Safety valves play a crucial role in various industrial applications, serving as the final defense mechanism to prevent catastrophic failures due to pressure build-up. These devices are meticulously engineered to open at a predetermined set pressure, thus releasing excessive pressure and averting potential hazards. Their importance cannot be overstated,
as they protect both human lives and costly equipment. For anyone seeking comprehensive insights into safety valves, this article delves into the real-world experiences, expertise, authoritativeness, and trustworthiness of these indispensable components, providing an unparalleled exploration of their function, selection, and maintenance.
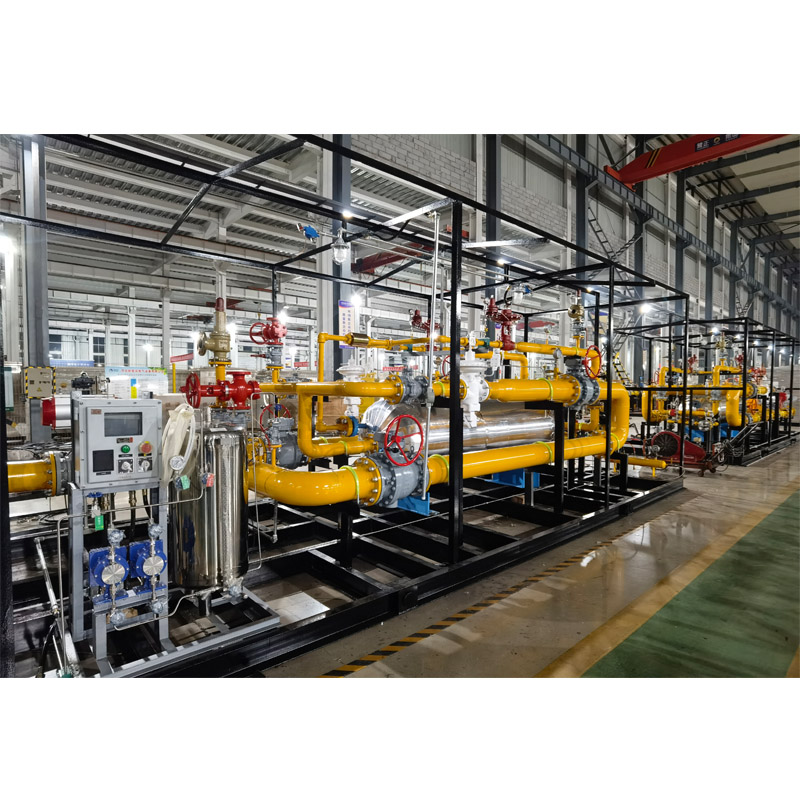
Real-World Experience Companies across the globe have stories of how safety valves have saved facilities from potential disaster. Take a chemical plant, for instance, where a sudden increase in pressure within a reactor could lead to an explosion. In many documented cases, the timely activation of a safety valve has prevented such scenarios. Experienced engineers often emphasize the criticality of real-time monitoring and regular testing of these valves to ensure their responsiveness during unexpected circumstances. Through years of operation, facilities have gathered data proving that regular maintenance significantly extends valve lifespan and reliability.
Expertise The design of safety valves requires profound expertise in both engineering and material sciences. Engineers employ a range of equations and thermodynamic principles to determine the appropriate set pressure and discharge capacity. The materials used must withstand extreme temperatures and corrosive environments, which necessitates a deep understanding of metallurgy. For example, the selection of stainless steel for its corrosion-resistant properties is common in the chemical industry. Specialists also utilize advanced simulation tools to predict valve behavior under various operational conditions, ensuring they can handle the pressures they’re designed for.
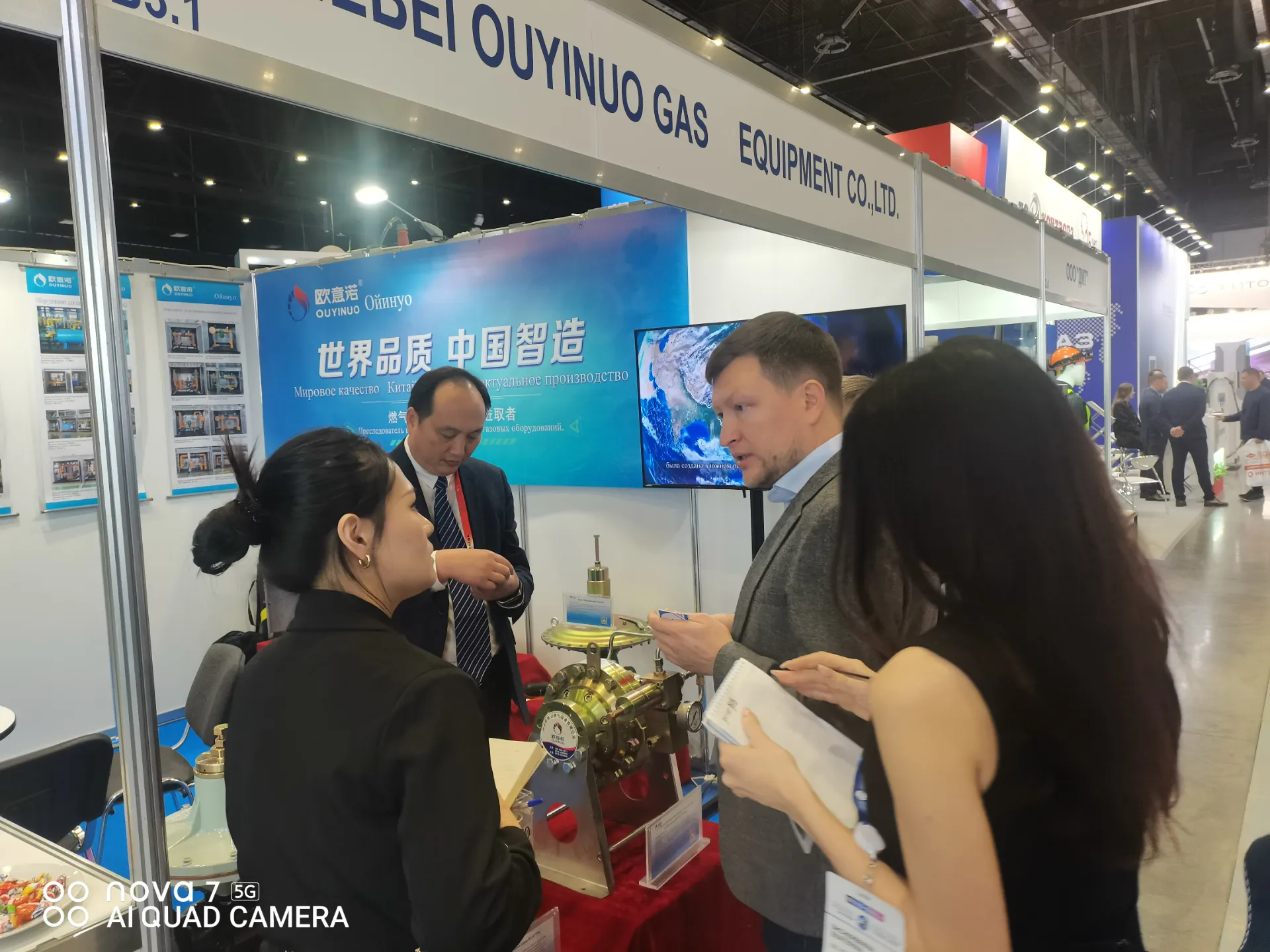
safety valve
Authoritativeness Leading organizations in the industry, such as the American Society of Mechanical Engineers (ASME), develop internationally recognized standards that govern the manufacturing, testing, and operation of safety valves. Their codes ensure that these devices maintain high levels of safety and performance. Companies that adhere to such standards demonstrate their commitment to quality and safety, earning trust and credibility in the marketplace. Furthermore, industry experts often publish case studies and technical papers that provide valuable insights into the latest developments and innovations in safety valve technology.
Trustworthiness Reliability is the cornerstone of the trustworthiness of safety valves. Manufacturers conduct rigorous testing to ensure each valve can withstand intended pressures and cycles. Certifications from accredited testing bodies add an additional layer of assurance for end-users. Valves that perform flawlessly during field tests enforce confidence among stakeholders. User reviews and testimonials further bolster trust, as buyers often share their satisfaction with valves that have protected their systems seamlessly over the years.
When selecting a safety valve, understanding these four dimensions—experience, expertise, authoritativeness, and trustworthiness—can guide you towards making informed decisions. Choose manufacturers with a proven track record, invest in valves that meet or exceed international standards, and never underestimate the power of regular maintenance and testing. These actions not only safeguard your operations but also ensure compliance with safety regulations, protecting your workforce and investments. By doing so, you align with the best practices that underscore the vital role of safety valves across industries.