Pneumatic valves are integral components in many industrial applications, renowned for their efficiency and reliability. For those unfamiliar with these devices, they regulate the flow and pressure of air or gas within a system, serving as a switch to control the distribution and release of energy. With applications ranging from manufacturing to energy sectors, understanding the intricacies of pneumatic valves, as well as the best ways to utilize them, is essential for optimizing operational performance.
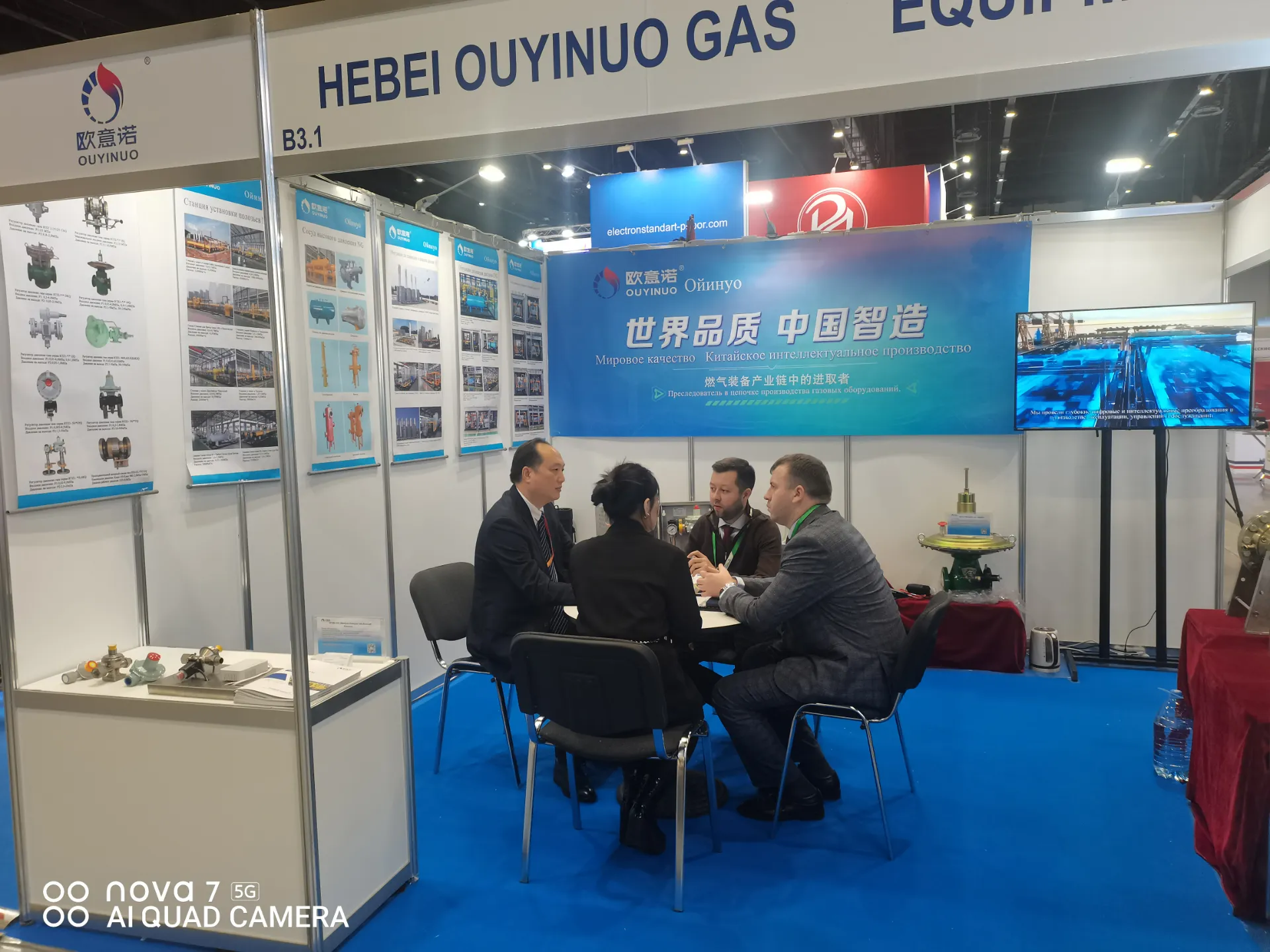
Real-world experience demonstrates the significance of selecting the right type of pneumatic valve for specific applications.
Imagine an automated assembly line where precision and timing are paramount. Utilizing a high-speed pneumatic valve can drastically reduce the delay in response time, ensuring each segment of the line operates in seamless harmony. The importance of purchasing from reputable suppliers cannot be overstated, as it directly impacts the durability and performance of the valves in high-stress environments.
Expertise in this field underscores the variety of pneumatic valves available, each tailored to specific functions and industries. For instance, a diaphragm valve is optimal for applications requiring tight leakage control and the capability to handle aggressive chemicals. Professionals often emphasize how a thorough assessment of the medium, temperature, and necessary flow rate can guide the selection process, ensuring not only efficiency but also safety in applications where hazardous materials are present.
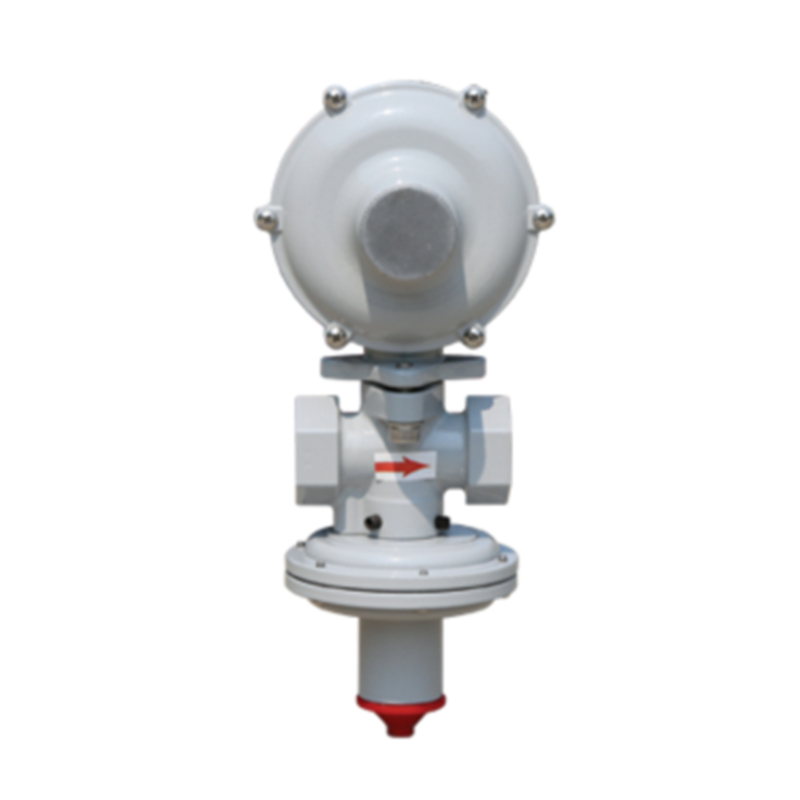
The authoritative perspective on pneumatic valves focuses on their versatility and robust construction, particularly in energy generation and resource management scenarios. Industries reliant on compressed air systems often employ three-way valves for their ability to manage air streams effectively, which can be critical in minimizing energy wastage and enhancing overall system performance. Research and case studies consistently showcase how innovative pneumatic valve solutions contribute to sustainability efforts by reducing the carbon footprint of industrial operations.
pneumatic valve
Trustworthiness is paramount when it comes to maintaining and operating pneumatic valves. Regular maintenance ensures the longevity and reliability of these components. A trusted provider often offers detailed guides and support for maintenance practices, reinforcing the optimal performance of pneumatic systems. It's advisable to engage in predictive maintenance strategies, which utilize sensor data to forecast potential failures before they occur, thereby minimizing downtime and maintaining operational integrity.
Detailed product knowledge extends to understanding actuator mechanisms, which play a crucial role in the operation of pneumatic valves. Whether it’s a single-acting or double-acting actuator, each possesses distinct benefits depending on the application scenario. Engaging with knowledgeable industry experts can provide insights into which actuator is best suited for your specific needs.
Furthermore, the advent of smart technology has revolutionized the pneumatic valve landscape, integrating digital capabilities with traditional pneumatic systems. These advanced systems allow for remote monitoring and real-time data analytics, offering operators unprecedented control and insight into valve operations. This technological enhancement not only improves efficiency and reduces errors but also aligns with modern industry standards for digital transformation.
In conclusion, pneumatic valves are indispensable to many industrial applications, offering reliability and efficiency across various sectors. A deep understanding of the types and functionalities, coupled with a commitment to regular maintenance and the embrace of smart technologies, can significantly enhance operational performance. By prioritizing experience, expertise, authoritativeness, and trustworthiness, businesses can leverage pneumatic valves to achieve both operational excellence and sustainability goals.