Gas pressure vessels play a crucial role in various industries where there is a need to store and transport gases under pressure. Particularly in the fields of oil and gas, chemicals, and food processing, the reliability, safety, and efficiency of these vessels are paramount. As an experienced professional in this domain, I can attest to the nuanced engineering and precise standards that govern their design and usage.
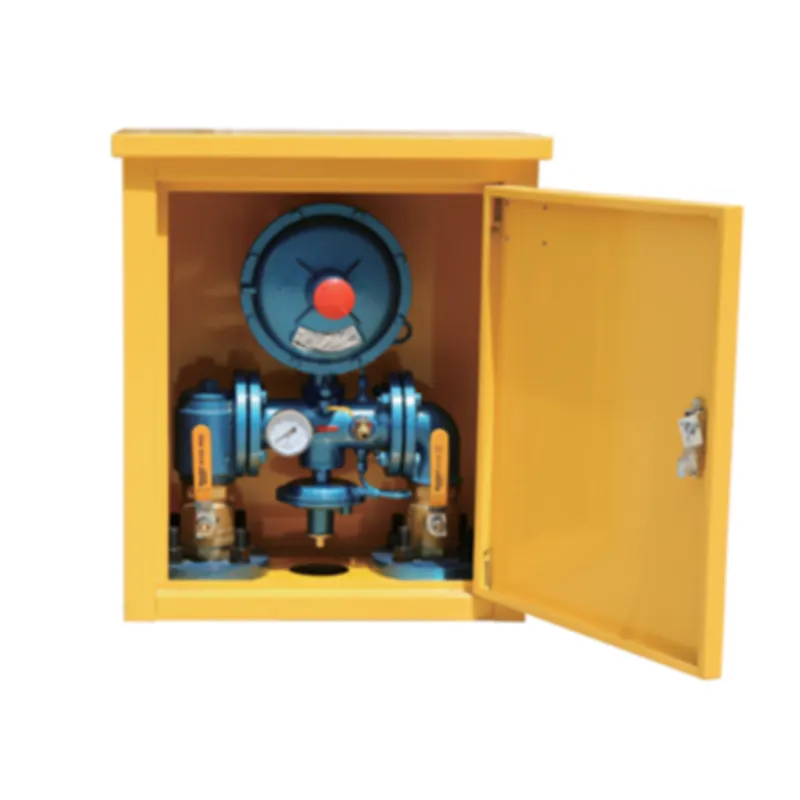
A gas pressure vessel is not just a container; it is a meticulously engineered solution designed to withstand high levels of internal pressure safely. The materials used in their construction are critical — typically, high-strength steel, aluminum, or composite materials are employed. These materials are chosen based on factors such as cost, durability, weight, and resistance to corrosion and high-temperature conditions.
In my years working as an engineer specializing in gas pressure systems, one key insight I've gathered is the importance of understanding the chemical properties of the gas stored. Different gases react distinctively with various materials; thus, incompatible pairing might lead to catastrophic failures. For instance, hydrogen embrittlement is a phenomenon that can occur if hydrogen gas is stored in certain types of steel pressure vessels, causing the material to crack and fail under stress.
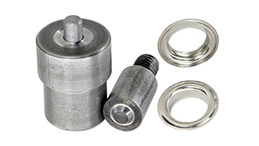
Moreover, expertise in pressure vessel design must adhere to international standards and certifications, such as the American Society of Mechanical Engineers (ASME) Boiler and Pressure Vessel Code. Compliance ensures that the design, manufacture, and inspection of these vessels meet rigorous safety and quality standards. Regular inspections and maintenance routines are indispensable practices that contribute to the longevity and operational safety of the vessels.
gas pressure vessel
When discussing trustworthiness and authority in the realm of gas pressure vessels, one cannot overlook the role of rigorous testing and validation processes. Non-destructive testing techniques, such as ultrasonic testing, radiographic inspection, and pressure testing, are employed to verify the structural integrity and performance of the vessels without causing damage. These testing procedures are vital to ensure that the vessels can safely contain the designated gases under high pressure over extended periods.
The evolving landscape of pressure vessel technology also demands a continuous update of skills and knowledge. Advanced simulation software and predictive maintenance technologies are now integral in designing and managing pressure vessels. Such advancements enhance the capability to predict potential issues before they manifest, thereby minimizing downtime and enhancing safety.
In conclusion, the manufacture and use of gas pressure vessels necessitate a blend of expertise, experience, and adherence to authoritative standards. With a steadfast commitment to safety and reliability, industries can benefit from the effective and secure utilization of these essential components. Whether you're a seasoned engineer or a company executive, understanding and applying the principles of pressure vessel engineering can significantly impact operational efficiency and safety.