Safety relief valves are critical components in a multitude of industrial applications, ensuring the safe and efficient operation of various systems. These devices serve as the last line of defense against excessive pressure build-up, preventing potential disasters in environments ranging from chemical plants to power generation facilities.
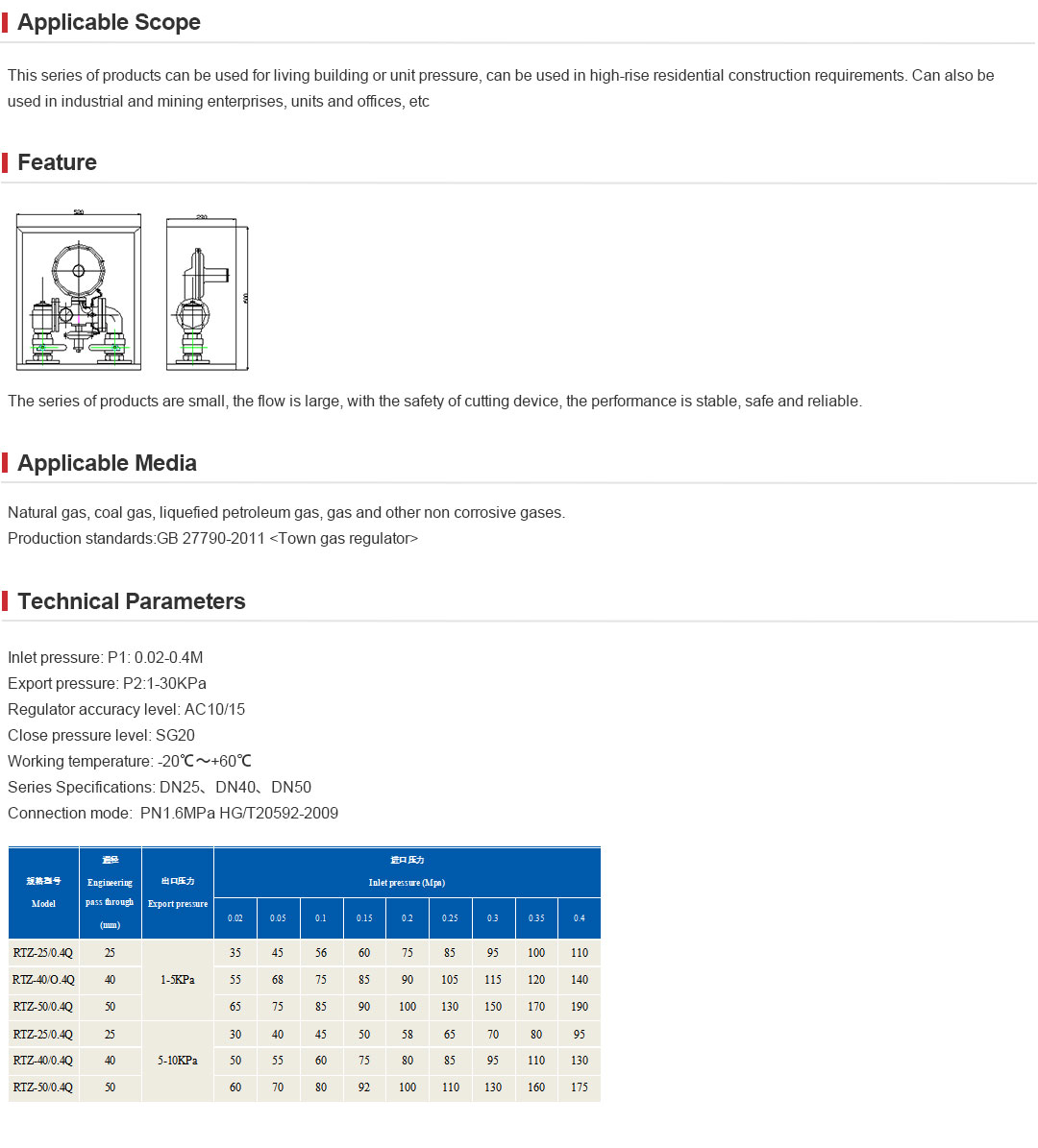
Experience plays a crucial role in understanding the nuances of safety relief valves. Many companies that have operated with safety relief valves for decades often highlight their reliability when properly maintained. Manufacturers frequently design these valves to automatically release pressure once it exceeds a specified limit, thereby protecting equipment from potential damage or catastrophic failure. For instance, industries handling volatile substances rely heavily on the proper functioning of these valves to maintain safety standards and regulatory compliance.
Expertise in the realm of safety relief valves extends beyond basic functioning. Professionals in the field must possess a comprehensive understanding of the various types of valves, such as direct spring-loaded, pilot-operated, and bellows type, each offering unique advantages for different applications. Direct spring-loaded valves, for example, are commonly used in systems where overpressure occurs frequently but not continuously. Conversely, pilot-operated valves provide precise control in systems that require high capacity relief. Expertise also entails knowledge of material compatibility, as the valve materials must withstand the media being processed to prevent corrosion or degradation over time.
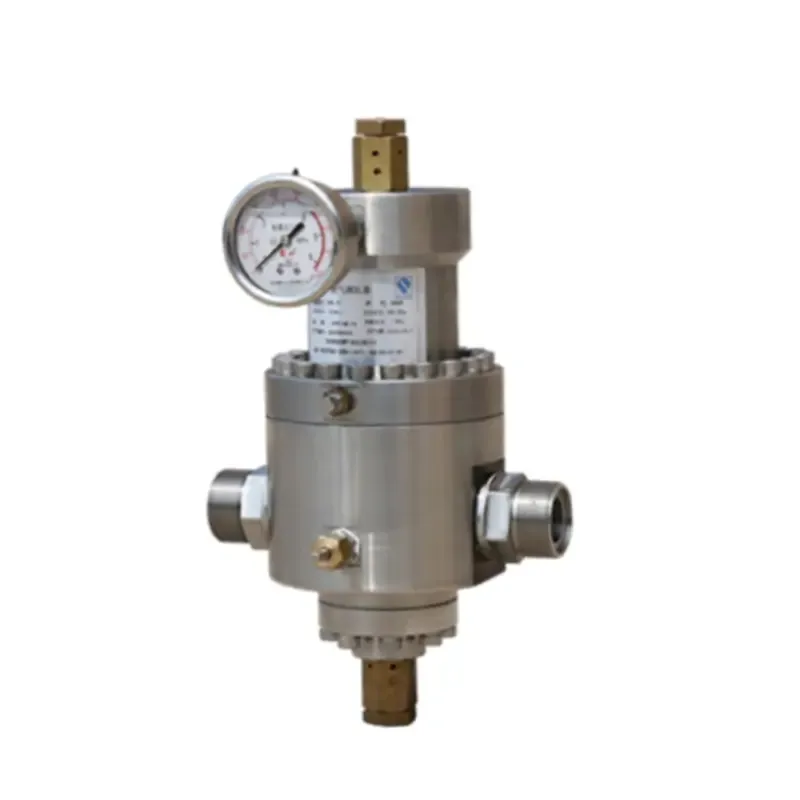
Authoritativeness in the sphere of safety relief valves is often attributed to adherence to recognized standards and certifications. In the United States, the American Society of Mechanical Engineers (ASME) provides a comprehensive set of guidelines and codes for the design and testing of these valves. Products that meet ASME standards are widely regarded as reliable and efficient. Similarly, international standards like those from the International Organization for Standardization (ISO) ensure that relief valves used in global markets maintain consistency in safety and performance.
safety relief valve
Trustworthiness is inherently linked to the reliability and quality assurance provided by manufacturers and suppliers of safety relief valves. Companies with a long track record in the industry often offer robust warranties and service agreements, affirming their commitment to delivering quality products.
Customers frequently rely on trusted brands, as the consequences of valve failure can be dire. Moreover, trustworthy companies often provide comprehensive after-sales support, including maintenance services and technical training for operators, ensuring the continued effectiveness of their products.
Choosing the right safety relief valve requires careful consideration of operational conditions, including the pressure and temperature range, the type of media being handled, and the installation environment. For instance, industries using corrosive media such as caustic chemicals must utilize valves made from resistant materials like stainless steel or specialized alloys to prevent premature failure. In contrast, high-temperature applications may necessitate valves made from materials capable of retaining structural integrity under extreme heat.
Furthermore, the integration of digital monitoring systems with traditional safety relief valves has emerged as a modern advancement, adding an extra layer of security. These systems provide real-time data on valve performance, enabling predictive maintenance and reducing the likelihood of unexpected failures. This integration exemplifies the fusion of traditional engineering with cutting-edge technology to enhance safety and operational efficiency.
In summary, safety relief valves are indispensable for maintaining safety and operational integrity in various industries. Experience, expertise, authoritativeness, and trustworthiness are paramount in ensuring that these critical components perform their intended function reliably and effectively. By staying abreast of industry standards, leveraging technological advancements, and prioritizing quality assurance, companies can significantly mitigate risks associated with pressure-related incidents.