Pressure reducing regulators are pivotal components across numerous industries, ensuring optimal performance, safety, and efficiency in systems where pressure control is critical. As an experienced engineer with decades of expertise, I've seen firsthand the transformative impact these regulators can have on operations, so choosing the right one is paramount.
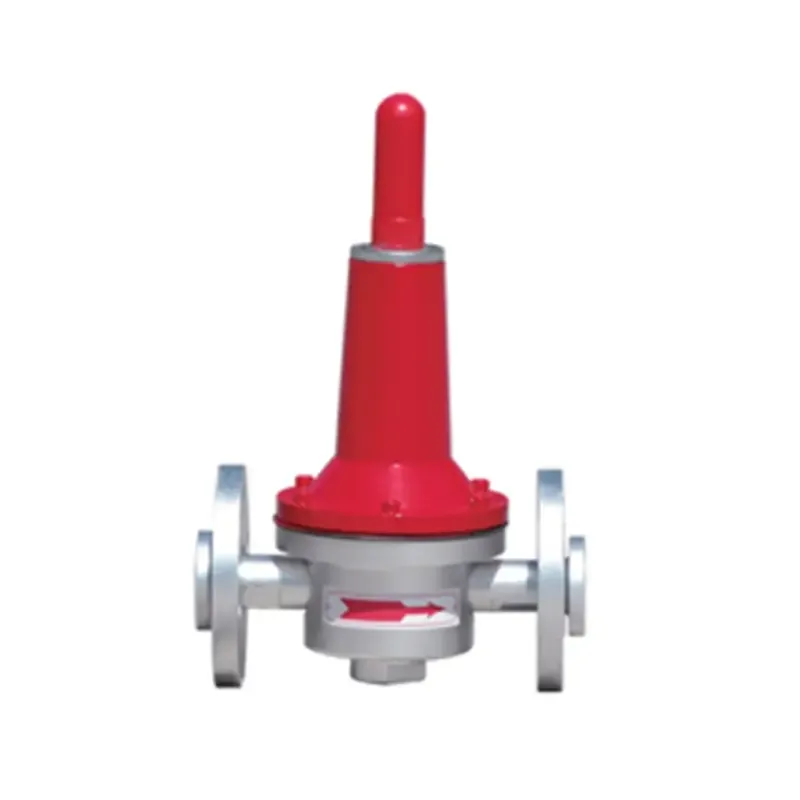
Selecting a suitable pressure reducing regulator involves understanding the intricacies of its mechanism, material composition, and application-specific suitability. At the core, these devices are designed to maintain a consistent downstream pressure from a variable upstream source, a function that is indispensable for protecting sensitive instrumentation and equipment.
Calculations of flow requirements must be precise. Misjudging the required regulator capacity can lead to operational inefficiencies or catastrophic failures. Therefore, a thorough evaluation of flow rate, pressure range, and media type is essential. From personal experience, including variables such as temperature fluctuations and potential corrosive properties of the fluid in your calculations can safeguard performance and longevity.
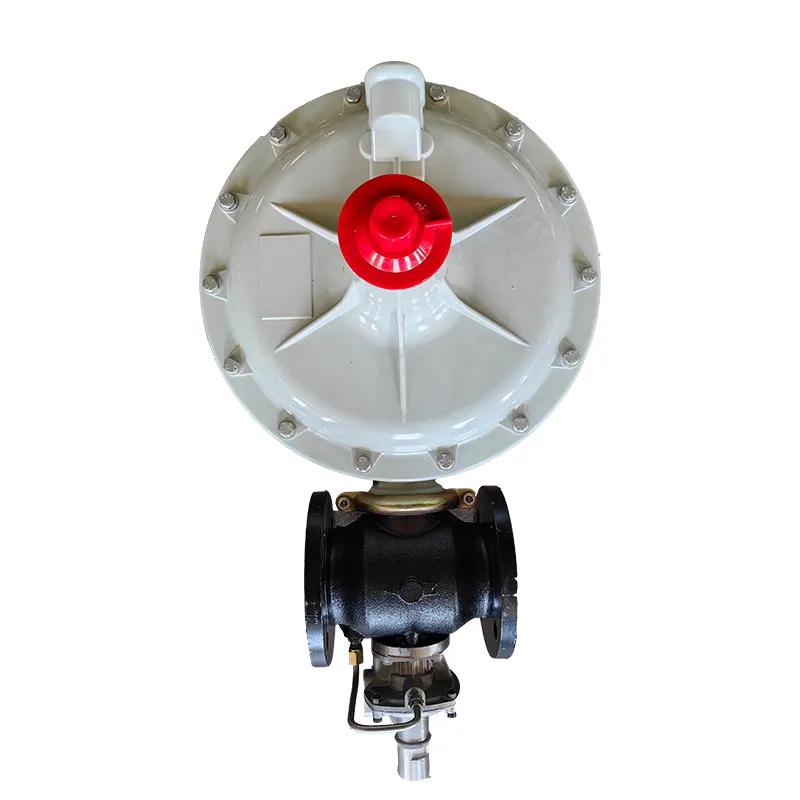
When exploring materials, stainless steel and brass are frequently encountered options, each with distinct advantages. Stainless steel, known for its corrosion resistance, is ideal for harsh environments, while brass offers an economical and sufficient solution for less demanding applications. In high-stakes scenarios, opting for materials that ensure durability under all operational conditions is a testament to sound engineering judgment.
Precision in design engineering must not be overlooked. A well-designed regulator will incorporate advanced features such as sensitive diaphragm assemblies and self-relieving configurations, ensuring minimal pressure deviations. Utilizing technologies like pilot-operated mechanisms can further enhance accuracy, providing finer control even at lower pressure differentials.
pressure reducing regulators
From a safety perspective, integrating pressure reducing regulators into your systems acts as a first line of defense against overpressure scenarios.
A key experience from my professional journey involves embedding these regulators in petrochemical systems. In such volatile environments, reliability is non-negotiable. A failure in pressure management could escalate into catastrophic safety incidents, affecting lives and environments.
Accreditation and compliance with industry standards like ANSI, ASME, and API are critical marks of a regulator’s quality and credibility. As has been evident from managing large-scale engineering projects, adherence to these standards is not merely bureaucratic; it is a validation of the product’s reliability and the manufacturer's commitment to safety and performance excellence.
The trust one places in a brand is equally crucial. Collaboration with reputed manufacturers, who are transparent about their testing processes and product certifications, fortifies trust. Moreover, access to technical support and after-sales service is indispensable. Responsiveness to client needs and swift problem resolution are indicative of a brand's trustworthiness and commitment.
In conclusion, the choice of a pressure reducing regulator is not just a technical decision but a strategic one that can profoundly influence operational efficacy and safety. Delving into the specifics of application requirements, material suitability, design intricacies, and compliance ensures that your choice aligns with both current needs and future anticipations. Employ a comprehensive approach, and your investment in pressure reducing regulators will yield not just functional continuity but robust safety and quality assurance.