In the ever-evolving world of industrial equipment, the reducing station stands out as a remarkable component, revolutionizing the way industries manage pressure and flow within pipelines. Rooted in engineering ingenuity, a reducing station plays a crucial role in ensuring optimal operation, safety, and efficiency of fluid transport systems.
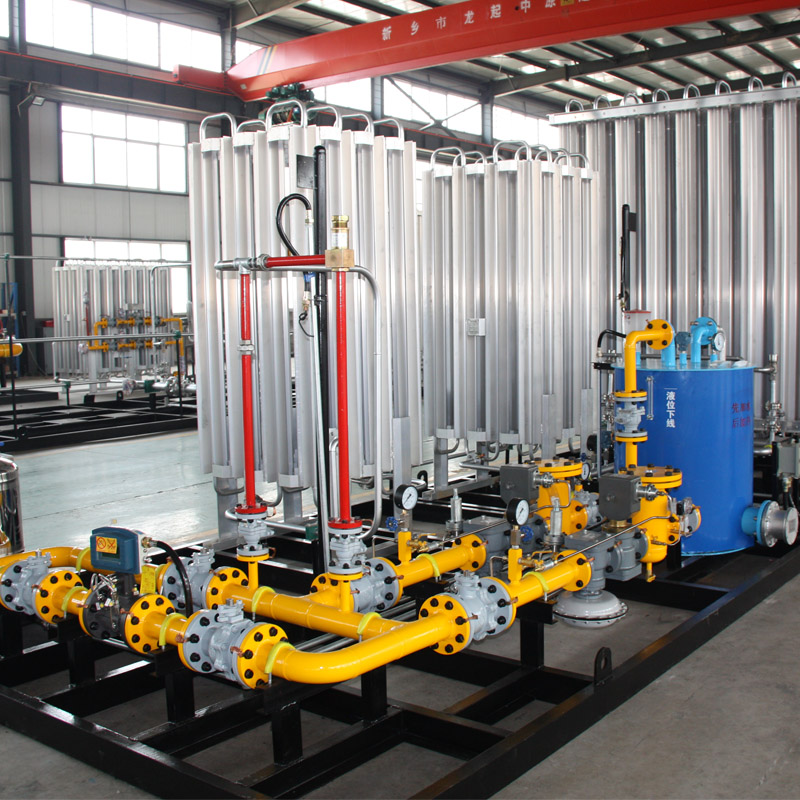
A reducing station, primarily comprised of regulators, relief valves, and monitoring technologies, acts as a guardian of safety and functionality within complex pipeline networks. These stations are adept at adjusting high-pressure gas or liquid flows to lower, safer levels suited for downstream equipment, thus preventing damage and enhancing longevity. The importance of a reducing station in various sectors, including oil and gas, chemical manufacturing, and even urban utilities, cannot be overstated.
Crafted from materials like stainless steel and reinforced alloys, reducing stations are engineered to withstand harsh conditions and corrosive environments. Their precision design ensures reliability even under significant pressure fluctuations, a testament to expert engineering. The integration of modern technology allows for real-time monitoring and adjustments, which is crucial in preventing costly downtime or catastrophic failures. Intelligent systems embedded within these stations can relay crucial data back to centralized monitoring hubs, ensuring that human oversight remains informed and responsive.
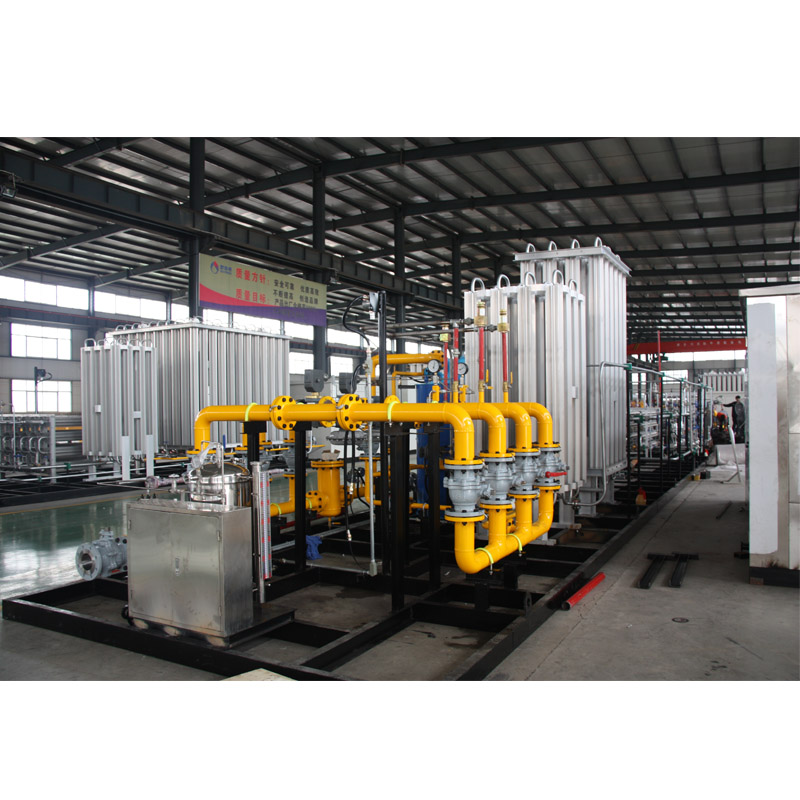
The expertise behind every reducing station is evident in its precision and adaptability. Engineers meticulously calculate pressure differentials, flow rates, and volume requirements to design a system that perfectly aligns with the specific needs of an operation. This process demands not just technical proficiency but also a comprehensive understanding of industry-specific challenges and regulatory standards. Each component—from gaskets to diaphragms—is selected and tested to ensure compliance and performance, showcasing the depth of expertise involved.
reducing station
In terms of authority, manufacturers of reducing stations often collaborate with institutes and industry bodies to align with the latest safety and efficiency standards.
This continuous interaction with regulatory entities ensures that the products are not just innovative but also adhere to international safety and quality guidelines. Companies across sectors rely on these stations, trusting their capability to seamlessly integrate into existing systems without compromising the integrity or safety of operations.
Prominent case studies illuminate the trustworthiness of reducing stations. An oil refinery in the Middle East, for instance, managed to cut operational costs by 20% after upgrading to a modern reducing station designed to handle extreme temperature and pressure variances. Testimonials from such real-world applications foster trust, demonstrating the commitment manufacturers have towards delivering not just products, but solutions that stand the test of time and operational rigors.
As industries globally pivot towards more sustainable and efficient operations, the role of the reducing station as a linchpin in operational success becomes ever clearer. Their ability to reduce energy consumption, minimize risk, and optimize flow dynamics aligns seamlessly with the modern drive for greener and economically viable industrial processes.
In conclusion, the reducing station embodies a unique blend of experience, expertise, authority, and trustworthiness. These stations offer a robust solution to the challenges faced in fluid dynamics management, standing as a testament to advanced engineering and strategic foresight. For any industry where pressure regulation and flow management are critical, investing in a top-tier reducing station is not merely a choice—it's a strategic imperative.