In the world of industrial applications, heat exchangers serve as indispensable components in processes that require heat transfer between two or more fluids. Whether it's enhancing energy efficiency in power plants or optimizing air conditioning systems, the role of heat exchangers is pivotal. Drawing from years of experience in the field, this article delves into various aspects of heat exchangers—highlighting their significance, types, advantages, and key considerations for selecting the right model tailored to your specific needs.
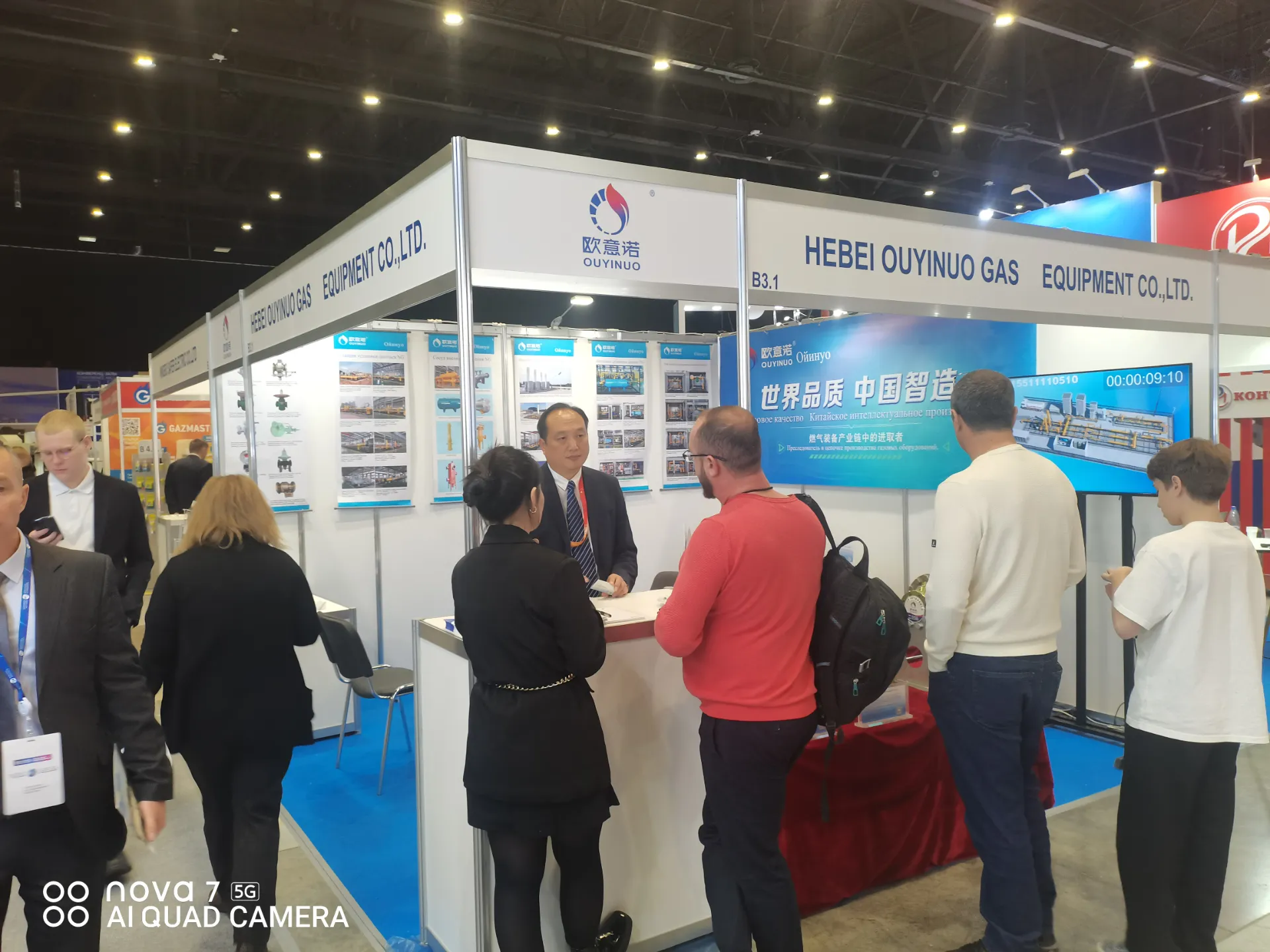
Heat exchangers are devices designed with precision engineering to facilitate the transfer of heat from one medium to another. This process does not necessitate the mixing of fluids,
which can be liquids, gases, or both. With energy efficiency becoming a global priority, industries are increasingly relying on advanced heat exchanger designs to optimize resource utilization and reduce operational costs.
A cornerstone of modern applications, heat exchangers come in various types, each serving distinct sectors and purposes. The most common types include shell-and-tube, plate, air-cooled, and regenerative heat exchangers. Shell-and-tube models, known for their robustness and versatility, are widely used in industries like oil refining and chemical processing. Meanwhile, plate heat exchangers, prized for their compact design and efficiency, are ideal for applications requiring high thermal performance, such as in HVAC systems and marine environments.
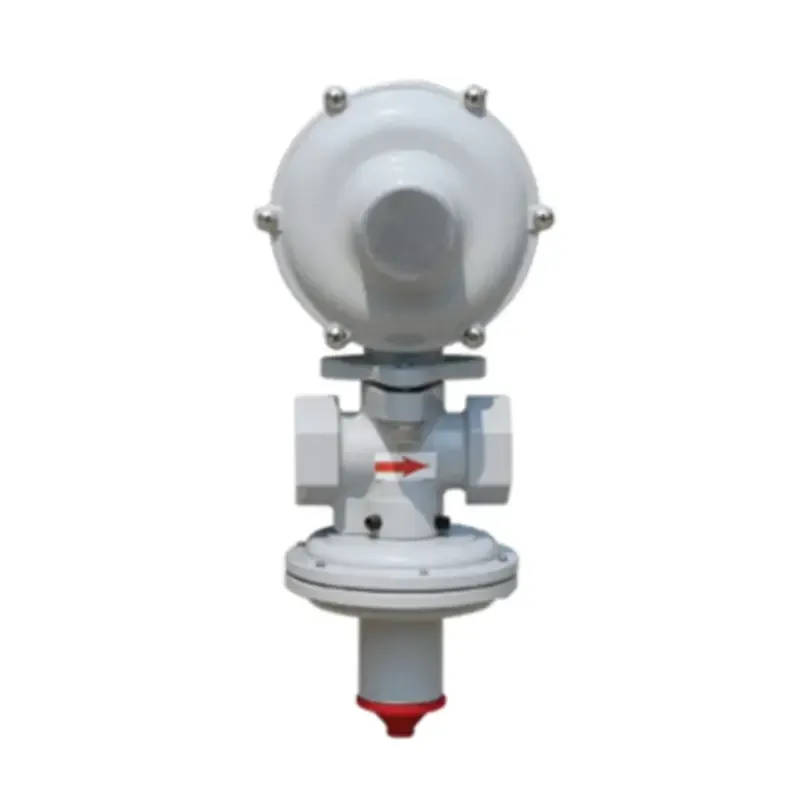
The choice of a heat exchanger hinges on multiple factors, including the type of fluids involved, temperature ranges, pressure limits, and maintenance requirements. One must consider the thermal performance of the design, which affects the operational efficiency and longevity of the system. Additionally, environmental conditions and potential fouling issues should be assessed to ensure long-term reliability and minimal downtime.
heat exchanger
Investing in a well-designed heat exchanger not only augments energy conservation but also enhances the safety and environmental compliance of industrial operations. Advanced materials and manufacturing processes have resulted in heat exchangers that not only perform effectively but also withstand challenging operational conditions, thereby ensuring longevity and reliability.
When selecting a heat exchanger, it is crucial to collaborate with manufacturers or suppliers who possess expertise and a proven track record in the field. The credibility of the supplier can significantly influence the performance outcomes and operational efficiency of the equipment. Ensuring that they adhere to international standards and have robust quality control measures can mitigate risks related to equipment failure or suboptimal performance.
Real-world experiences reveal that proactive maintenance and regular inspections play a vital role in preserving the efficiency and extending the lifespan of heat exchangers. Periodic cleaning, monitoring for signs of corrosion or wear, and replacing worn-out components are essential practices that contribute to the sustainable operation of heat exchangers.
In conclusion, heat exchangers represent a critical element in the realm of industrial operations, enabling efficient heat transfer that drives process optimization and energy savings. By understanding the types, functions, and key considerations associated with these devices, businesses can make informed decisions that align with their operational goals and sustainability commitments. Partnering with authoritative suppliers and prioritizing maintenance can further ensure that heat exchangers fulfill their role with excellence, thereby cementing their place as vital assets in industrial settings.