Gas heat exchangers play a crucial role in various industrial applications, serving as a linchpin in processes that require the efficient transfer of heat between fluids. Understanding the intricacies of this essential component is key to optimizing operations and ensuring the longevity and efficiency of your equipment. With comprehensive expertise garnered from years of experience in the field, this article aims to unpack the complexities and provide insightful guidance for leveraging gas heat exchangers to their full potential.

Firstly, it's fundamental to distinguish the different types of gas heat exchangers prominent in the industry. These include shell-and-tube heat exchangers, plate heat exchangers, regenerative heat exchangers, and air-cooled exchangers. Each type has its specific design and functional advantages. For instance, shell-and-tube heat exchangers are favored for their robust construction and ability to handle high pressure and temperature conditions, making them suitable for industries such as petrochemicals and power generation.
An essential principle behind the effective operation of gas heat exchangers is understanding the properties of the gases involved, such as specific heat capacity, density, and thermal conductivity.
Gas must be able to transfer heat efficiently for the exchanger to perform optimally. In-depth analysis and precise calculations are required to select the appropriate materials and design configurations that will optimize these properties, ensuring a high rate of heat transfer.
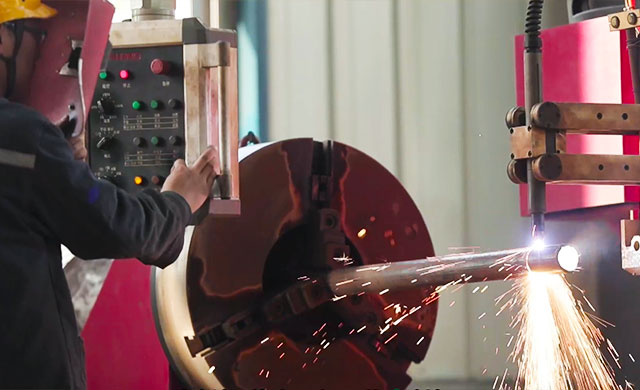
One of the challenges faced by many industries is maintaining the efficiency of gas heat exchangers over time. Fouling, corrosion, and leakage are common issues that, if left unchecked, can lead to significant downtime and costly repairs. Implementing a robust maintenance schedule is critical. This includes regular inspections, cleaning, and the use of corrosion-resistant materials to prolong the life of the exchanger. For cutting-edge solutions, some operators are incorporating predictive maintenance techniques, which utilize sensors and monitoring technology to predict failures before they occur, thereby reducing downtime and maintenance costs.
gas heat exchanger
Advanced technological integration has also revolutionized the use of gas heat exchangers. The incorporation of smart technology allows for real-time monitoring of performance metrics, such as temperature gradients and flow rates. This not only facilitates immediate adjustments but also allows for the collection of data that can be analyzed to improve system design and efficiency further. Leveraging such technology not only enhances operational efficiency but also aligns with modern sustainability and energy-saving mandates, reducing both operational costs and environmental footprint.
Selecting the right gas heat exchanger requires not just technical knowledge but also an understanding of the specific needs of your operation. Consulting with experts who can provide tailored solutions based on a thorough analysis of your current processes and future needs is invaluable. These professionals bring an authoritative understanding of thermodynamics, fluid mechanics, and material science, ensuring that your choice not only meets current industry standards but also anticipates future regulatory changes and technological advancements.
Trust in your equipment's reliability is crucial. This can be bolstered by investing in components from reputable manufacturers known for their engineering excellence and robust quality assurance processes. Verifying certifications, customer testimonials, and compliance with industry standards can offer additional peace of mind. Engaging with manufacturers who provide comprehensive support and warranties is also advisable, as this can significantly mitigate risks associated with unforeseen operational challenges.
In conclusion, gas heat exchangers are indispensable to many industrial processes, and making informed decisions about their selection, maintenance, and integration can have profound effects on operational efficiency and sustainability. By leveraging expert knowledge and cutting-edge technology, businesses can optimize the performance of their heat exchangers, reduce operational costs, and minimize environmental impact, paving the way for continued success in a competitive market.