Pressure pipes are integral components in numerous industries, widely valued for their ability to transport fluids, gases, and even solids under high pressure conditions. Renowned for their resilience and adaptability, pressure pipes are engineered from a variety of materials, each chosen to meet specific requirements and environmental challenges. This article explores the critical features, materials, applications, and considerations for pressure pipes, offering insights based on industry expertise and practical experience.
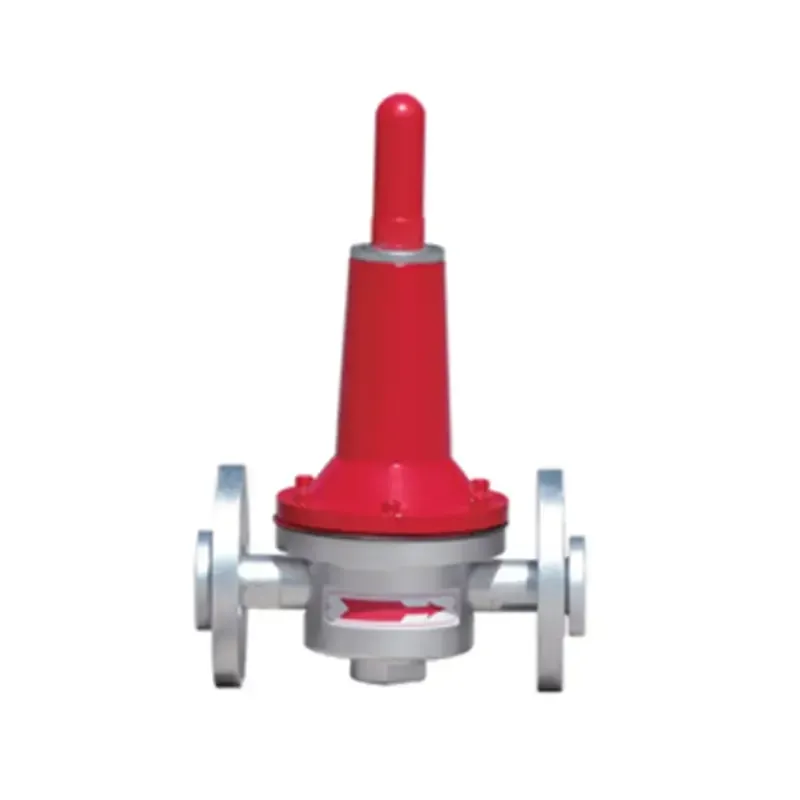
Understanding the functional aspects of pressure pipes begins with recognizing their primary role to efficiently convey substances under pressure levels that exceed standard atmospheric pressure. The failure of these systems can lead to catastrophic results, making it essential to select the right type of pipe for the application. The selection process demands a thorough understanding of factors such as the substance being transported, temperature conditions, and the pressure levels involved.
Among the most common materials used for pressure pipes are steel, copper, plastic (such as PVC and HDPE), and composite materials. Steel pipes are often preferred for their exceptional strength and durability, which makes them suitable for high-pressure applications in industries like oil and gas.
Their ability to withstand high temperatures and resist corrosion adds to their reliability.

Copper pressure pipes are revered in plumbing systems due to their excellent thermal conductivity and corrosion resistance. They are an excellent choice for water supply lines in residential and commercial construction. Meanwhile, plastic pressure pipes like PVC (polyvinyl chloride) and HDPE (high-density polyethylene) are increasingly popular in industries where weight reduction, corrosion resistance, and low cost are primary considerations. These pipes are frequently utilized in agricultural irrigation systems, water mains, and sewer systems.
Composite materials, which combine the properties of two or more distinct materials, offer tailored solutions for specific applications. These pipes exhibit enhanced resistance to corrosion and wear, making them ideal for transporting aggressive chemicals or operating in harsh environmental conditions.
pressure pipe
For engineers and decision-makers, choosing the right pressure pipe is heavily contingent on performance requirements and operating environments. It is critical to conduct a thorough analysis of factors such as pressure ratings, compatibility with the transported substance, temperature tolerance, and cost efficiency. Additionally, installation processes, maintenance requirements, and lifespan should also be factored into the decision-making process.
Real-world experiences reinforce the importance of regular maintenance and inspection of pressure pipes to prevent failure and to ensure operational integrity. Employing modern technologies such as ultrasonic testing, radiographic testing, and digital monitoring systems can help in early detection of issues such as leaks, corrosion, or mechanical failures, thereby enhancing safety and performance reliability.
Professional expertise suggests integrating risk management strategies into the workflow to identify possible threats to pressure system integrity, and to implement appropriate control measures. This proactive approach not only protects assets but also ensures compliance with industry standards and regulations, thereby fostering trust among stakeholders.
The authority of this information is rooted in decades of collective experience in the field, underscoring the importance of selecting quality materials and reliable manufacturers to avoid the pitfalls of inferior products. As technological advancements continue to reshape industries, staying informed about the latest developments in pressure pipe materials and technologies is imperative for maintaining competitive advantage and fulfilling safety and efficiency mandates.
In conclusion, pressure pipes are vital to the infrastructure of various industries. Their complex nature and critical function necessitate a comprehensive understanding of materials and applications, coupled with a proactive approach to maintenance and risk management to ensure longevity and performance. Whether in construction, plumbing, or industrial applications, the reliability of pressure pipes remains a cornerstone of modern engineering.