Pressure pipes are a critical component in various industries, playing an indispensable role in transporting fluids and gases across multiple applications. Understanding the depth of their functionality can empower industries to make informed decisions on the best type of piping systems to implement. Leveraging over a decade of hands-on experience in the field, I can confidently address the multifaceted nature of pressure pipes, dissecting their complex dynamics into understandable and applicable expertise.
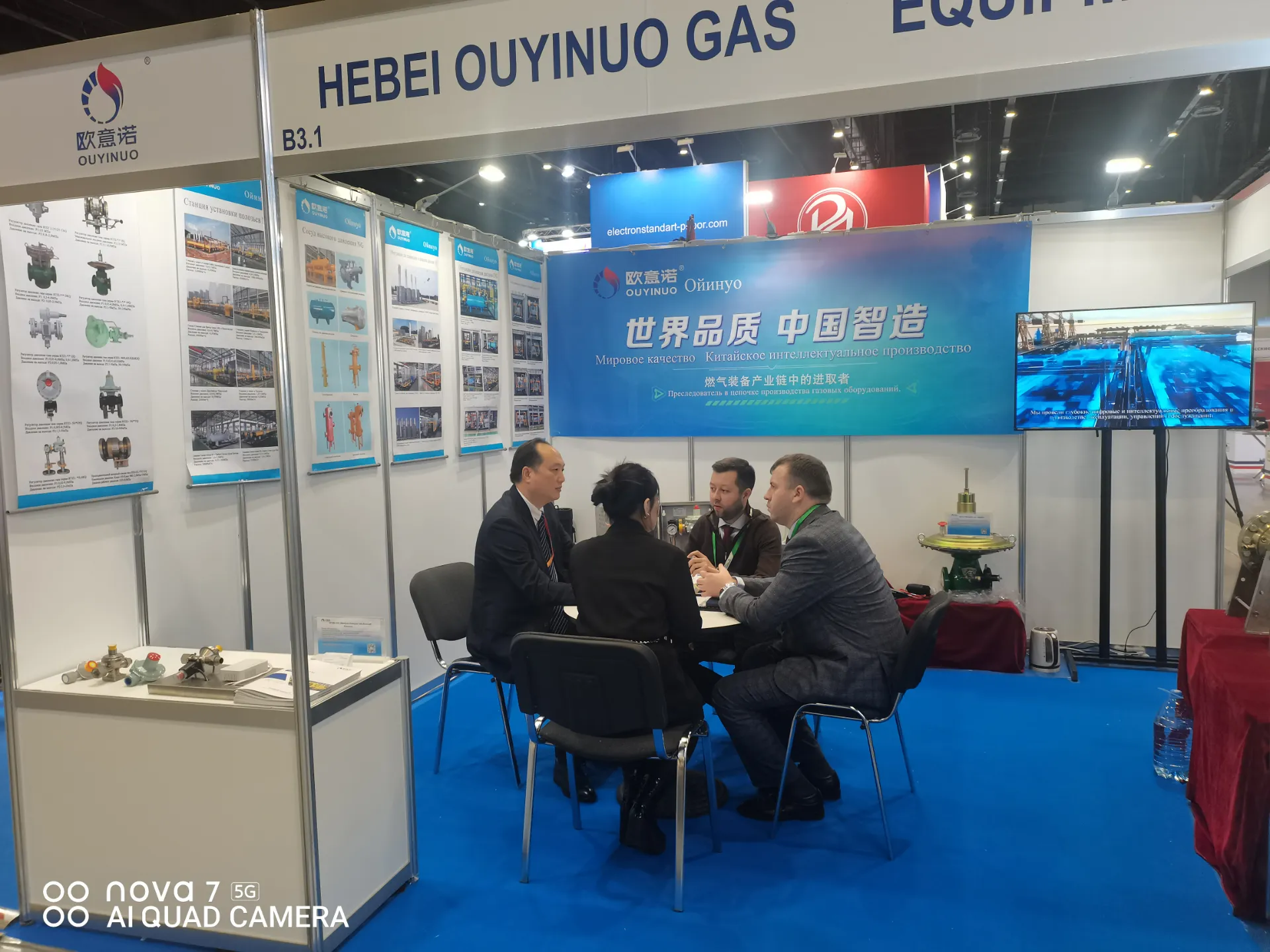
Pressure pipes are typically categorized by the material they are made from, such as steel, copper, polyvinyl chloride (PVC), or high-density polyethylene (HDPE). Each material offers unique benefits depending on the context of its application. For instance, steel pipes boast high strength and can withstand extreme pressures and temperatures, making them ideal for oil and gas industries. Conversely, PVC pipes are lightweight and corrosion-resistant, best suited for residential water systems or irrigation projects.
The expertise in choosing the right pressure pipe involves evaluating the maximum pressure it must handle. For example, an industrial application might require pipes that can endure pressures of thousands of psi, whereas residential systems might only need to withstand a few hundred psi. Advanced modeling software and testing allow professionals to simulate scenarios where pipes are subjected to maximum load capacities. This ensures reliability and safety, two paramount factors in system design.
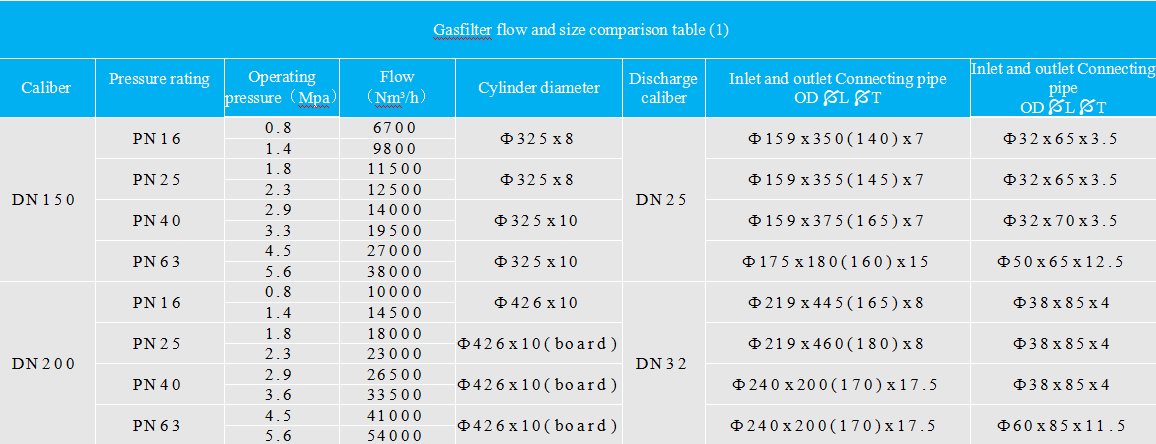
Let’s delve into a real-world experience. A recent project involving the replacement of an antiquated municipal water supply line demonstrated the significance of choosing the right pressure pipe material. Initially, older cast iron pipes were prevalent due to their durability and strength. However, issues like rust buildup and eventual breaks led to severe maintenance challenges. In replacing these with ductile iron pipes, we observed significant improvements in performance and longevity. Ductile iron not only retained the strength properties of cast iron but also provided added flexibility, crucial for accommodating ground movement and thermal expansion.
pressure pipe
Beyond product selection, there is an authoritative need for precise installation and maintenance techniques. Proper alignment during installation, attention to potential weak points, and utilization of technologically advanced sealing methods can prevent catastrophic failures. Empirical data indicates that most pressure pipe failures stem from poor installation practices or material mismatches, rather than the inherent quality of the pipes themselves.
Trustworthiness in the perspective of pressure pipes also involves adherence to standardizations and compliance protocols. Regulatory organizations, such as the American Society for Testing and Materials (ASTM) and the American Water Works Association (AWWA), set rigorous standards for pressure pipes to meet. These standards influence every aspect, from manufacturing to material stress tests, ensuring that pipes will perform as expected under various conditions.
In conclusion, pressure pipes stand as a foundational element across different sectors by ensuring complex systems function smoothly and safely. With an emphasis on experience-driven insights and a robust understanding of industry standards, stakeholders can make informed decisions. Knowledge in material science, pressure dynamics, and installation techniques culminates in the mastery necessary to select and implement pressure piping systems effectively. By prioritizing durability, reliability, and regulatory conformity, industries can achieve optimal performance and safety in their fluid transport operations, maintaining the integrity and functionality of their systems for the long term.