In the realm of industrial equipment, the gas heat exchanger stands out as a pivotal component that optimizes thermal dynamics within various applications. As industries continually seek efficiency and innovation, understanding the nuances of gas heat exchangers can offer significant advantages in both operational efficiency and sustainability.
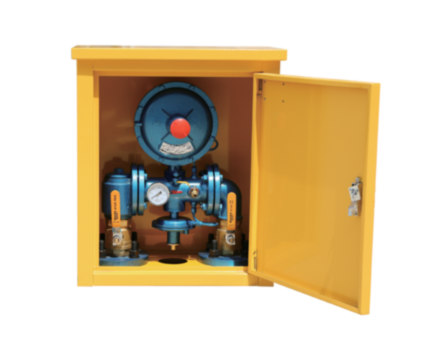
At the heart of a gas heat exchanger is its ability to facilitate the efficient transfer of heat between two or more fluids, crucially without mixing them. This process is vital across sectors such as power generation, chemical processing, and HVAC systems. A gas heat exchanger allows industries to make substantial energy savings, reduce emissions, and enhance process efficiency — ultimately contributing to both economic and environmental goals.
Professional expertise in designing and operating gas heat exchangers is critical.
Selecting the right material is one of the first steps. Typically, materials such as stainless steel, titanium, or nickel alloys are utilized due to their ability to withstand high temperatures and corrosive environments. A poorly chosen material can lead to system failure, increased maintenance costs, and operational downtime, which underscores the importance of material expertise.
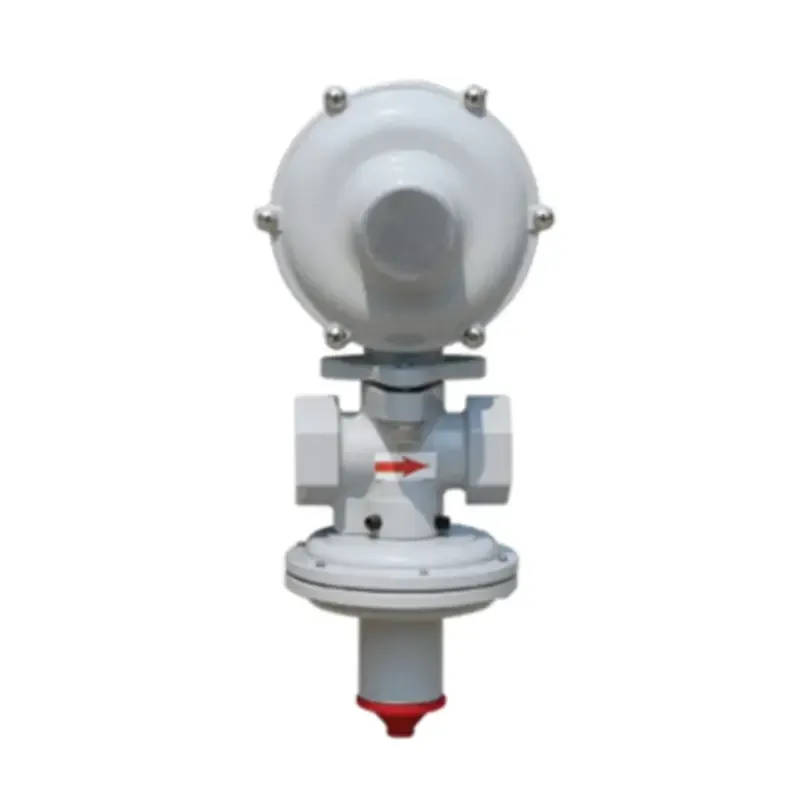
Technical proficiency also comes into play in selecting the appropriate type of heat exchanger for specific applications. Options include shell-and-tube, plate, and finned-tube designs, each offering distinct advantages. For instance, shell-and-tube exchangers are renowned for their robustness in high-pressure applications, whereas plate exchangers offer superior heat transfer efficiency in space-constrained environments. The decision should be informed by the specific thermal requirements and physical constraints of the operation in question.
gas heat exchanger
The authoritative implementation of gas heat exchangers involves a detailed understanding of thermal dynamics principles, such as conduction, convection, and radiation, as well as the characteristics of the gases involved. An adept engineer can manipulate these variables to optimize exchanger performance, maximizing heat recovery and minimizing energy wastage. The ability to model and simulate exchanger operations before actual deployment can significantly enhance system reliability and efficiency.
Trustworthiness in the realm of gas heat exchangers is built on demonstrated success and reliability. Systems must meet stringent industry standards and be tested under a range of operating conditions to ensure safety and durability. Engineers and companies offering heat exchanger solutions should have a verifiable track record of expertise, ideally supported by certifications from relevant industry bodies.
Real-world experience provides invaluable insights into the operation and maintenance of gas heat exchangers. Field engineers often contribute practical knowledge, having faced and overcome challenges such as fouling, which can drastically reduce efficiency. Regular maintenance schedules informed by empirical data are essential to mitigate common issues and extend the life of the equipment.
In conclusion, a profound grasp of the science and engineering behind gas heat exchangers, combined with field-derived experience, ensures these systems operate at peak efficiency, delivering both economic and environmental benefits. As technology evolves, ongoing research and innovation will likely lead to even more advanced systems, further cementing the gas heat exchanger's role in modern industrial operations. For industries looking to optimize their thermal management processes, investing in high-quality gas heat exchangers designed and maintained by reputable professionals is an imperative step forward.