Choosing the Right Safety Relief Valve for Your Industrial Application
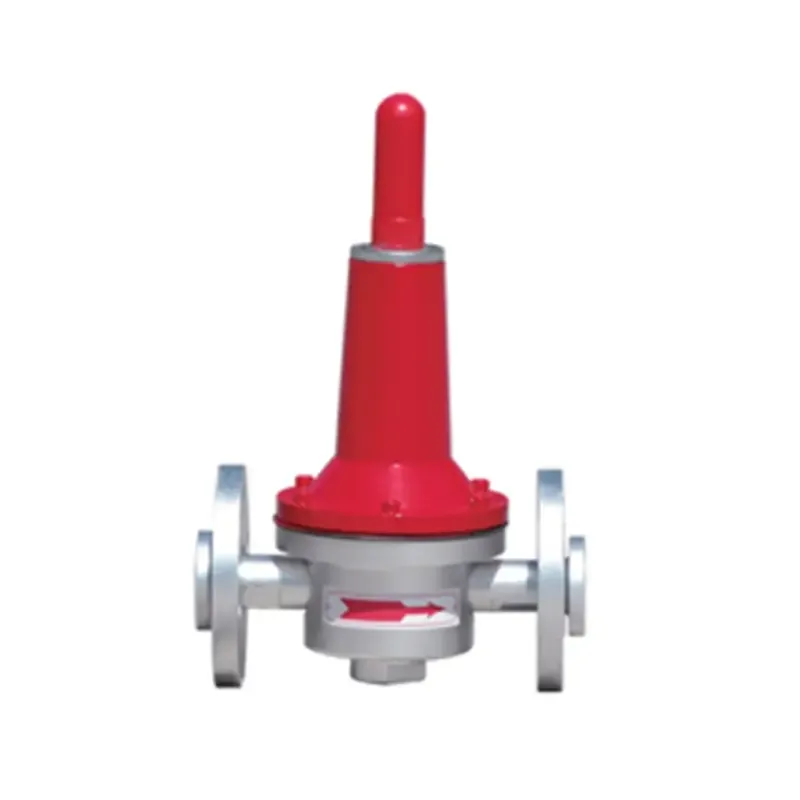
Safety relief valves are indispensable components in industrial systems, designed to protect against overpressure and ensure safe operation. As an industrial component with critical importance, selecting the right safety relief valve requires a comprehensive understanding of its functions, types, and the specific needs of your system.
Industrial Applications and Importance
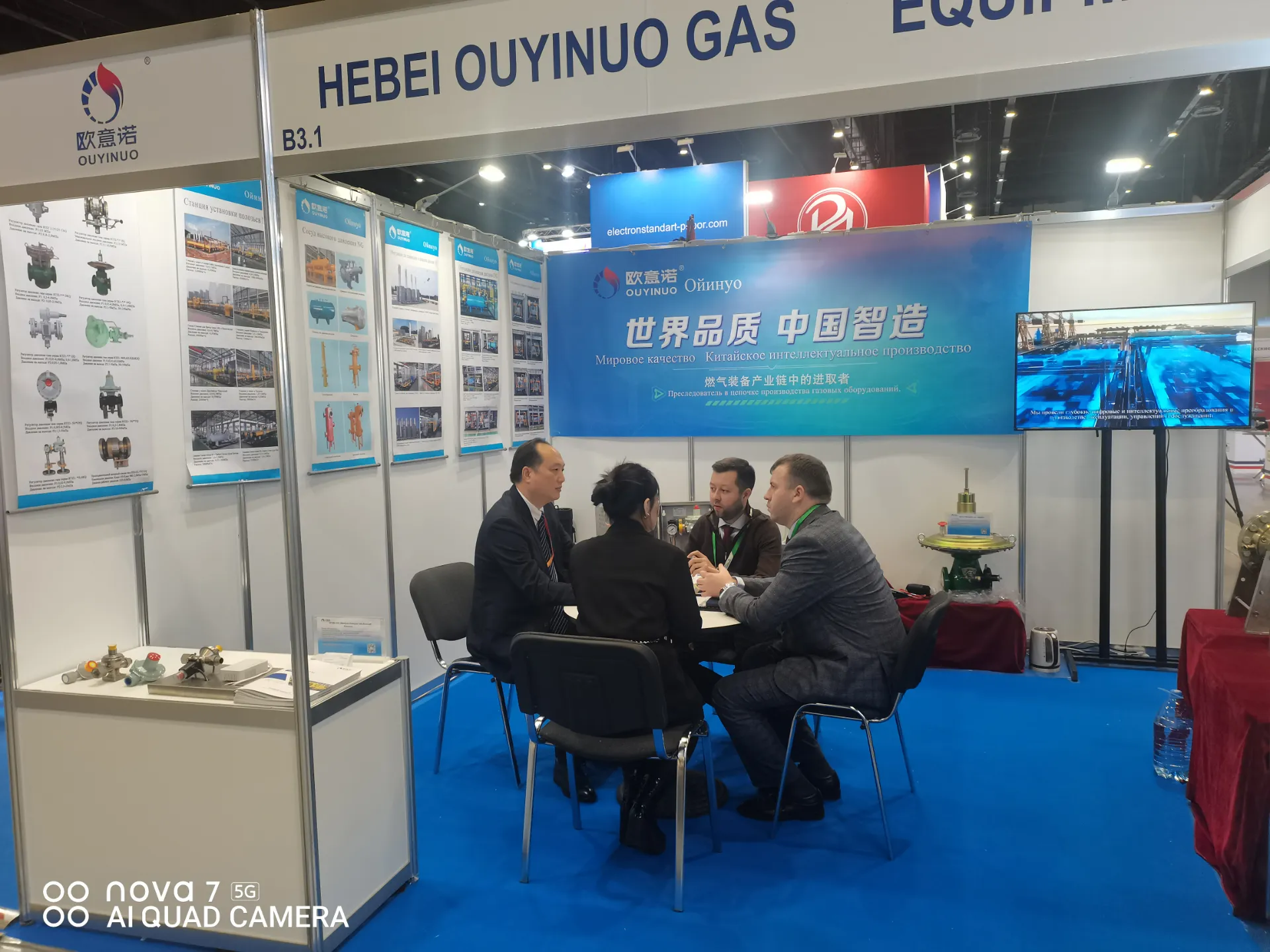
Safety relief valves safeguard systems by releasing excess pressure, preventing potential hazards such as system failures or explosions. In sectors like oil and gas, petrochemicals, manufacturing, or power generation, having a properly functioning safety relief valve can mean the difference between smooth operations and catastrophic failure. These valves are crucial in maintaining operational integrity and safeguarding both personnel and equipment.
Understanding Different Types of Safety Relief Valves
There are several types of safety relief valves available, and choosing the right one depends on the specific requirements of your system. The most common types include direct spring-loaded, pilot-operated, and balanced bellows valves.
Direct spring-loaded valves are simple and cost-effective, ideal for systems where the relief scenarios are not frequent. Pilot-operated valves, meanwhile, are suited for high-pressure applications providing more precise control and tighter sealing. For situations where backpressure might impact valve performance, balanced bellows valves can deliver reliable operation without performance degradation.
Assessing Your System's Requirements
Having an intimate understanding of your system's operational parameters is vital. Variables such as operating pressure, temperature, type of fluid (liquid, gas, or vapor), and the frequency of pressure relief events are key determinants. It's essential to ensure that the material of the valve is compatible with the fluid, taking into account factors like chemical resistance and temperature resilience.
Moreover,
consider the location of the valve installation. Different environmental conditions such as exposure to extreme weather, risk of corrosion, or physical impact might necessitate specific materials or additional protective features.
safety relief valve
Ensuring Compliance to Standards
For trustworthiness and authority, ensure the valve complies with relevant industry standards such as ASME (American Society of Mechanical Engineers) or API (American Petroleum Institute) standards. Compliance certificates and marks provide assurance of quality and adherence to safety protocols.
Opt for valves from reputable manufacturers known for reliability and technological innovation. Companies with a track record for industry excellence not only offer superior products but also provide technical support and after-sales service.
Installation and Maintenance
The installation of a safety relief valve should be performed by experienced professionals who understand the nuances of the specific valve type and system architecture. Proper installation is crucial for the valve's effectiveness and the system's safety.
Regular maintenance and testing ensure longevity and reliability. Scheduled inspections can preemptively identify wear and tear or operational anomalies, enabling timely interventions. Employ industry best practices and standards for maintenance routines to sustain operational efficiency.
Cost Considerations
While cost is a significant factor, it should not eclipse the importance of reliability and safety. A lower-cost valve may translate into higher operational risks or maintenance costs over time. Evaluate the total cost of ownership, considering factors like initial cost, maintenance requirements, downtime costs, and life expectancy.
Conclusion
Incorporating the right safety relief valve into your system is both a strategic investment and a necessary safety measure. Through thorough evaluation of system requirements, careful selection of valve type, and ensuring compliance with industry standards, you safeguard not only the operational success of your system but also the safety of your employees and equipment. By prioritizing quality, reliability, and adherence to standards, your facility can operate with enhanced safety and confidence.