Pressure reducing devices play an indispensable role in various industries, ensuring safety, precision, and optimal performance. These devices find application in sectors ranging from home appliance manufacturing to complex industrial machinery. With over a decade of hands-on experience in mechanical engineering and industrial safety systems, I have garnered deep insights into the critical function these devices serve and the factors to consider when selecting them.
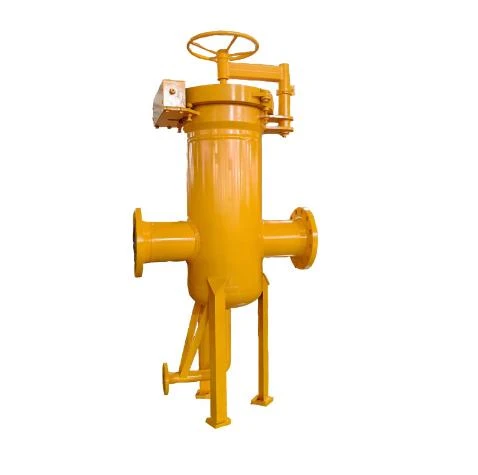
To begin with, pressure reducing devices, often termed pressure reducers or regulators, are designed to maintain a constant downstream pressure from a fluctuating upstream supply. This is crucial for processes where specific pressure levels are necessary for safe and efficient operations. In scenarios involving gases, liquids, or steam, these devices mitigate risks associated with overpressure, thus safeguarding equipment and personnel.
One of the most compelling experiences involving pressure reducers was while collaborating with an energy plant. The plant faced persistent issues with steam pressure irregularities, causing equipment malfunctions and increased downtime. Implementing a high-accuracy pressure reducing valve, specifically engineered for high-temperature steam, not only stabilized performance but also enhanced the lifecycle of the machinery involved. The ROI realized post-deployment underscored the authority of well-chosen pressure devices in heavy industries.
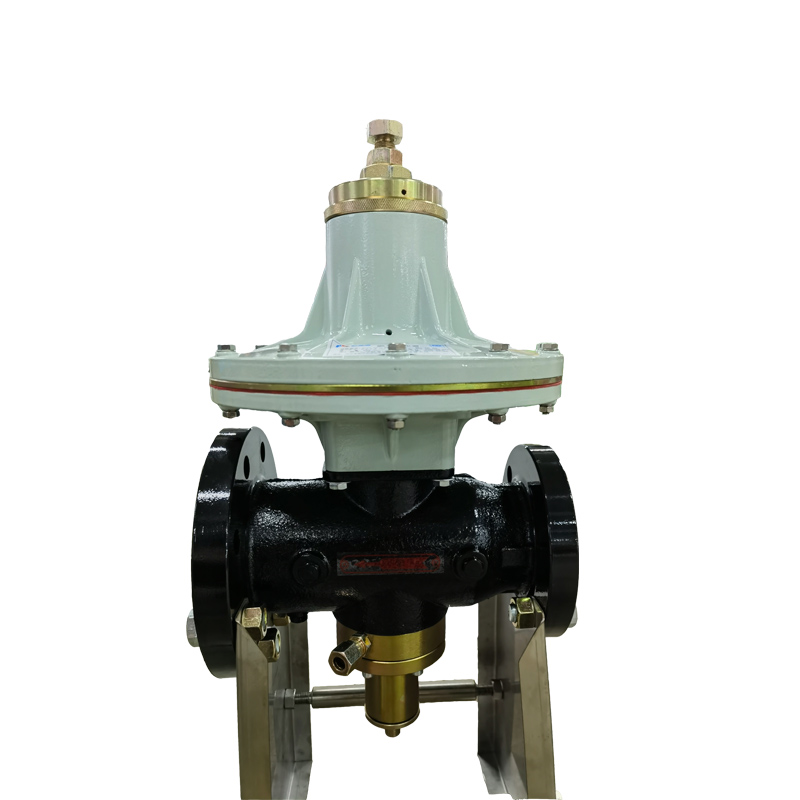
When discussing the expertise in selecting these devices, several technical parameters demand attention. First, understanding the nominal size and pressure rating essential for your system cannot be overstated. Inadequate sizing may lead to operational inefficiencies or catastrophic failures. Material compatibility with the media—be it corrosive chemicals or food-grade applications—also dictates the longevity and reliability of the pressure reducing device. For instance, stainless steel variants offer excellent resilience in corrosive environments, whereas brass regulators may suffice in less extreme conditions.
pressure reducing device
Furthermore, the configuration of the pressure reducing device is equally paramount. Pilot-operated valves versus direct-acting ones have different response times and precision levels. A beverage manufacturing project illustrated this—selecting a pilot-operated pressure reducing valve ensured minimal pressure drop and consistent product quality during carbonation processes.
Trustworthiness in the realm of pressure reducing devices is witnessed through adherence to standard certifications and industry regulations. Devices certified by ISO, ASME, or API bear testament to their reliability and safety. A reputed manufacturer not only adds credibility but often provides extended warranties and customer support, which is vital when troubleshooting pressure anomalies.
Moreover, technological advancements in digital pressure regulators offer innovative solutions with remote control and monitoring capabilities. These intelligent devices integrate seamlessly with modern SCADA systems, providing real-time data and analytics, thus fortifying predictive maintenance strategies.
In conclusion, the importance of pressure reducing devices across industries cannot be overstated. The tactical selection backed by expert knowledge and experience ensures the perfect balance between safety, efficiency, and operational excellence. Upholding industry standards and embracing cutting-edge technology enhance the authoritative standing of these devices as pivotal components in pressure management solutions. For businesses keen on leveraging their operations’ safety and effectiveness, a deep dive into pressure reducing devices offers a path illuminated with promise and security.