Gas safety relief valves play an instrumental role in the landscape of industrial safety and operational efficiency. These components are not merely technical add-ons but are vital guardians of system integrity and human safety. Drawing from decades of expertise in industrial gas systems, this article delves into the nuanced world of gas safety relief valves, exploring their importance, functionality, and best practices for ensuring optimal performance and safety compliance.
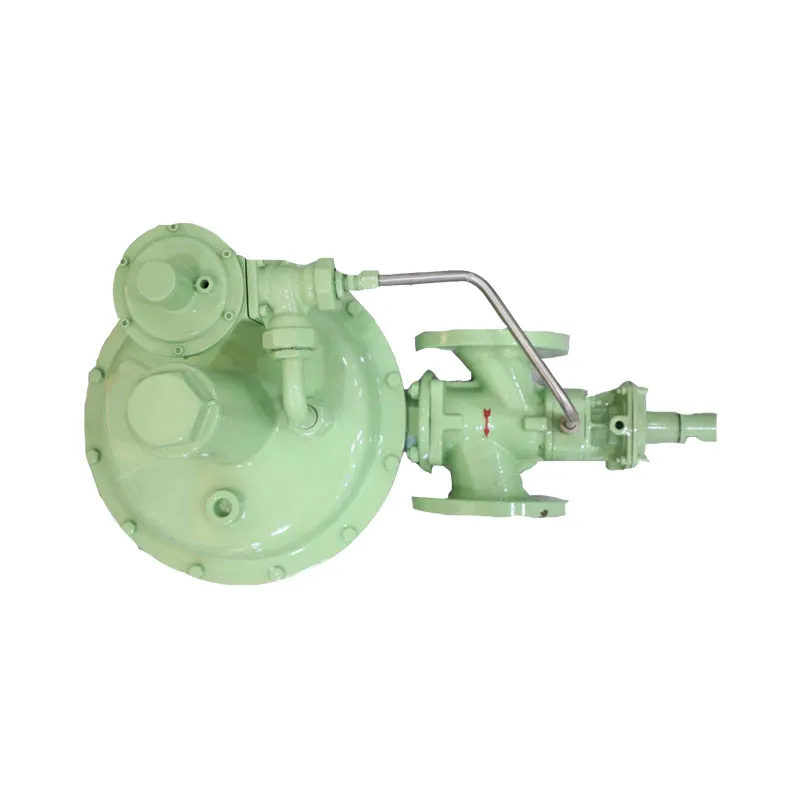
Understanding Gas Safety Relief Valves
Gas safety relief valves are designed to relieve excess pressure from a system, preventing potentially catastrophic failures. Their function is based on simple yet highly effective mechanical principles when the pressure within a system reaches a predetermined threshold, the valve opens to release excess gases. Once the pressure returns to safe levels, the valve automatically closes, maintaining the system's operational equilibrium.
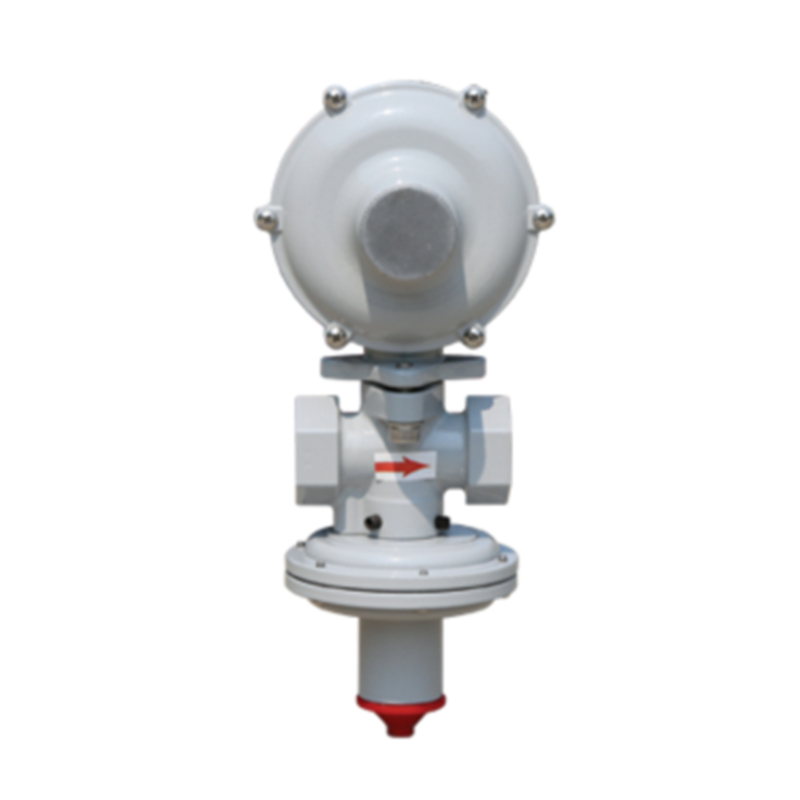
The critical importance of these valves cannot be overstated. They serve as the last line of defense against overpressure, which can lead to equipment damage, explosions, and even loss of life. It is this paramount role that underscores the need for proper selection, installation, and maintenance of gas safety relief valves.
Selecting the Right Gas Safety Relief Valve
The selection process for an appropriate relief valve is a meticulous undertaking that demands detailed knowledge of system requirements and environmental conditions. Engineers and safety experts collaborate to evaluate factors such as the type of gas being handled, temperature, pressure, flow rate, and the chemical properties of the process material. Utilizing this data, they can determine the most suitable valve type, material, and size.
Material selection is crucial, as valves must withstand aggressive chemicals and high temperatures, ensuring longevity and reliability. For instance, stainless steel valves offer excellent resistance to corrosive environments, making them ideal for use in the chemical processing industry.
Installation Best Practices
Even the best relief valve can fail if not installed correctly. The installation process should adhere to industry standards and regulatory requirements, ensuring that the valve functions as intended. Valves must be installed at precise angles to avoid false pressure readings and ensure unobstructed release paths for vented gases. It is also vital to ensure that vent lines are directed to safe locations to prevent hazards from escaping gases.
gas safety relief valve
Furthermore, integrating advanced monitoring systems provides real-time analytics and diagnostics, allowing for preemptive maintenance and immediate response to anomalies.
Maintenance and Compliance
Ongoing maintenance is imperative to ensure the long-term effectiveness of gas safety relief valves. Routine inspections should include valve calibration, checking for blockages or corrosion, and verifying the integrity of all seals and gaskets. Documenting these inspections not only helps maintain compliance with industry standards but also enhances the overall safety strategy.
Partnering with certified professionals for maintenance tasks ensures expertise-driven service that upholds the integrity of the safety system. Compliance with regulations such as API 520/521 and ASME Boiler and Pressure Vessel Code, Section VIII, is non-negotiable, as they provide guidelines that cover critical aspects of valve design, testing, and maintenance.
Innovations in Gas Safety Relief Valve Technology
Recent advancements have led to the development of smart valve technology. These next-generation valves incorporate sensors and connectivity features that allow for automatic adjustments based on real-time pressure readings. They can also communicate with central control systems to provide insights into system performance and predictive maintenance needs, significantly reducing the risk of failure.
Conclusion
Incorporating gas safety relief valves into an industrial setting is a complex yet vital task that demands expertise, stringent adherence to standards, and a commitment to safety. As innovations continue to evolve, these valves will become even more integral to comprehensive safety strategies. Businesses relying on gas systems must prioritize investing in quality valves, skilled installation, and regular maintenance, ensuring both operational efficiency and the utmost protection for their workforce and infrastructure.
By focusing on these areas, companies can not only comply with legal requirements but also cultivate a safer working environment, build trust with stakeholders, and enhance the longevity and reliability of their industrial operations.