Gas pressure reducing valves are a critical component in many industrial, commercial, and residential applications where regulating and maintaining optimal gas pressure is essential for safety, efficiency, and asset longevity. Understanding the nuances of these devices requires insight into their function, design, and application, which highlights their importance in systems reliant on gas flow.
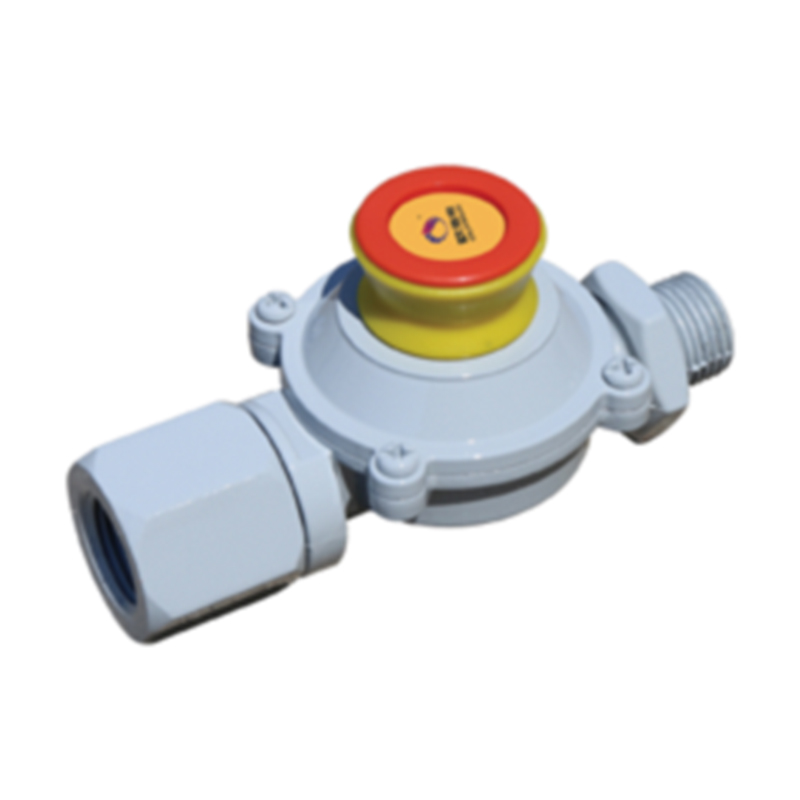
The fundamental role of gas pressure reducing valves is to convert high-pressure gas in the supply system into a lower, more manageable pressure for downstream use. This is crucial for ensuring equipment operates under safe and efficient conditions. For instance, gas appliances in homes, such as heaters and stoves, require a steady, lower-pressure gas supply to function correctly without compromising safety. Similarly, industrial machinery often necessitates precise pressure control to maintain efficiency and prevent damage to sensitive equipment.
Gas pressure reducing valves work through a sophisticated mechanism that can include diaphragms, pistons, and springs. These components work together to reduce the gas pressure from the supply line to the desired level. Valves are designed to react dynamically to changes in downstream demand and upstream supply pressure, adjusting accordingly to maintain a consistent output pressure. This adaptability is essential in applications where gas demand can fluctuate significantly, such as in manufacturing processes or heating systems with variable usage patterns.
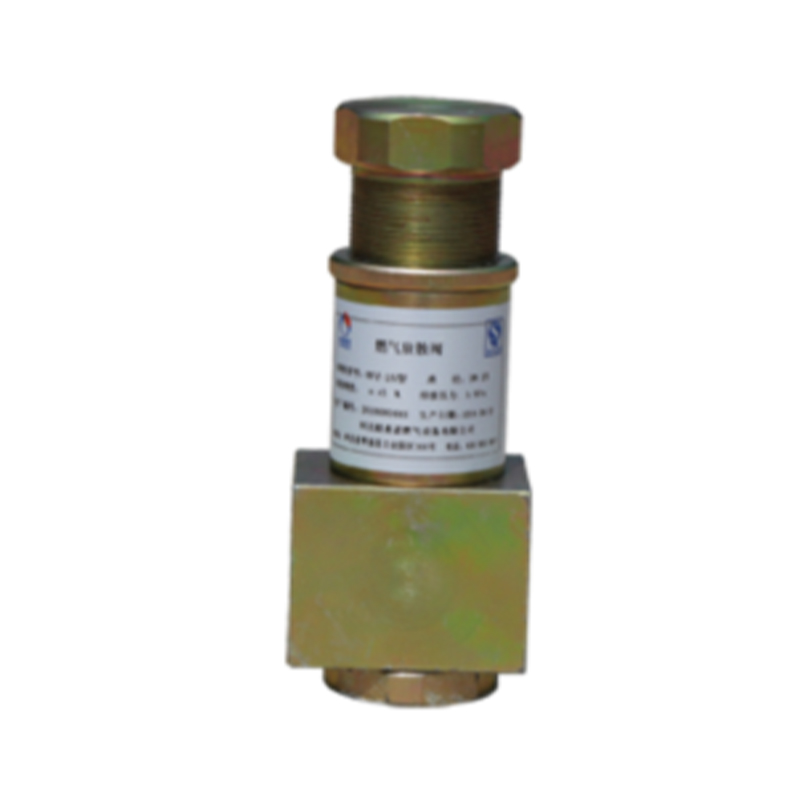
From a materials standpoint, the construction of gas pressure reducing valves often involves durable metals like brass, stainless steel, or specialized alloys designed to withstand the pressures and chemical composition of the gases they regulate. This durability ensures reliability and longevity, which is crucial in industrial applications where failure can lead to significant safety hazards or costly operational downtimes. In addition to their robust physical construction, modern valves may incorporate advanced technologies such as digital monitoring capabilities or automated control systems, enhancing their precision and ease of integration into complex systems.
In terms of installation and maintenance, gas pressure reducing valves require careful consideration. Proper installation is essential to ensure optimal performance and prevent leaks or system malfunctions. This involves correct sizing of the valve based on system demands and ensuring that all connectors and seals are properly secured. Regular maintenance checks, including inspecting for wear and tear and testing output pressure, are also advisable to ensure ongoing functional integrity and safety.
gas pressure reducing valve
Compliance with regulatory standards and guidelines is another critical aspect of operating gas pressure reducing valves. Various national and international standards govern the manufacturing, installation, and maintenance of these devices, ensuring they meet safety and efficiency benchmarks. Organizations like the American National Standards Institute (ANSI) and the International Organization for Standardization (ISO) provide frameworks that manufacturers and operators must adhere to, guaranteeing the products' credibility and reliability.
Real-world experience underscores the importance of choosing the right gas pressure reducing valve for specific applications. Considerations include the type of gas being used, operating temperature ranges, and the specific requirements of the downstream equipment. For instance, a valve designed for natural gas transmission may not be suitable for applications involving specialized gases in laboratory settings or chemical processing facilities. Consulting with experts who understand the nuances of different valves and their applications can provide invaluable guidance in selecting the appropriate product, ensuring not only regulatory compliance but also optimal performance.
Trust in the functionality and reliability of gas pressure reducing valves is founded on several pillars expertise in design and application, stringent manufacturing standards, and comprehensive testing under various conditions. Manufacturers who demonstrate a commitment to these principles tend to have stronger reputations and customer trust. They invest in research and development to innovate and improve valve design, enhancing performance and reliability while reducing costs and environmental impact.
Overall, gas pressure reducing valves are indispensable in numerous applications, offering precise pressure regulation to ensure safe and efficient gas flow. Their selection, installation, and maintenance require significant expertise and adherence to regulatory requirements, underscoring their sophistication and critical role in modern gas handling systems. These factors collectively contribute to the increasing demand and continued innovation in gas pressure reducing valve technology, ensuring they meet evolving industrial and consumer needs.