Pressure pipes are integral to various industries, offering efficient transportation of fluids and gases under pressure. Crafted from materials like steel, PVC, and composite materials, these robust pipes are designed to sustain substantial pressure levels, making them indispensable in sectors such as oil and gas, water treatment, and chemical processing. Ensuring the optimal application and performance of pressure pipes requires a deep understanding of their construction, function, and maintenance.
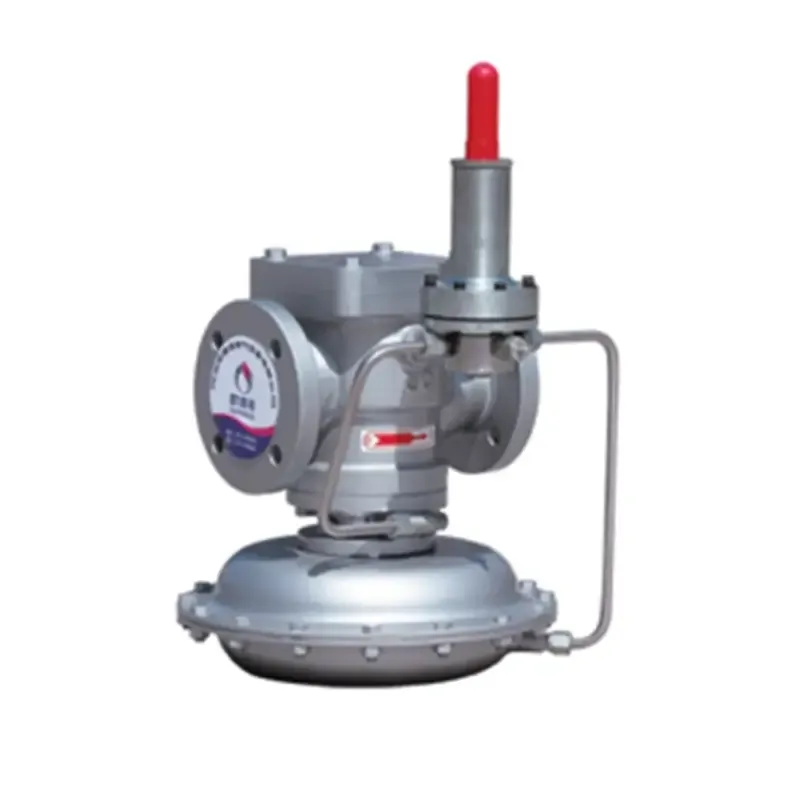
In industrial settings, pressure pipes are the backbone of infrastructure systems, particularly in the oil and gas industry. Their role in transporting crude oil, natural gas, and refined products across long distances is crucial. The selection of a suitable pressure pipe for these operations involves a meticulous analysis of factors including temperature, pressure ratings, and chemical compatibility. Utilizing advanced materials such as high-density polyethylene (HDPE) has significantly improved the performance and longevity of these pipes, offering resistance to corrosion and environmental stress cracking.
The water treatment industry also relies heavily on pressure pipes for the distribution of potable water and the treatment of wastewater. PVC pressure pipes are often preferred in this sector due to their lightweight nature, ease of installation, and cost-effectiveness. However, engineers must be vigilant about pressure ratings and potential for rupture, ensuring that pipes are compatible with the operational pressures they will encounter. The use of ductile iron pipes provides additional strength and resilience, particularly in systems facing higher pressure demands.
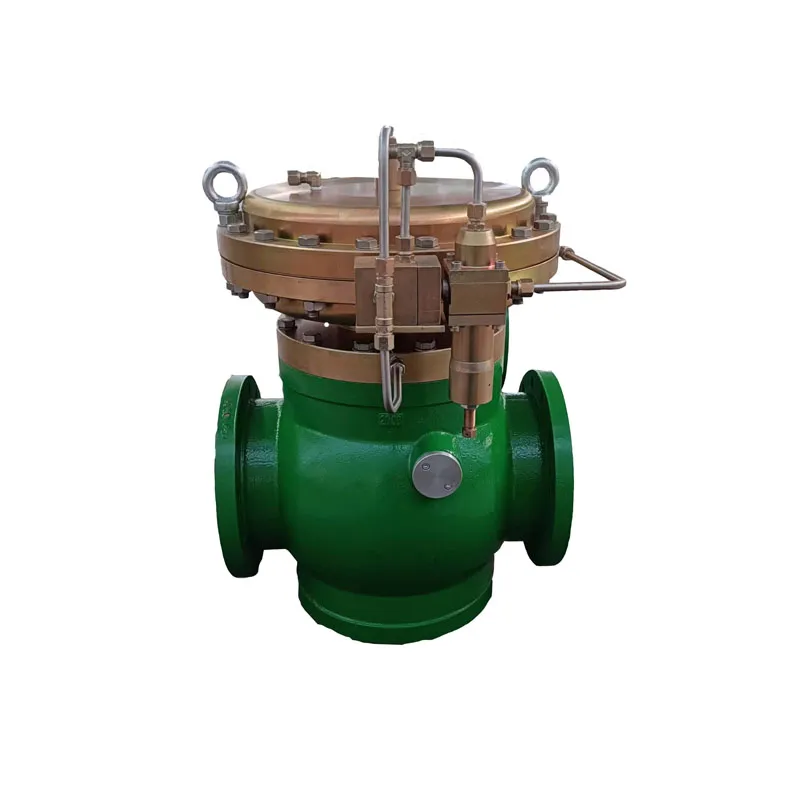
From a technical perspective, regular inspection and maintenance of pressure pipes are paramount to maintaining system integrity. Non-destructive testing methods such as ultrasonic testing and radiographic testing allow operators to detect potential flaws without compromising the pipe's functionality. Incorporating smart sensor technologies can further enhance monitoring capabilities, providing real-time data on pressure fluctuations and stress levels within the pipeline.
This proactive approach to maintenance not only prevents catastrophic failures but also extends the pipeline's service life.
pressure pipe
Regulatory compliance forms a cornerstone of pressure pipe utilization, with industry standards dictating manufacturing, installation, and operational guidelines. The American Society of Mechanical Engineers (ASME) and similar international bodies set forth stringent codes to ensure safety and reliability. Adhering to these standards not only ensures safe operations but also reinforces customer trust in the products being used. Manufacturers and operators are therefore encouraged to remain vigilant about updates to these regulations, fostering a culture of safety and compliance.
Sustainability considerations are also shaping the future of pressure pipe development. The shift towards environmentally friendly materials and manufacturing processes is becoming more pronounced. Companies are increasingly investing in research to develop biodegradable materials that do not compromise on performance or durability. Reducing carbon footprints and promoting recycling initiatives are additional steps being taken to align with global environmental goals.
In conclusion, pressure pipes are a critical component across multiple industries, providing essential infrastructure for the safe transport of fluids and gases under pressure. Their success hinges on a blend of robust design, strict adherence to industry standards, and innovative maintenance practices. By focusing on these aspects alongside sustainability efforts, companies can ensure both operational excellence and environmental responsibility. The future of pressure pipes lies in leveraging technological advancements and adopting sustainable practices that meet the evolving demands of modern industries.