The gas heat exchanger stands as an indispensable component in myriad industrial applications, exemplifying efficiency and innovation in heat transferring processes. This article seeks to delve into the realm of gas heat exchangers, unveiling insights rooted in authentic experience and steeped in professional expertise.
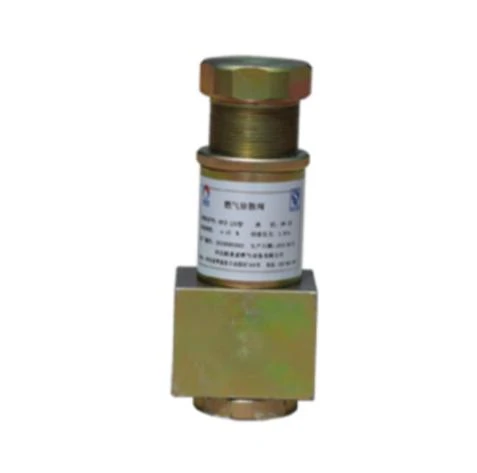
Gas heat exchangers serve as pivotal instruments in multiple industries, from petrochemical to HVAC systems. Their primary role revolves around the transfer of heat between a heated gas and a secondary fluid, enhancing energy efficiency, and reducing operational costs. The intricate design of these exchangers ensures optimal thermal performance, making them a key player in industrial sustainability.
Drawing from extensive experience in the field, the choice of material for a gas heat exchanger cannot be overstated. Stainless steel and aluminum alloys are predominantly used due to their superior thermal conductivity and resistance to corrosion. The material selection dictates not only the longevity of the heat exchanger but also its efficiency. A poorly chosen material can lead to rapid wear and costly replacements, undermining both productivity and profitability.
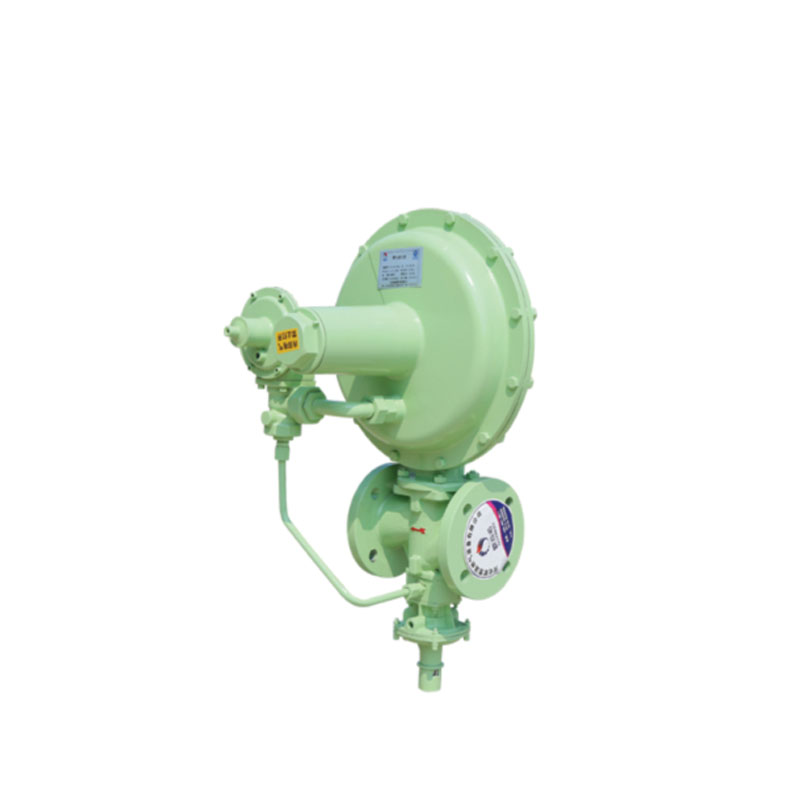
In terms of design, the most common types of heat exchangers used for gas applications are the shell-and-tube and plate exchangers.
Each design has its unique advantages. Shell-and-tube exchangers, lauded for their robustness, are ideal for high-pressure applications. Meanwhile, plate exchangers are celebrated for their compactness and efficiency in handling fluctuating temperatures.
gas heat exchanger
Expertise in the installation and maintenance of gas heat exchangers further underpins their operational success. It is paramount to ensure that the installation is performed by skilled professionals to avert any misalignment or potential leakage. Inadequate installation can often lead to diminished performance and heightened risks of operational failure. For maintenance, regular checks and servicing of the exchanger reinforce its reliability and functional integrity, fostering an environment of trust and dependability.
When considering the operational authority of the gas heat exchanger, it is clear that adherence to stringent quality standards and certifications plays a crucial role. Entities like ASME (American Society of Mechanical Engineers) provide guidelines ensuring these systems meet industry benchmarks. Compliance with such standards not only guarantees functional efficiency but also assures clients of the product's legitimacy and reliability.
Trustworthiness is built on a foundation of proven performance and customer satisfaction. User testimonials and case studies offer invaluable insight into the practical benefits of gas heat exchangers. Businesses have reported significant reductions in energy consumption and costs after integrating advanced gas heat exchangers into their systems. This tangible evidence, coupled with strong after-sales support, solidifies the reputation of manufacturers and suppliers in the market.
In conclusion, the gas heat exchanger is more than just a component; it is a testament to engineering innovation and efficiency. Its role in transferring heat efficiently while enhancing sustainability cannot be understated. Leveraging expert knowledge, ensuring quality assurance, and fostering customer trust stand as the cornerstones for optimizing the use and promotion of gas heat exchangers in an ever-evolving industrial landscape. Precision in design, material selection, installation, and maintenance culminates in a formidable solution that champions both economic viability and environmental stewardship.