Safety valves are critical components in a wide range of industries, serving as the last line of defense against equipment failure, excessive pressure build-ups, and potentially catastrophic outcomes. Their primary function is to protect systems by releasing pressure automatically when it reaches a certain set point. Given their vital role, choosing the right safety valve is not just a matter of regulatory compliance, but it is also a strategic decision that directly impacts operational safety, efficiency, and cost-effectiveness.
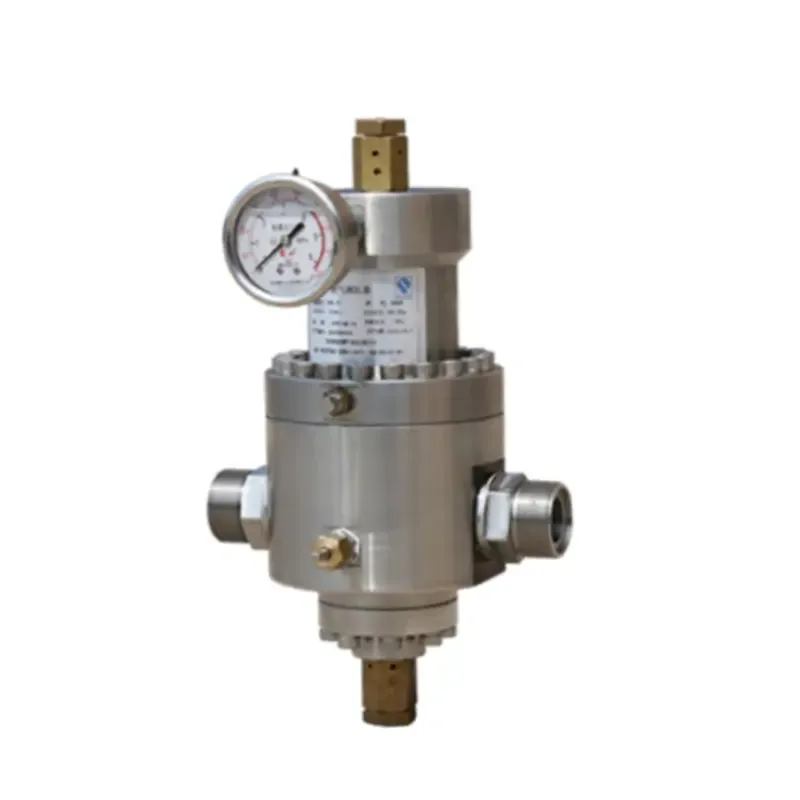
In industries such as oil and gas, chemical processing, and power generation, safety valves operate under demanding conditions. Therefore, understanding their specifications, applications, and regulatory requirements is paramount. One of the key assessments involves selecting the appropriate type and size of the valve to match the particular application it will serve. Factors such as pressure ratings, temperature limits, and materials compatibility must be meticulously evaluated to ensure long-term reliability and performance.
Safety valves are not one-size-fits-all devices. Among the various types, pressure relief valves, pressure safety valves, and pilot-operated safety valves serve different applications and operational environments. For instance, pressure relief valves might be more suited for liquid environments, while pressure safety valves are typically employed in steam applications. The decision to choose one over the other should be based on a thorough understanding of the system dynamics and specific operational challenges.
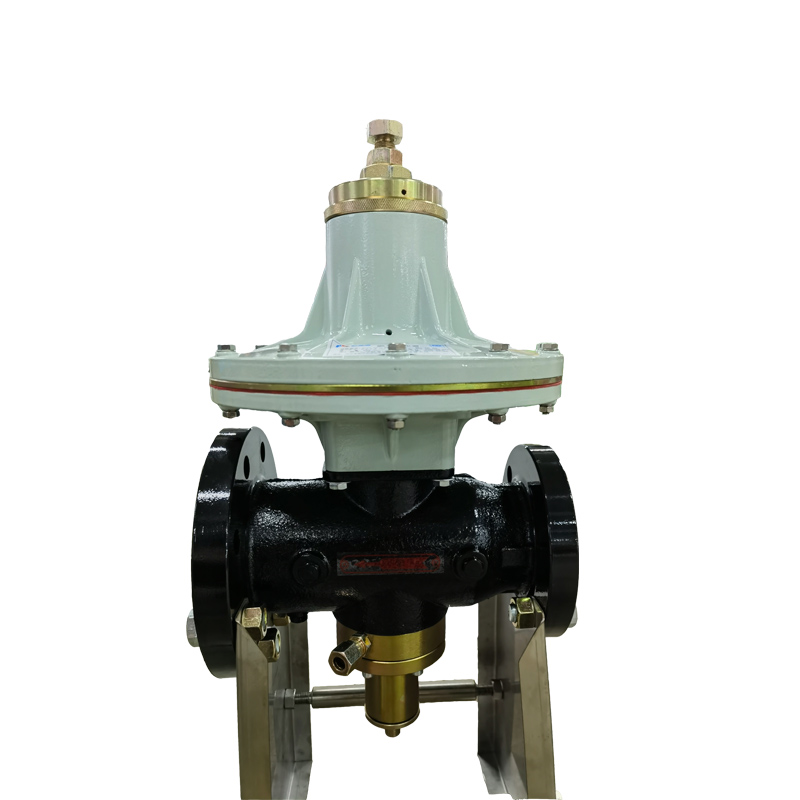
Another critical element in the selection and operation of safety valves is compliance with industry standards and regulations. Bodies such as the American Society of Mechanical Engineers (ASME) have established rigorous testing and certification processes to ensure these valves can perform under expected service conditions. Adhering to these standards is not merely a matter of maintaining industry best practices; it is often a legal obligation that ensures safety and operational efficacy.
The intricacies of safety valve maintenance are also an essential consideration. Regular inspection and maintenance schedules must be established to detect signs of wear, corrosion, or material degradation. Neglecting these aspects can lead to valve failure, undermining the safety of the entire system. Using advanced diagnostic tools and techniques, such as ultrasonic testing and thermography, allows for predictive maintenance, reducing the risk of unexpected failures and associated downtimes.
safety valve
Advancements in technology have introduced smart safety valves, equipped with sensors and connectivity features that allow for real-time monitoring of pressure levels and valve performance. This advancement enhances predictive maintenance strategies and facilitates more informed decision-making. However, integrating these advanced systems requires an investment in both technology and training, ensuring personnel are equipped to manage the new capabilities effectively.
When selecting a safety valve, it is also crucial to consider the reputation and expertise of the manufacturer. Partnering with reputable suppliers who have a track record of quality and reliability can provide additional assurance. In a fast-evolving industry landscape, staying updated with the latest safety standards and technological advancements is essential, ensuring equipment is not only compliant but also optimized for peak performance.
Furthermore, employing a safety-first culture within the organization can significantly influence the effectiveness of safety valve implementation. Training personnel on emergency protocols, ensuring clear procedural guidelines, and fostering an environment where safety is prioritized over shortcuts contribute markedly to operational safety.
Cost considerations are often at the forefront of decision-making processes; however, it is vital to take a holistic approach, evaluating the total cost of ownership rather than just the initial investment. Poorly chosen or inadequately maintained safety valves could lead to operational disruptions, presenting expenses vastly outweighing the initial purchase cost.
In conclusion, the role of safety valves extends beyond simple mechanical components; they are integral to safety and operational efficiency across various sectors. By focusing on their selection, compliance, maintenance, and the integration of new technologies, industries can optimize the reliability and performance of their systems, safeguarding both personnel and infrastructure. Adopting best practices from reputable sources and investing in advanced solutions not only satisfies legal and regulatory obligations but also enhances organizational trust and reputation. Emphasizing experience, expertise, authoritativeness, and trustworthiness in these processes ensures the sustainable and effective management of these critical safety devices.