In the intricate world of industrial equipment, a safety valve stands as a quintessential component ensuring not only the efficiency but also the security of various systems. These valves are engineered to automatically release substances from a boiler, pressure vessel, or other systems when the pressure or temperature exceeds preset limits. The significance of safety valves cannot be overstated, particularly in industries where high-pressure operations are a daily occurrence.
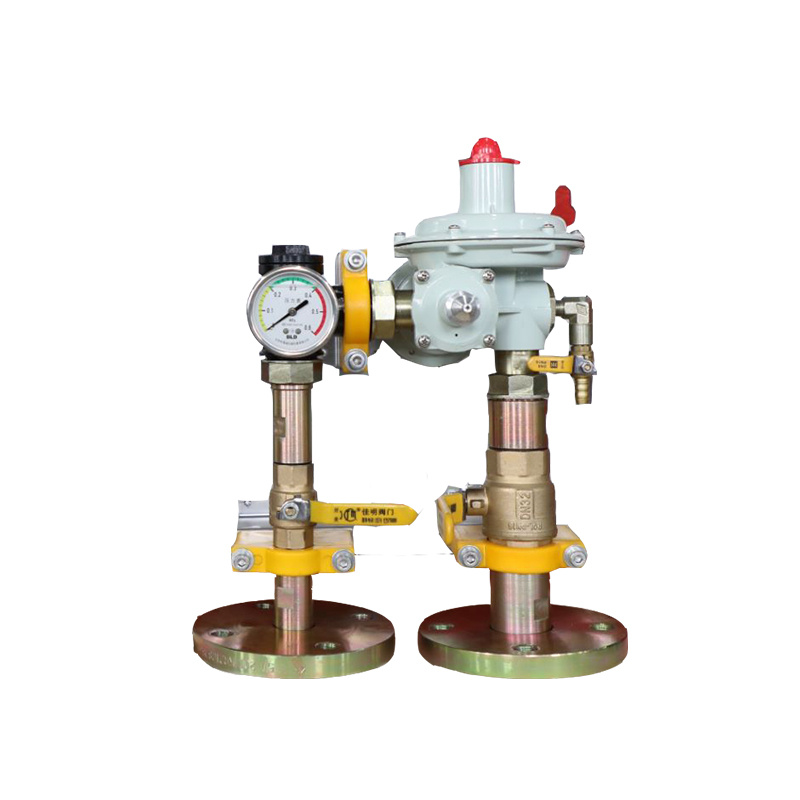
From the perspective of an industrial expert, experiencing the reliability of a high-quality safety valve can make a substantial difference in operational safety. In various industries, such as oil & gas, pharmaceuticals, power generation, and chemical processing, pressure control is paramount. An effective safety valve not only protects machinery and equipment from damage due to overpressure but also ensures the protection of human resources, which is irreplaceable.
A professional approach towards selecting the right safety valve should involve an in-depth understanding of your system's operational parameters. For instance, it's crucial to consider the set pressure, temperature ratings, and the capacity of the valve, ensuring compatibility with system requirements. These elements are fundamental for a safety valve to function correctly under specified conditions.
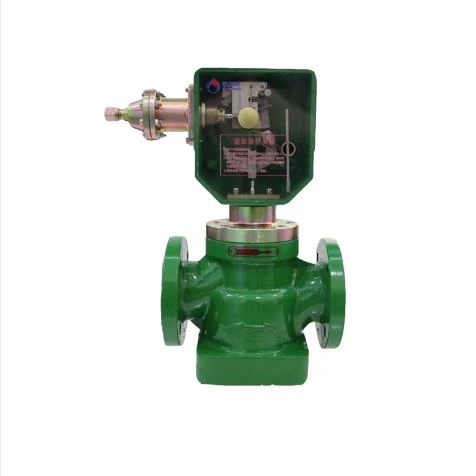
In terms of expertise, the development and manufacturing of safety valves are guided by stringent industry standards such as ASME (American Society of Mechanical Engineers) or API (American Petroleum Institute). Adhering to these standards signifies a manufacturer's commitment to quality and reliability. Professionals in the field must stay abreast with the latest technological advancements and regulatory requirements to maintain an edge in safety valve technology. Essential features include the incorporation of materials that resist corrosion and wear, prolonged lifecycle, and adaptability to various operational settings.
safety valve
Authoritativeness in safety valve deployment can be seen in the attention to detail in installation and maintenance practices. Certified technicians and engineers should perform installation following manufacturer guidelines and industry best practices. Regular inspections, testing, and maintenance are pivotal in upholding the safety features and operational readiness of these valves. Moreover, these practices contribute to an organization's compliance with safety regulations and codes, thereby mitigating risks associated with valve failure.
Building trustworthiness around safety valve use involves transparency and education. Organizations should educate their staff about the operational principles of safety valves and the specific roles they play in safeguarding system integrity. Providing comprehensive documentation that includes operating manuals, installation guides, and maintenance schedules contributes to a clear understanding and trust in the equipment being used.
Safety valves are not merely mechanical devices; they are the guardians of industrial stability. Adopting a diligent approach to selecting, installing, and maintaining these valves reflects an organization's commitment to safety and operational excellence. By focusing on real-world experience, and integrating expert knowledge with authoritative practices and sustained trust, industries can optimize the use of safety valves, ensuring a safe and efficient operation across various applications.
For more detailed insights and queries related to safety valve selection and maintenance, consulting with seasoned experts and manufacturers can provide tailored solutions aligning with specific operational needs and objectives.