Electric valves, a cornerstone of numerous industries, offer a pivotal role in automating and controlling fluid flow in various applications. The expertise in selecting and maintaining these devices is not only crucial for optimal performance but also for enhancing operational efficiency. Understanding the intricacies of electric valves can bridge the gap between theoretical knowledge and practical application, underscoring their importance in engineering and industrial processes.
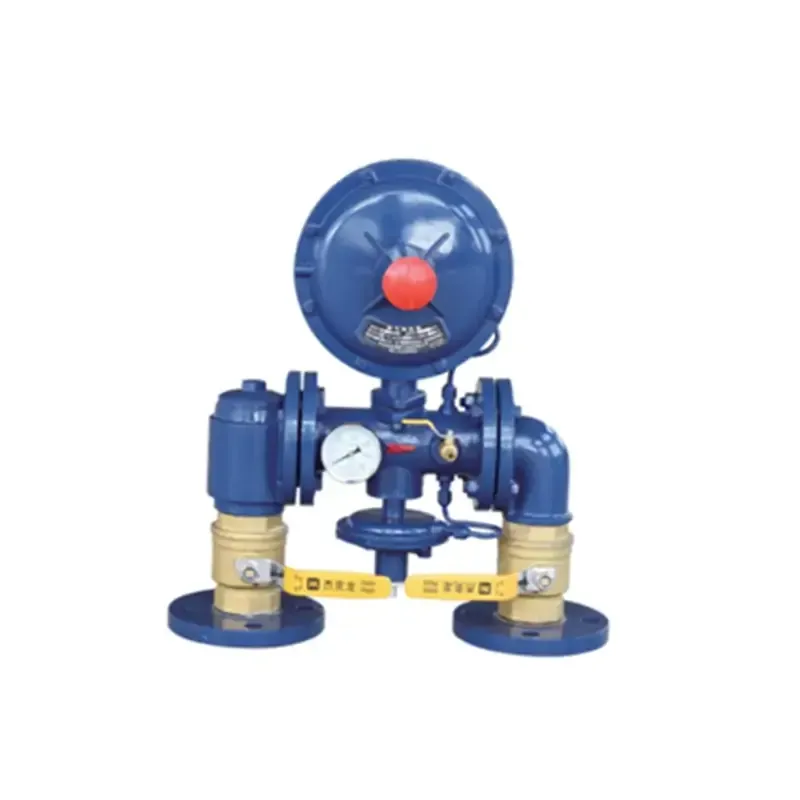
The world of electric valves encompasses a variety of types, each tailored to specific needs. Among the most common are ball valves,
butterfly valves, and gate valves. Ball valves are known for their durability and excellent shutoff capabilities. They are cost-effective solutions for on/off control without pressure drop. Butterfly valves, on the other hand, are used where space is limited and rapid response is required. They are designed for throttling service and moderate pressure and temperature drops. Gate valves are primarily chosen for their low-pressure drop and ability to cut through liquids.
Choosing the right electric valve involves more than just understanding the type. It requires insight into the material compatibility, pressure ratings, and temperature considerations of the specific application. Materials like stainless steel, brass, and plastic each have unique properties that make them ideal for particular uses. Stainless steel offers corrosion resistance, making it suitable for harsh environments, while brass is often selected for its machinability and lower cost. Plastic valves are lightweight and resistant to various chemicals, making them ideal for chemical industries.
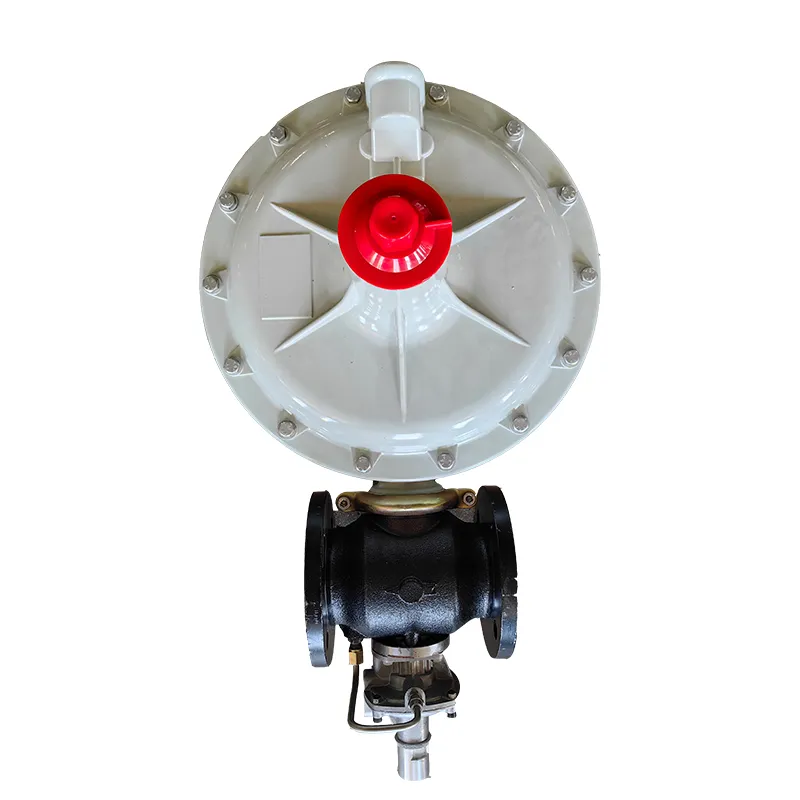
Installation and maintenance contribute significantly to the reliability of electric valves. Proper installation ensures that the valve functions as intended, reducing the risk of malfunction and extending its lifespan. Understanding the installation process involves knowing aspects such as flow direction, mounting position, and environmental considerations. Regular maintenance, including lubrication, inspection, and cleaning, can prevent common issues such as leaks, corrosion, and electrical failures.
electric valve
As an authority in electric valve systems, one must emphasize the impact of technological advancements on their operation. Smart electric valves equipped with sensors and IoT capabilities are revolutionizing how industries manage fluid control. These advanced systems provide real-time data on valve performance, enabling predictive maintenance and reducing downtime. By integrating such technologies, businesses can optimize their processes, improve safety, and reduce operating costs.
Trust in electric valve systems also hinges on adherence to industry standards and regulations. Compliance with standards such as ISO, ANSI, and API ensures that valves meet quality and safety benchmarks. Proper certification not only boosts customer confidence but also aligns operations with international best practices.
In summary, the realm of electric valves is vast and complex, demanding a blend of experience, expertise, authoritativeness, and trustworthiness to navigate effectively. Selecting the appropriate valve requires a comprehensive understanding of the application, material compatibility, and technological advancements. By maintaining rigorous installation and maintenance protocols, and adhering to industry standards, companies can ensure that their electric valve systems operate efficiently and reliably, ultimately contributing to enhanced industrial operations and productivity. Through this lens, electric valves not only represent a critical component of fluid control but also a testament to the advancements in engineering and technology.