Relief valves, often considered the unsung heroes of fluid systems, play a critical role in ensuring the safe and efficient operation of various industries. These indispensable components are not merely supplementary; they are essential in preventing catastrophic failures, maintaining pressure equilibrium, and safeguarding expensive equipment from potential damage. Their significance extends across multiple domains, including chemical processing, oil and gas, water treatment, and even residential plumbing.

Understanding the nature and operation of relief valves is pivotal for anyone involved in industries that rely heavily on pressurized systems. These devices are designed to release a defined amount of fluid once a predetermined pressure is exceeded, thus keeping the system operating within safe limits. A relief valve, therefore, ensures that the pressure does not reach a point where it could cause pipes to burst or equipment to fail.
Selecting the right relief valve is an exercise that requires a deep understanding of not just the valve itself, but the system it will protect. Factors such as the type of fluid, the regular operating pressure, and the worst-case scenario pressure must be meticulously considered. For instance, valves used in steam systems are vastly different from those employed in gas pipelines. Each environment demands specific construction materials and operational mechanisms to meet safety standards.
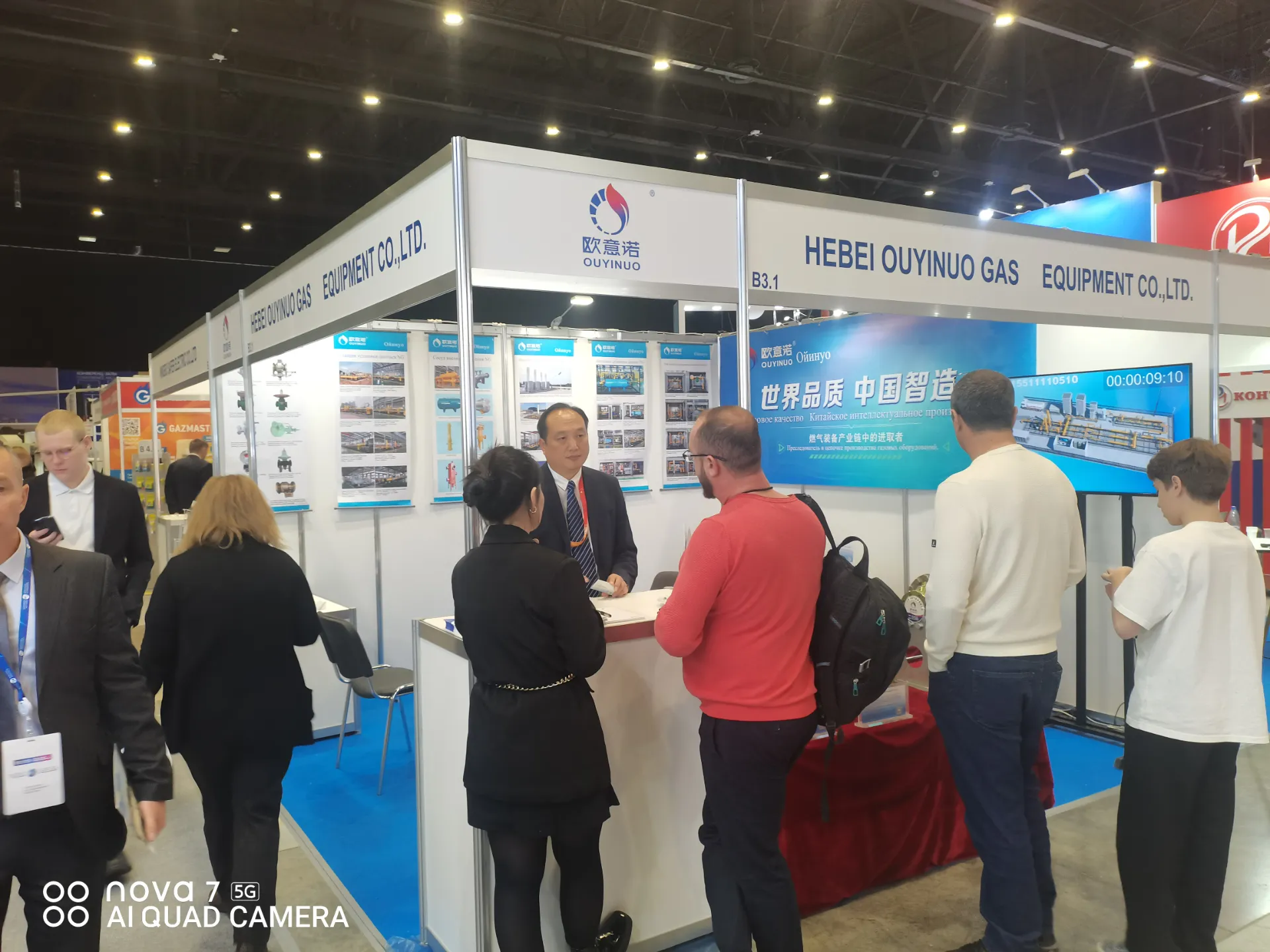
One of the key advancements in relief valve technology is the use of advanced materials that offer enhanced resistance to corrosion and wear. Stainless steel remains a popular choice given its durability and resilience against corrosive substances. Innovative materials, such as hastelloy and monel, provide superior withstand capabilities in environments with extreme temperature fluctuations and aggressive media. These advancements have extended the lifespan of relief valves, reducing both the frequency of maintenance and the risk of unexpected failure.
Another pivotal aspect is the rise of digital monitoring systems integrated with relief valves. By maintaining real-time data analytics and predictive maintenance schedules, digital systems can significantly enhance the overall reliability of pressure containment systems. They allow operators to track the performance and condition of relief valves, preemptively identifying issues that could lead to system failure. This level of oversight not only enhances safety but also promotes cost efficiency by minimizing downtime.
relief valves
Maintaining a regular inspection schedule is crucial for the optimal performance of relief valves. Adhering to regulatory requirements and following industry best practices assures that these valves operate as intended. Given that even the slightest malfunction could lead to dire consequences, there is little room for oversight. Regular calibration, visual inspections for any wear and tear, and testing to ensure valves open and close at the correct pressure levels are part of a comprehensive maintenance routine. Engaging with certified professionals who possess a profound understanding of pressure systems is advisable to execute these tasks.
Trustworthiness in relief valve performance is non-negotiable. Given that these valves are practically the last line of defense against uncontrolled pressure build-ups, selecting a manufacturer with a proven track record of reliability and compliance with international standards is vital. Companies with ISO certifications or adherence to the American Society of Mechanical Engineers (ASME) guidelines should be prioritized. These accreditations confirm that the products have undergone rigorous testing and meet stringent quality benchmarks.
In terms of real-world applicability, companies that have invested in state-of-the-art relief valve technology have reported a tangible return on investment. Not only do they benefit from enhanced safety and compliance but also reduced insurance costs and increased operation efficiency. Innovations in valve technology have allowed industries to achieve seamless integration into their systems, effectively reducing the possibility of human error.
In conclusion, the strategic selection, maintenance, and integration of relief valves into pressure systems are as important as any other process in industries that manage high-pressure environments. By ensuring safety and operational efficiency, these components are crucial to the longevity and success of modern industrial practices. The ongoing advancements in relief valve technology promise even greater reliability and cost-effectiveness, underscoring their indispensable role in an increasingly complex industrial landscape.