In the complex world of fluid dynamics, the regulating valve holds a pivotal position for its ability to control flow and pressure within piping systems. Far more than just a mechanical component, a regulating valve demands a detailed understanding for optimal selection and integration, which can significantly impact the efficiency and safety of industrial operations.
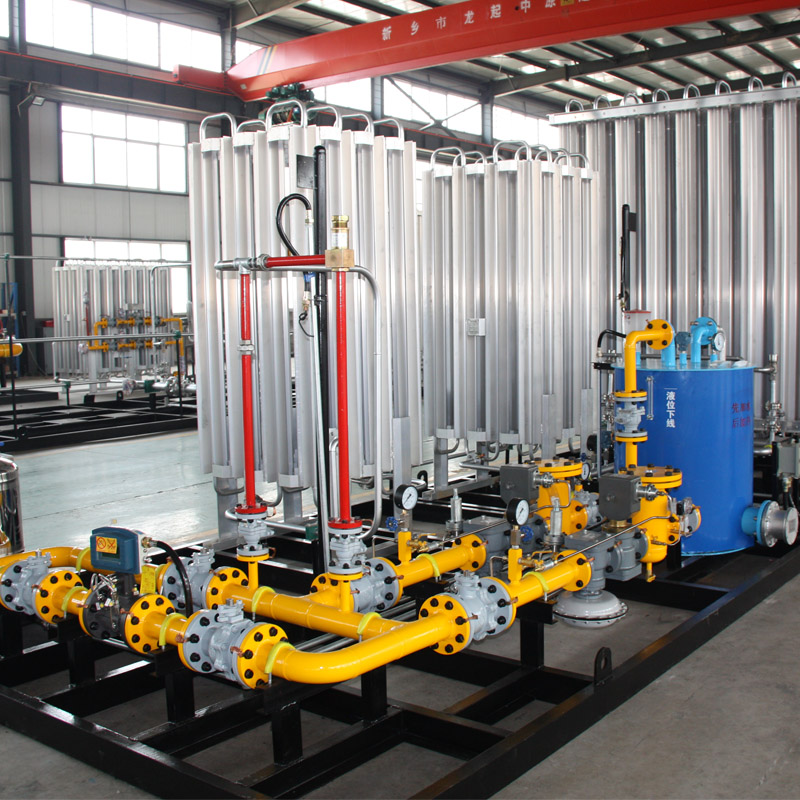
Regulating valves are used across various industries, from oil and gas to chemical manufacturing, where precise control of fluid flow is essential. The importance of these valves cannot be overstated as they ensure the desired flow is maintained, system performance is optimized, and safety is upheld. This demands an expert approach to understanding their types, functionalities, and applications.
One of the common types of regulating valves is the globe valve, renowned for its excellent throttling capabilities. Characterized by their spherical body, these valves are perfect for applications that require precise control, such as in chemical feed systems. Its design reduces the risk of leakage and allows for easy maintenance, making it a favorite in many industries.
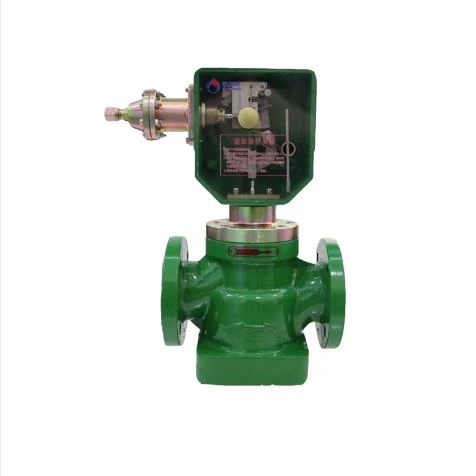
Butterfly valves, on the other hand, are known for their compact design and ease of operation. Ideal for large-diameter pipes, they are often used in water management systems and HVAC applications. Their simplistic design ensures minimal pressure drop and offers a cost-effective solution for large-scale fluid regulation.
In comparison, ball valves provide an excellent sealing with their quarter-turn operation. While traditionally used in shut-off applications, innovations in design have seen them adapted for regulating purposes, particularly where a tight seal and minimal leakage are paramount.
A noteworthy mention is the control valve, which is essential in process control systems. Often automated and integrated with control systems, they can respond to signals from sensors and regulators to modulate the flow instantaneously, ensuring system stability and efficiency. Their usage in complex industries such as oil refineries underscores their indispensable role in modern engineering.
regulating valve
When selecting a regulating valve, understanding the Environmental, Mechanical, Operational, and Maintenance (EMOM) factors is crucial. Environment determines material compatibility; mechanical considerations involve pressure and temperature limits; operational factors focus on flow capacity and response time; and maintenance includes ease of service and longevity. By evaluating these parameters, engineers can align valve choice with system needs, ensuring operational excellence.
It's imperative to consider the potential for advanced technology integration. Smart valves, equipped with sensors and IoT capabilities, allow for real-time monitoring and predictive maintenance. By leveraging data analytics, organizations can not only enhance performance but also extend the lifecycle of their valves, reducing operational costs and downtime.
When implementing a regulating valve solution, trustworthiness is established through rigorous testing and compliance with international standards such as ANSI, API, and ISO. These certifications attest to a valve's reliability under specified conditions, providing peace of mind to engineers and plant operators. Working with manufacturers who adhere to these standards ensures the valves' validity and durability in critical operations.
Furthermore, expertise in operational training for staff handling these valves ensures they can identify potential issues early and understand the nuances of adjusting and maintaining these components. This comprehensive approach reinforces trust and authority in the system's integrity.
In conclusion, the choice and implementation of a regulating valve require a balanced blend of expertise, experience, and an authoritative approach. By prioritizing these factors, companies can ensure that their systems are not only efficient and safe but also adaptable to the evolving demands of modern industry applications.