The realm of natural gas pressure regulators is not often at the forefront of discussions in energy management, yet their significance cannot be overstated. These devices quietly ensure the smooth and efficient delivery of natural gas to countless homes and industries worldwide. When delving into the complexities of natural gas pressure regulators, it's crucial to approach the topic with a focus on genuine experience, professional expertise, authority, and trustworthiness.
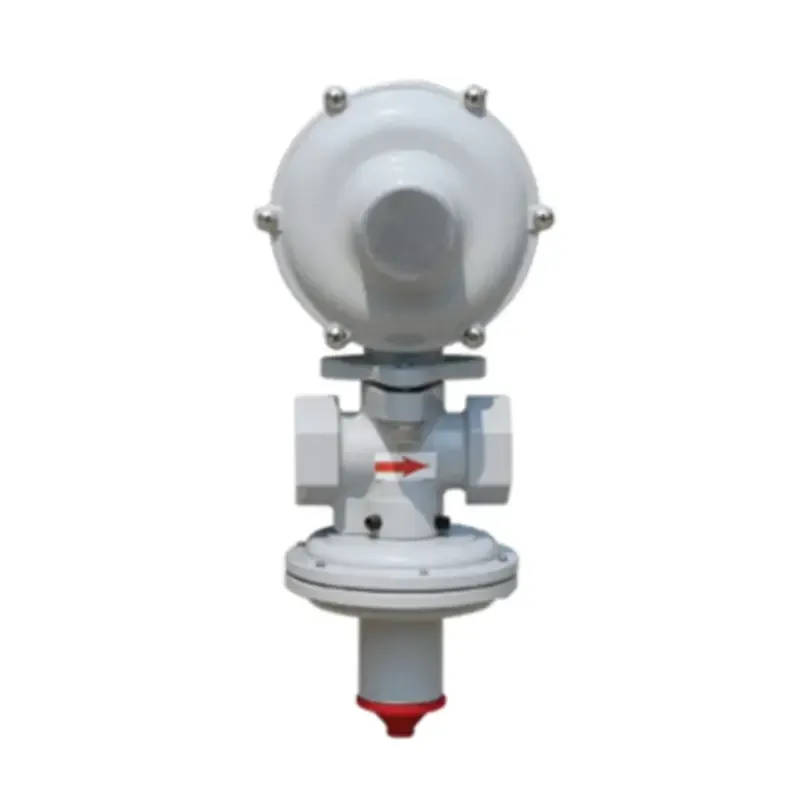
For anyone involved in the field,
understanding the technology and function of natural gas pressure regulators is foundational. These devices are engineered to maintain downstream pressure at a desired level, ensuring that fluctuations in supply do not impact the consumer. A significant part of their usefulness comes from their ability to adapt to varying consumption rates. Whether the demand spikes or decreases, these regulators keep the pressure consistent, safeguarding appliances and industrial processes from potential damage due to overpressure or vacuum conditions.
From a professional standpoint, installing, maintaining, and troubleshooting these regulators requires a high degree of expertise. Technicians and engineers working with natural gas systems must be thoroughly trained and knowledgeable about the specific types of regulators available, including direct-operated, pilot-operated, and spring-loaded regulators. Each kind brings its own set of advantages and challenges, making the selection process highly dependent on the specific application and environmental conditions.
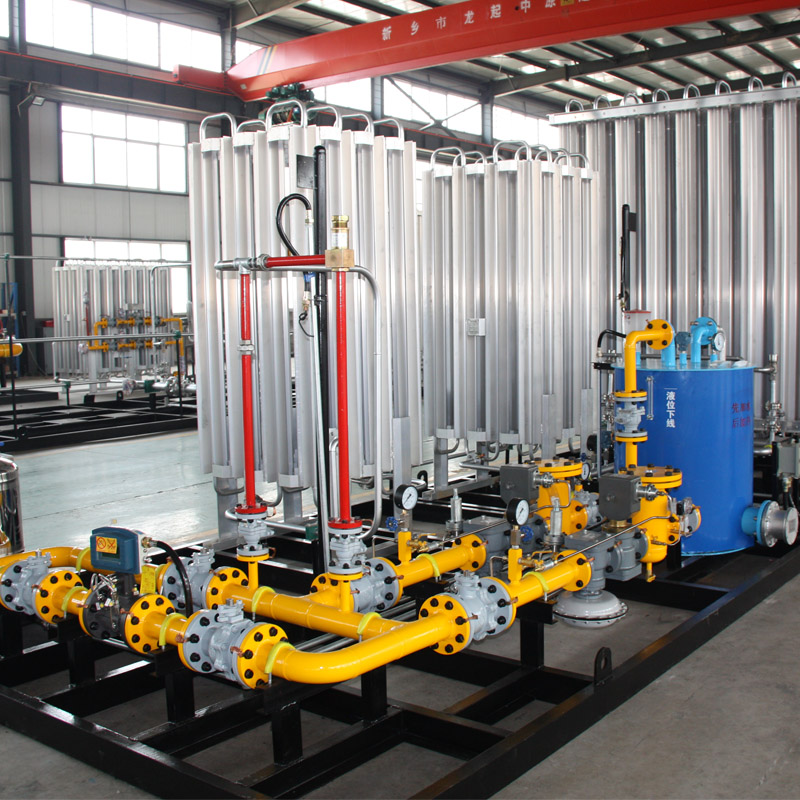
Direct feedback from field engineers often highlights the importance of choosing the right materials, particularly when the regulators are exposed to harsh environmental conditions. Corrosion-resistant components are critical in ensuring longevity and reducing maintenance costs over time. Additionally, the integration of advanced monitoring systems within these regulators can provide real-time data, enabling operators to make informed decisions quickly and effectively, thus preventing both downtime and potential safety hazards.
Natural gas pressure regulator
One of the most authoritative voices in the industry is that of standards organizations and regulatory bodies. Compliance with regulations such as ASME/ANSI standards, European Norm (EN), and other local directives is vital for both safety and operational efficiency. These regulations ensure that all equipment can withstand certain pressure levels and are subject to rigorous testing during the manufacturing process.
Trust in the equipment is paramount, typically earned through proven track records and certifications from recognized bodies. Manufacturers often emphasize their commitment to quality and safety by obtaining ISO certifications and investing in extensive research and development. By doing so, they align themselves with the core principles of safety and reliability that consumers and industries demand.
In terms of user experience, investing in a high-quality natural gas pressure regulator delivers both peace of mind and economic benefits. An efficient regulator reduces the likelihood of gas leaks and related incidents, which could otherwise lead to hazardous situations and significant financial loss. Moreover, regulators that perform optimally ensure energy is used efficiently, which can translate into cost savings on utility bills across sectors.
To conclude, while natural gas pressure regulators may function quietly in the background, their impact on safety, efficiency, and cost-effectiveness in energy consumption is profound. Professionals engaging in the purchase, management, or maintenance of these essential devices must commit to ongoing education and adherence to best practices and standards. Through this commitment, they ensure that the benefits of natural gas as a resource are fully realized, securely, and sustainably.