Gas heat exchangers play a critical role in various industries, ranging from energy production to manufacturing processes, playing an indispensable role in thermal regulation and process optimization. Their primary function is to transfer heat between two or more fluids, especially gases, without having them mixed. Leveraging high-performance materials and advanced thermodynamic principles, these devices not only enhance machinery efficiency but also contribute to energy conservation and environmental sustainability.
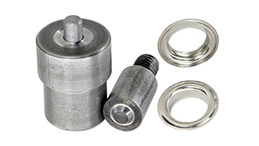
When selecting a gas heat exchanger, several factors demand careful consideration. First, understanding the nature of the gas, including its chemical composition and temperature range, is crucial. For instance, corrosive gases may necessitate heat exchangers made from materials such as stainless steel or even advanced alloys to withstand degradation. Furthermore, the temperature differential between the incoming and outgoing gas flows must be managed to maximize heat transfer efficiency.
The choice of heat exchanger design is instrumental in its performance. Common designs include shell-and-tube, plate, and air-cooled heat exchangers, each offering distinct advantages. Shell-and-tube designs are renowned for their robustness and ability to handle high pressures and volumes, making them suitable for industrial applications. Plate heat exchangers, with their compact structure and high surface area, are ideal for applications requiring quick heat transfer in limited spaces. Air-cooled exchangers, on the other hand, are crucial in scenarios where water is scarce or expensive.
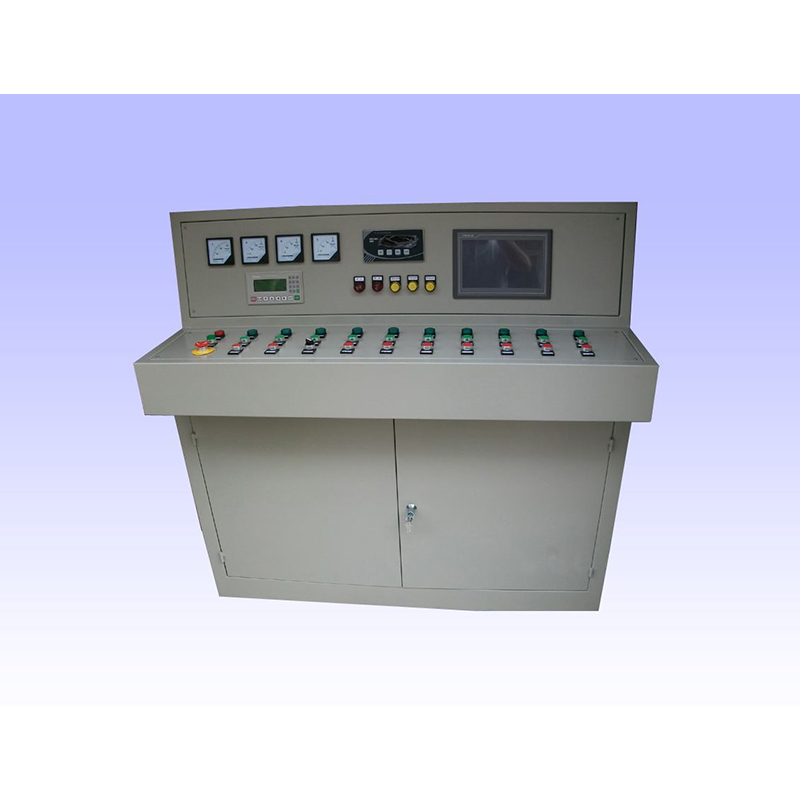
The installation and maintenance of gas heat exchangers directly correlate with their longevity and efficiency. Proper installation necessitates precision alignment and secured fittings to prevent gas leaks—a task that demands professional expertise. Regular maintenance ensures debris does not accumulate within the exchanger, which could impede gas flow and reduce efficiency. Advanced diagnostic tools and condition monitoring systems can now preemptively identify potential failures, allowing for proactive maintenance and avoiding costly downtimes.
Innovation in gas heat exchangers is progressively enhancing their capabilities. Recent advancements in material science, such as the development of nanomaterials and heat-resistant composites, are pushing the envelope in terms of thermal conductivity and durability. Moreover, integrating smart technology into these exchangers allows for real-time monitoring and data analytics, optimizing performance and energy use effectively.
Gas heat exchanger
Another key aspect to consider is the ubiquitous pursuit of environmental compliance and efficiency. As global awareness of carbon emissions and regulatory pressures heightens, gas heat exchangers are pivotal in reducing the carbon footprint of industrial processes. By maximizing thermal efficiency, these systems lower energy consumption, thus reducing the demand on fossil fuels and minimizing greenhouse gas emissions.
Expertise in the field indicates that personalized approaches to designing gas heat exchangers significantly enhance their performance. Collaborating with specialized manufacturers that understand specific industry requirements can lead to custom solutions that are more effective than off-the-shelf options. This partnership often results in heat exchangers that not only meet performance specifications but also align with organizational goals for sustainability and cost-effectiveness.
Building trustworthiness and authority in the market requires transparency in operation and communication. Companies providing gas heat exchangers should offer detailed documentation and reporting on the performance metrics and efficiencies of their products. Customer testimonials and case studies further bolster confidence, illustrating proven successes across similar applications.
Finally, the role of gas heat exchangers in emerging technologies and renewable energy cannot be overstated. As industries gradually shift towards green energy solutions, the relevance of efficient thermal management is amplified. Heat exchangers are integral in the operation of systems like geothermal plants and biogas facilities, where they help in transforming raw energy sources into viable outputs with minimal environmental impact.
In conclusion, gas heat exchangers remain a cornerstone of industrial and environmental efficiency, bolstered by continual advancements in technology and materials. By emphasizing experience, expertise, authoritativeness, and trustworthiness, stakeholders can ensure optimal selection, utilization, and innovation in heat exchanger applications, thereby contributing positively to both economic and environmental outcomes.