries continue to advance and face new challenges, the role of gas coalescers will only grow, reinforcing their indispensable position in industrial operations globally.