Ensuring the safety and reliability of industrial operations is a priority across various sectors, and the role of the safety valve is paramount to achieving this objective. Safety valves, often deemed as the last line of defense, serve critical functions in preventing catastrophic outcomes by releasing pressure that exceeds specified limits. Not only do they safeguard equipment, but they also play an essential role in protecting human life and the environment.
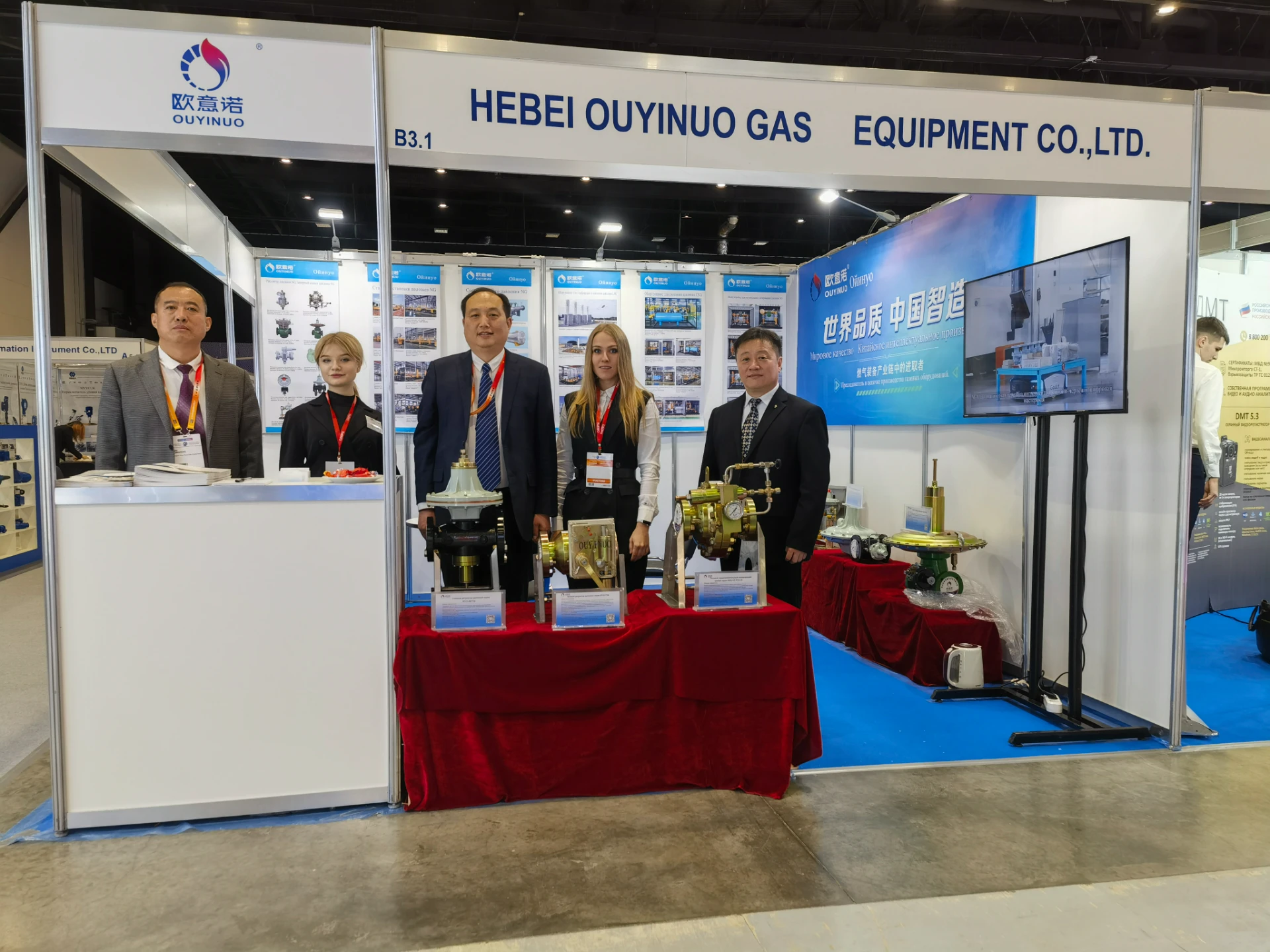
A seasoned engineer with decades of experience in industrial safety once remarked, A well-maintained safety valve is akin to a trusted sentinel that ensures operational peace. His words underscore the fundamental principle that these devices must be meticulously selected, installed, and maintained to provide the utmost protection and assurance. Experience shows that improper valve selection or maintenance can lead to dreadful consequences, including equipment failure, fire hazards, and environmental damage.
When exploring the technical expertise behind these devices, it becomes evident that the design, material selection, and operational parameters must align with specific industrial needs. For example, safety valves constructed from stainless steel are highly recommended in corrosive environments, while those made from carbon steel might suffice in less demanding settings. Understanding the intricacies of valve materials and designs is crucial for engineers aiming to optimize plant safety.
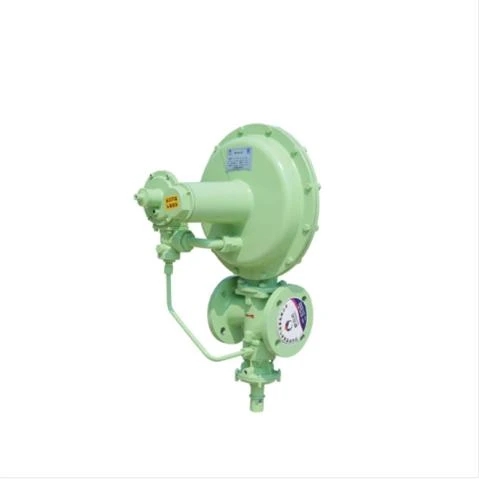
Authoritative guidelines and standards, such as those provided by the American Society of Mechanical Engineers (ASME) and the International Organization for Standardization (ISO), offer comprehensive insights into best practices for safety valve operation and maintenance.
These standards not only inform industry practices but also set benchmarks for compliance. Many industrial mishaps have been avoided by adhering to these guidelines, proving their pivotal role in establishing authoritative safety protocols.
safety valve
Trust, perhaps the most intangible yet vital aspect of safety valve management, is fostered through diligent quality assurance and testing. Regular inspections and simulations are necessary to ensure that safety valves perform accurately under critical conditions. Industries often partner with certified testing agencies to evaluate the valves, ensuring that they meet or exceed operational expectations. This level of scrutiny builds confidence, both within an organization's workforce and among external stakeholders.
Real-world applications further illustrate the necessity of high-quality safety valves. In chemical processing plants, for instance, the release of hazardous gases due to valve malfunction can have dire consequences. A plant operator shared a testament to regular safety valve inspections, recounting an incident where a potential gas leak was averted, thus preventing what could have been a significant disaster. Such experiences highlight the interconnected nature of expertise, authoritative practice, and trust in establishing failproof safety measures.
In conclusion, the effectiveness of safety valves is anchored in a synergy of experience, technical expertise, adherence to authoritative standards, and an unwavering commitment to trust and reliability. As industries continue to evolve, the innovation in safety valve technology must keep pace, always prioritizing protection and assurance. For entities seeking to bolster their safety protocols, understanding and investing in high-quality safety valves is not just advisable, it is essential.