Filter separators stand as essential components in various industrial applications, ensuring the removal of unwanted particulates and liquids from gases and liquids. Their multifunctionality makes them pivotal in maintaining the efficiency and longevity of industrial equipment while safeguarding product quality. When talking about filter separators, understanding their design, application, and benefits is crucial for any professional or business seeking to optimize fluid and gas processing systems.
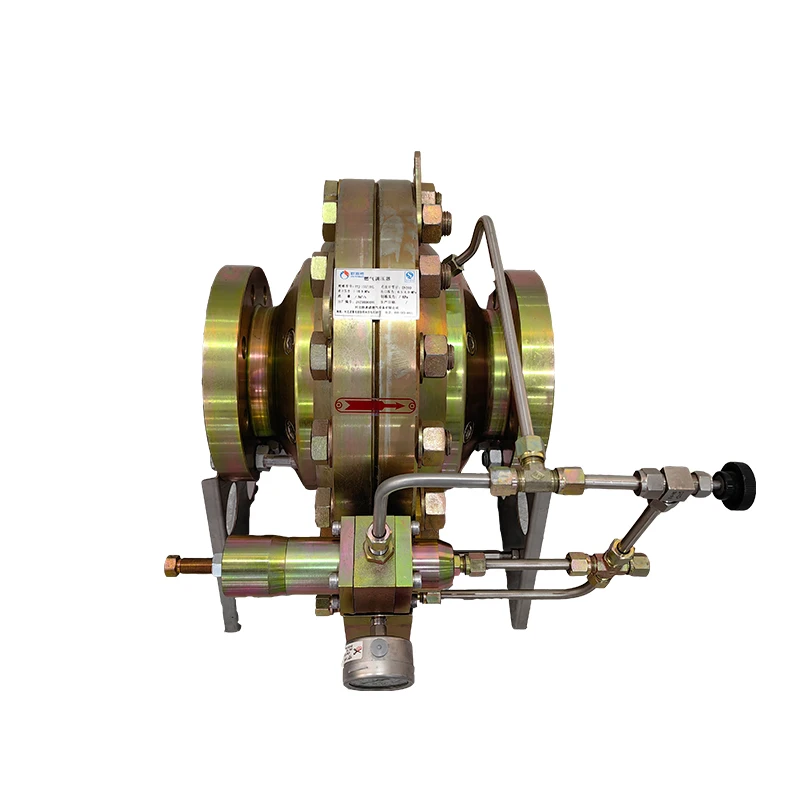
Experience reveals that filter separators are invaluable in industries such as oil and gas refining, petrochemical production, and even non-industrial applications like HVAC systems. The primary function of a filter separator is to extract any contaminant from flowing liquids or gases, rendering them clean and efficient for further processing or usage. This involves various separation techniques including centrifugation, gravity separation, and filtration.
With a proven track record, these units are versatile, handling a range of particle sizes and types, from sediments to oily residues. In an oil refinery, for instance, filter separators are employed to extract water and particulates from hydrocarbon streams, preventing equipment corrosion and pipeline blockages. For HVAC systems, they are crucial in maintaining air quality by trapping dust and allergens, thereby improving the air purity within buildings.
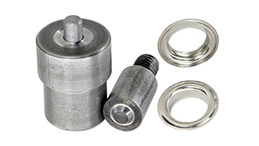
Expertise in the use of filter separators is critical for customization according to the specific needs of an industry. Engineers who specialize in fluid dynamics and filtration technology are pivotal in the design and optimization of filter separator systems. Tailoring the design involves selecting appropriate materials, determining optimal flow rates, and configuration of separator stages to ensure maximum efficiency and reliability.
Typically, filter separators are composed of two key sections the filtration section and the separation section. The filtration section is responsible for the initial removal of coarser particles from the fluid or gas stream. This is followed by the separation section, which finely removes smaller particulates and any residual liquids. These dual stages ensure that the output meets stringent industrial quality and safety standards.
Manufacturer authoritativeness is also a critical consideration. Leading manufacturers with decades of experience in producing filter separators provide the assurance of quality and reliability. They incorporate cutting-edge technology and have a comprehensive understanding of regulatory compliance standards worldwide. This ensures that the separators not only perform optimally but also meet safety and environmental guidelines.
filter separator
Ensuring trustworthiness involves delivering products that consistently perform under specified conditions. Customers are increasingly looking for transparency regarding the capabilities and limitations of filter separators. Trusted manufacturers often provide detailed product testing data, independent certification, and customer testimonials to reinforce product confidence. With a track record verified through peer-reviewed studies and industry benchmarks, these companies can provide a quality guarantee.
It is essential for businesses to engage with certified technicians for installation and maintenance of filter separators to ensure the system operates as intended. Proper maintenance routines are key to preventing downtime, sustaining performance levels, and extending the lifespan of the equipment.
As industries continue to evolve, there is a growing emphasis on sustainable practices. Modern filter separators are designed to be environmentally friendly by minimizing waste and energy consumption. Innovations such as self-cleaning mechanisms and materials that offer longer service life reduce the operational costs and environmental impact, appealing to businesses committed to corporate social responsibility.
In summary, filter separators are indispensable in maintaining the purity and efficiency of industrial processes. The integration of advanced technology, coupled with expert design and reliable manufacturing, makes them a trustworthy choice for industries looking to optimize their processing systems. By choosing a robust filter separator, businesses can ensure operational efficiency, equipment longevity, and adherence to environmental standards, ultimately leading to enhanced performance and profitability.
Investing in a quality filter separator is not just about meeting immediate operational needs but also about securing a sustainable future in industrial processing, making it a vital component for any forward-thinking company.